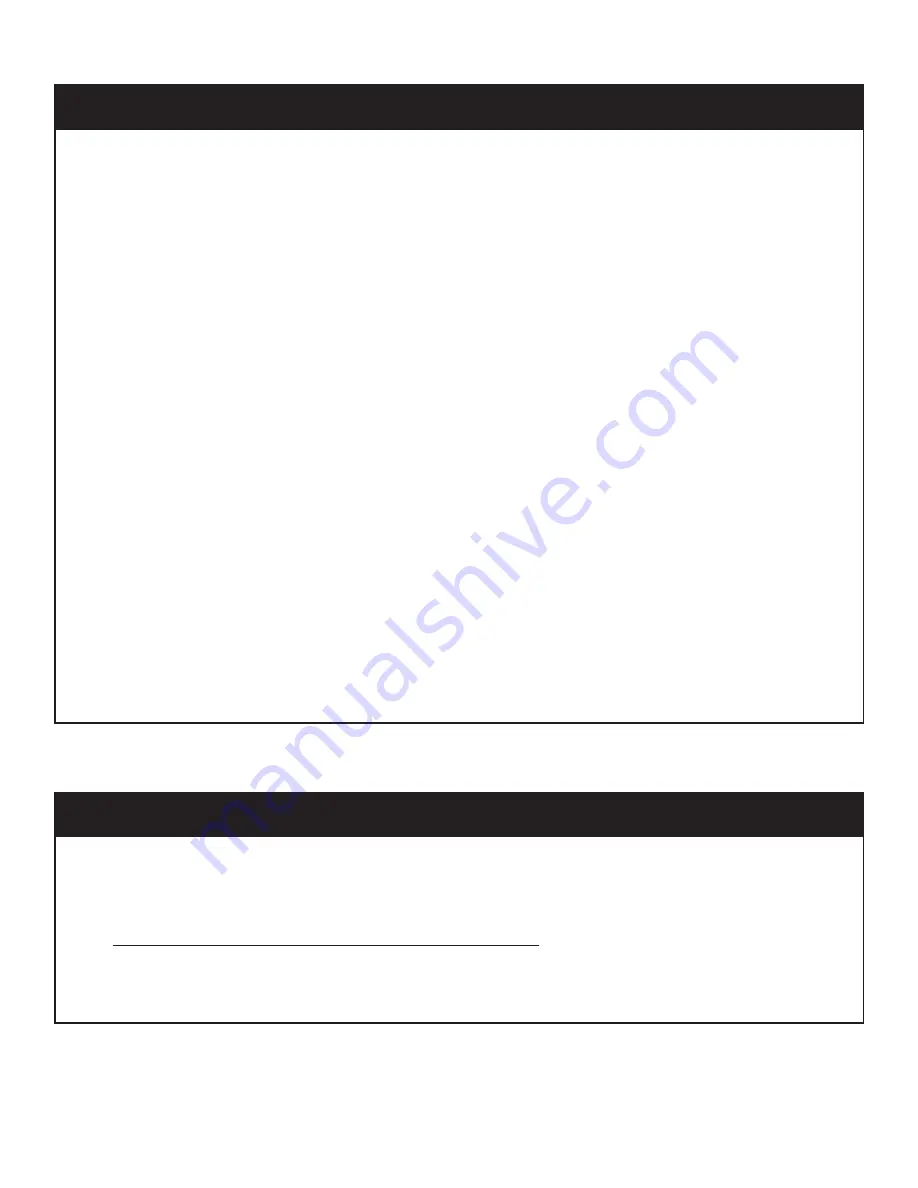
14
6. Piping The Boiler
All piping must conform to state and local codes. Page 11 shows the location
and size of the boiler tappings. It is recommended to install unions and gate valves at
the inlet and outlet of the boiler, so it may be readily isolated for service.
A low water cut off is required if the boiler is installed above the level of radiation.
Even if the boiler is installed below the level of radiation it is strongly recommended
that a low water cut off be installed. Install manual and/or automatic air venting
devices at the high points in the system to eliminate trapped air. The weight of all
piping should be supported by suitable hangers and floor stands, not by the boiler’s
purging/expansion station. Clearance for hot water pipes are 1 inch to combustibles.
The make-up water line must be piped into the boiler and be fitted with a backflow
preventer and a pressure reducing valve to reduce line pressure to 10 to 15 psi.
In the case of a gas installation, the boiler should be installed such that the gas
ignition system components are protected from water (dripping, spraying, etc.) during
appliance operation and service (circulator replacement, condensate trap, control
replacement, etc.).
If the boiler is to be used in conjunction with a chilled water system, it must be
piped with the appropriate valves to ensure the chilled medium does not enter the
boiler. If the boiler is connected to heating coils in an air handling system, where the
coils could be exposed to cold air circulation, provisions for freeze protection control
must be installed. The boiler must have flow control valves or other automatic means
to prevent gravity circulation of the boiler water during the cooling cycle.
NOTE: If the heating system is to be filled with antifreeze, use only formulations
expressly made for hydronic heating systems (such as propylene glycol). Do not use
automotive types of antifreeze (ethylene glycol). Use of antifreeze will alter system
output and characteristics. Consult a factory representative for details or assistance.
SAFETY RELIEF VALVE
1. The safety relief valve should be piped into one of the two upper 3/4” tapings in
the rear of the boiler
2. The relief valve should be installed using the hardware supplied in the trim kit
without valving between the PRV and the boiler.
3. Pipe the discharge for the safety relief valve with copper tube to within 4” from the
floor and make sure installation of the pipe conforms to local codes.