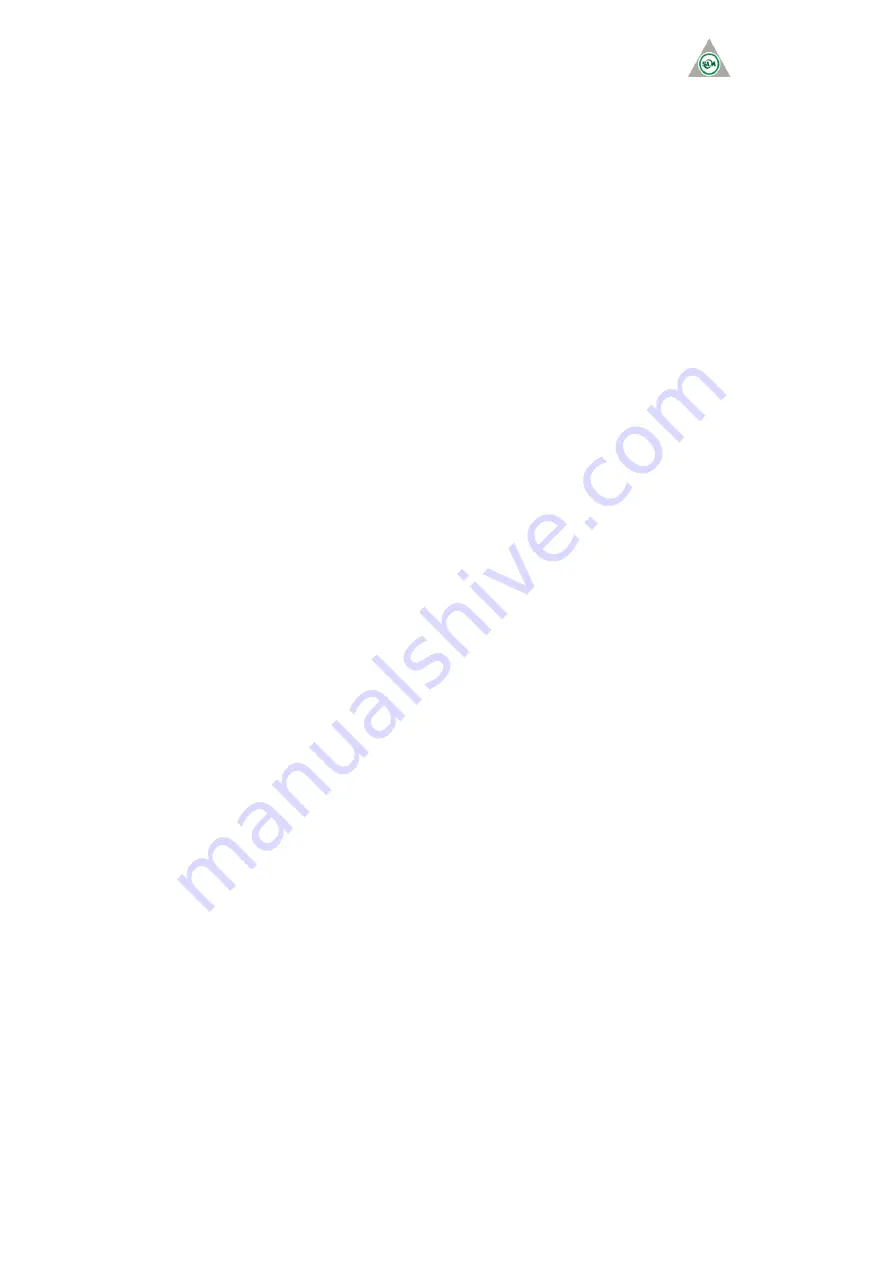
Generally the suction line is larger than the pump suction nozzle, and
eccentric reducers should be used. Eccentric reducers are not necessary for
bottom suction pumps.
If the liquid supply is located below the pump centre line, the reducer should
be installed with the straight side up. Most often air enters the suction pipe
entrained in the liquid. Installations with a static suction lift preferably should
have the inlet of the vertical suction piping submerged in the liquid to four
times the piping diameter.
A large suction pipe will usually prevent the formation of vortexes or
whirlpools, especially if the entrance is flared. A floating vortex breaker (raft)
around the suction piping may be provided if a tendency appears for a vortex
to form at the liquid surface.
A stream of liquid falling into the sump near the intake pipe will churn air into
the liquid. The supply line should extend down into the sump. Liquid supply
entering a well perpendicular to the intake line tends to rotate the liquid, which
interferes with the flow into the suction line. A baffle placed in front of the
supply pipe will remedy this situation. A short elbow should never to bolted
directly to the pumps suction nozzle.
The disturbance in the flow caused by the sharp bend so near the pump inlet
may result in noisy operation, loss in efficiency, and capacity, and heavy end
thrust. A long sweep or long radius elbow placed as far away from the pump
as practicable should be used if a bend is necessary in the suction line. If
separate suction lines cannot be used for each pump, then a tapering header
with Y-branches should be used.
A straight branch header should never be used. Prior to installing the pump,
suction piping and pump should be inspected internally, cleaned and flushed.
If a strainer is installed in the suction line, the openings in the screen must be
checked and cleaned periodically. The opening must be smaller than the
sphere size allowed by the impeller.The flow velocity in the suction pipe should
be 1.5 to 2.5 mts /sec., for normal cases, but should not exceed 3 mts /sec
Discharge piping should be installed with check valve and gate valve, with the
check valve being between the pump and the gate valve. The check valve
prevents reverse flow and protects the pump from excessive backpressure.
The gate valve is used to isolate the pump for maintenance, priming and
starting.
Cleaning the piping and Suction Pit ;
After the piping has been
installed, it should be cleaned and emptied of welding waste, welding rod ends
and other foreign material. Likewise, the suction pit should be thoroughly
cleaned of all loose rubbis
Summary of Contents for ZM 375/00
Page 7: ......
Page 20: ...20 ZM II 630 03 ...