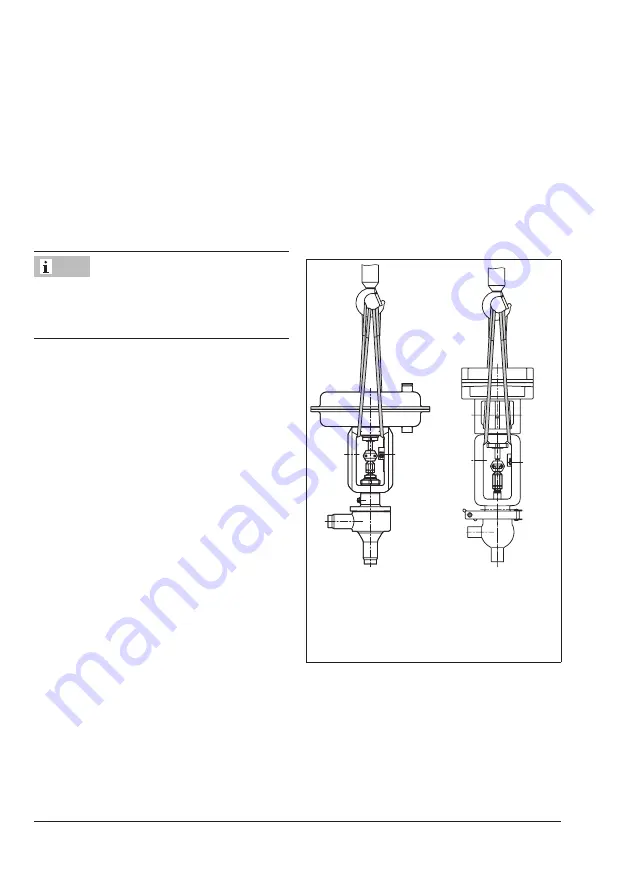
24
EB 8048 EN
Shipment and on-site transport
−
Protect the piping and any mounted
valve accessories against damage.
−
Protect the control valve against moisture
and dirt.
−
The permissible transportation tempera-
ture of standard control valves is –20 to
+65 °C (–4 to +149 °F).
Contact our after-sales service for the trans
-
portation temperatures of other valve ver
-
sions.
4.3.2 Lifting the valve
To install a large valve into the pipeline, use
lifting equipment (e.g. crane or forklift) to lift
it.
Lifting instructions
−
Use a hook with safety latch (see Fig. 5,
Fig. 6 and Fig. 7) to secure the slings
from slipping off the hook during lifting
and transporting.
−
Secure slings against slipping.
−
Make sure the slings can be removed
from the valve once it has been installed
into the pipeline.
−
Prevent the control valve from tilting or
tipping over.
−
Do not leave loads suspended when in-
terrupting work for longer periods of
time.
−
Make sure that the axis of the pipeline is
always horizontal during lifting and the
axis of the plug stem is always vertical.
−
Make sure that the additional sling be-
tween the lashing point on the actuator
and rigging equipment (hook, shackle
etc.) does not bear any load. The sling
only protects the control valve from tilting
while being lifted. Before lifting the con-
trol valve, tighten the sling.
Lifting points on the control valve
Fig. 5:
Special version
of Type 3249
with
Type 3271
Actuator
Fig. 6:
Ball body
version of
Type 3249
with
Type 3277
Actuator
Note