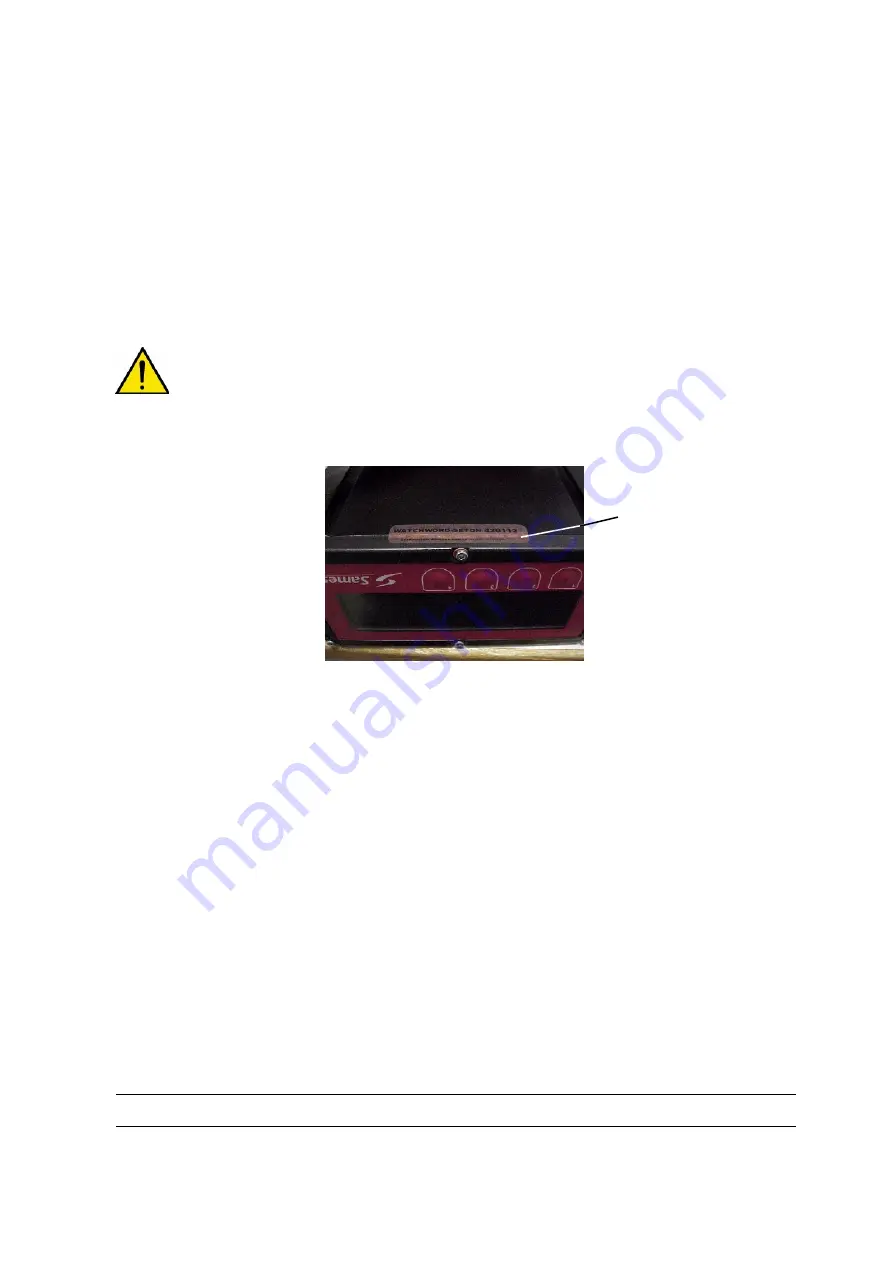
Index revision : H
6
6336
8 Powder-spraying equipment must be maintained regularly according to the manufacturer’s
instructions. Repairs must be carried out in strict compliance with these instructions.
9 Before cleaning the spray gun or carrying out any other work in the spraying area, the high-voltage
power supply must be switched off in such a way that it can not be switched back on by pressing
the spray gun “trigger.”
10 Only SAMES original spare parts guarantee operating safety of the equipment.
11 Ambient temperature must not exceed 40° C.
12 Switch off the electrical supply of the CRN 457 module before connecting the spray gun.
Before disconnecting the spray gun/ the atomizer, extinguish, switch off the power supply of the
CRN 457 (if not, a malfunction can occur).
WARNING : This equipment is intended for spraying powder paint only.
1.3. Guarantee
During the CRN 457 control module guarantee period, it is strictly forbidden to remove, attempt to
remove or cut the label (located under module) on pain of loss of guarantee.
Guarantee label