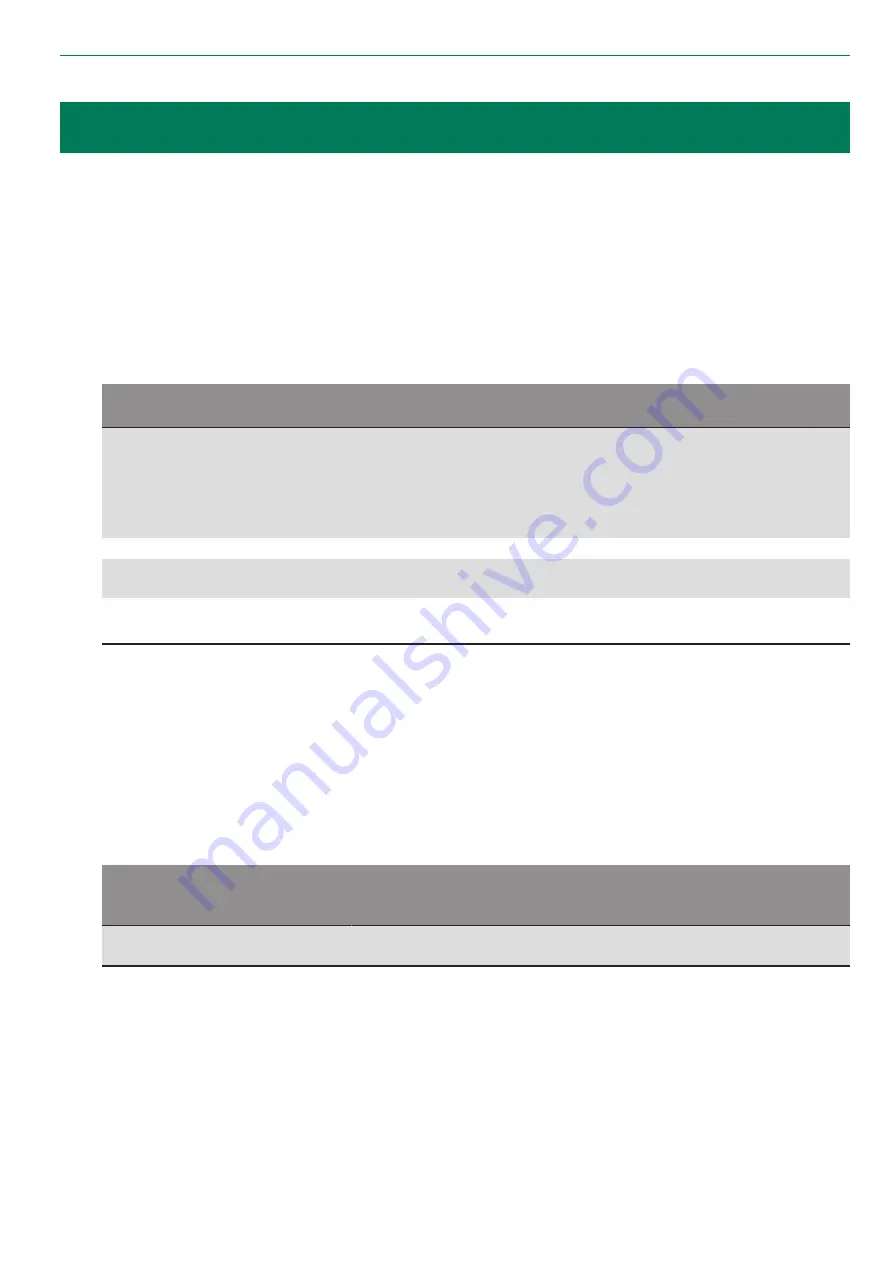
GFA-OOT
EN
Service
© Saltus Industrial Technique AB - 9839 1814 01
9
Service
Service Overview
As the gear wheels of the GFA module are exposed to hard wear it is important to regularly check their
condition. If any of the gear wheels are worn or damaged, all the gear wheels must be replaced. Needle
bearings are to be replaced if needed.
At regular intervals between the service, additional grease is to be supplied through the grease nipples.
Maintenance Instructions
Service Intervals and Actions
Interval
Action
Daily
■
Clean the GFA system
■
Inspect the system for any damage
■
Check all fastenings of the system
■
Run functional tests and listen for any abnormal
noise
At least after every 30,000 tightenings
■
Lubricate the system
At least after every 250,000 tightenings
■
Service interval for overhaul and preventive main-
tenance
In case of wear-out parts or in case of faulty tightening
result
■
Change the output socket gear
■
Change the wear-out parts
Preventive Maintenance
Cleaning the System
To clean the system, wipe carefully with a clean, smooth cloth.
Lubrication Instructions
Lubrication Instructions
Component
Recommended
Lubricant
Quantity
GFA module
Molykote Longterm 2 Plus
Until excess grease emerges on
the output socket
Summary of Contents for GFA-OOT
Page 2: ...2 Saltus Industrial Technique AB 9839 1814 01 Table of Contents EN Product Instructions 3...
Page 11: ...GFA OOT EN Service Saltus Industrial Technique AB 9839 1814 01 11...
Page 13: ...GFA OOT EN Service Saltus Industrial Technique AB 9839 1814 01 13...
Page 18: ...Service EN GFA OOT 18 Saltus Industrial Technique AB 9839 1814 01...