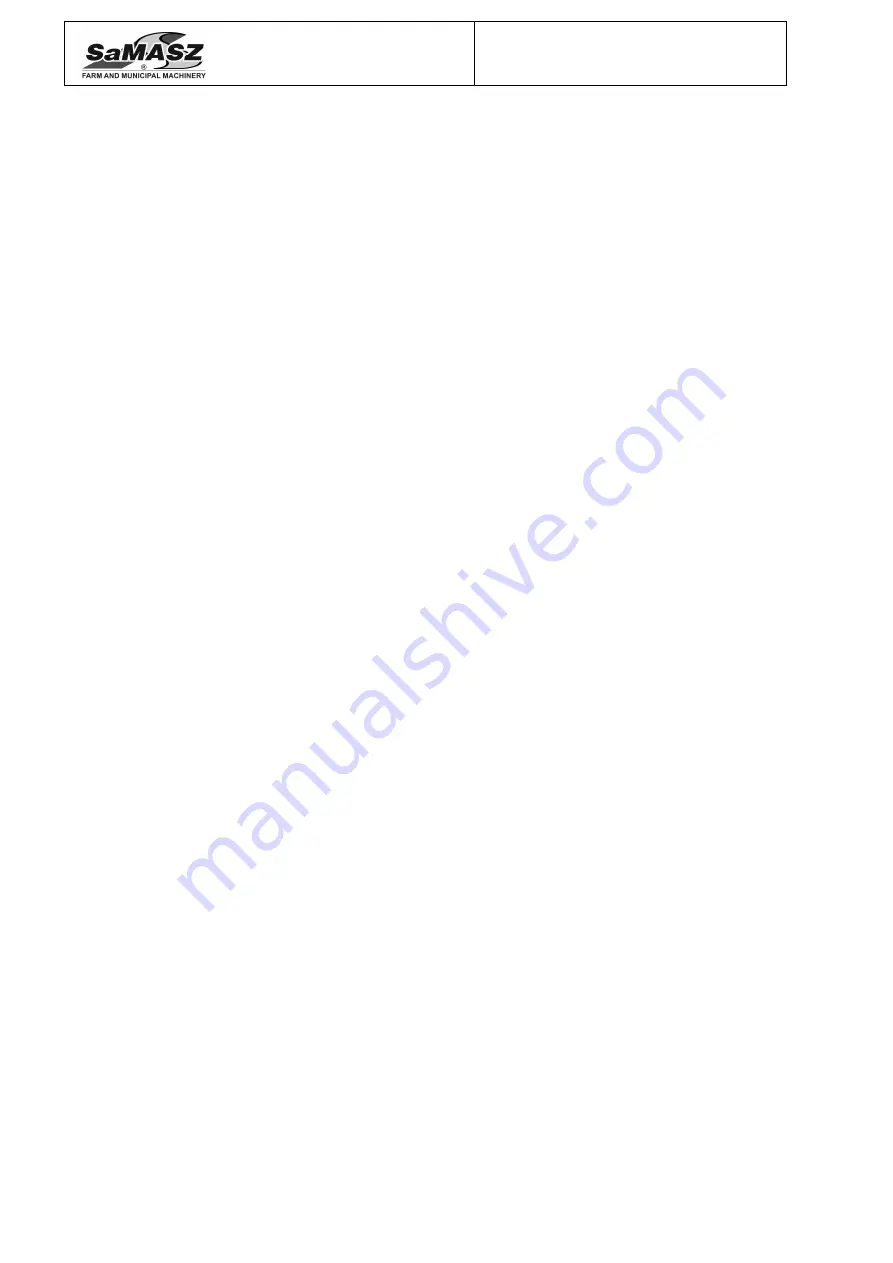
Operator’s manual
Double-sided disc mowers
with central suspension
- 2 -
6.4.
Adjusting conditioner............................................................................................................. 40
6.4.1.
Adjusting space between tine conditioner’s mask and its shaft ...................................... 40
6.4.2.
Adjusting conditioner's shaft rpm ................................................................................... 41
6.5.
Replacing conditioner’s tines ................................................................................................. 42
6.6.
Adjusting force of the pressure of roller conditioner ............................................................. 43
6.7.
Maintenance and service ........................................................................................................ 43
6.7.1.
Checking the knives and knife holders ........................................................................... 43
6.7.2.
Checking the tension of tine and roller conditioners’ driving chain ............................... 44
6.7.3.
Daily maintenance .......................................................................................................... 44
6.7.4.
After-season maintenance and storing of machine ......................................................... 45
6.8.
Conveyor control and adjustment .......................................................................................... 45
6.8.1.
Cleaning belts and rollers ............................................................................................... 45
6.8.2.
Conveyor belt replacement and adjustment instruction .................................................. 46
7.
LUBRICATION .................................................................................................. 48
7.1.
Cutterbar ................................................................................................................................ 48
7.2.
Intersecting axis gears ............................................................................................................ 49
7.3.
Roller conditioner’s gearbox.................................................................................................. 50
7.4.
Chain drives of the roller and the scarifier ............................................................................. 50
7.5.
Lubrication points .................................................................................................................. 51
8.
MALFUNCTION AND THEIR REPAIRS ...................................................... 52
9.
DISASSEMBLY AND WITHDRAWAL FROM USE .................................... 53
9.1 Scrapping ................................................................................................................................ 53
10.
WARRANTY CARD .......................................................................................... 53
11.
WARRANTY TERMS ........................................................................................ 53
11.1.
Warranty claims procedures ................................................................................................ 53
11.2.
Warranty repairs record ....................................................................................................... 55