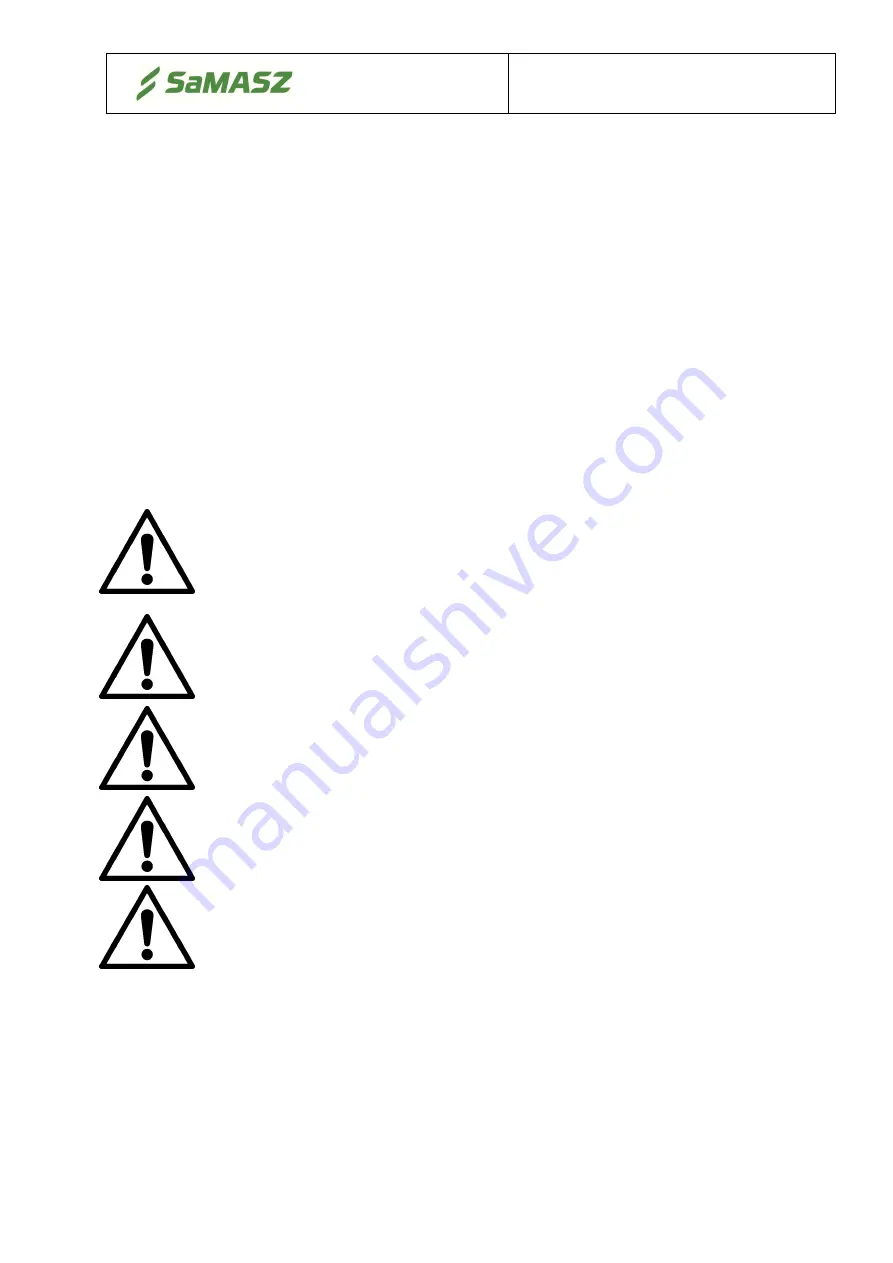
Operator’s manual
SCISSOR TRIMMER
PG 150 (F), PG 200 (F)
PG 150L (F), PG 200L (F)
- 21 -
6.
The Purchaser bears the costs of technical evaluation - when the manufacturer finds that a
claimed product is free of defects and a technical report confirms that.
7.
The Manufacturer has the right to cancel the warranty in the following cases:
a)
interference of the interior of the machine, changes of its mechanical design or
intentional damages, bending parts of the machine, etc.,
b)
damage caused by accidents, running into obstacles or other events, for which the
warrantor is not responsible,
c)
lack of needed records in the warranty card or filling in the warranty card
independently,
d)
use of the scissor trimmer not in accordance with operator
’
s manual or for incorrect
purpose, or use of the machine by untrained persons.
8.
Manufacturer can break the service agreement with immediate effect when the user do not pay
receivables according to that agreement in a timely manner and the delay in payment is longer
than 30 days from maturity date. Breaking the service agreement caused by the user makes
simultaneous breaching of the warranty.
9.
Manufacturer does not take compensation responsibility for the loss caused by breakdown of the
machine during work.
CAUTION:
Please ask your dealer to fill the warranty card with proper dates, stamps and
signature when purchasing. Lack of this important information may cause
cancel of warranty.
CAUTION:
The warranty card is valid only when there are the following information:
address, date and place of purchase, scissor trimmer type and invoice number.
CAUTION:
Every after-warranty repair can be done against payment by the repair shops
authorised by the dealer. Authorisation is a duty of your dealer.
CAUTION:
The manufacturer reserves the right to alter technical design and specification
without prior notice and without liability.
CAUTION:
The SaMASZ Company is continually working on improvement and
development of all types and models of scissor trimmers. For this reason
the form, accessories and technology of delivered products can change. No
claims can be made based on the data, illustrations or descriptions contained in
this manual or the spare parts catalogue.
The SaMASZ is not responsible for printing errors.