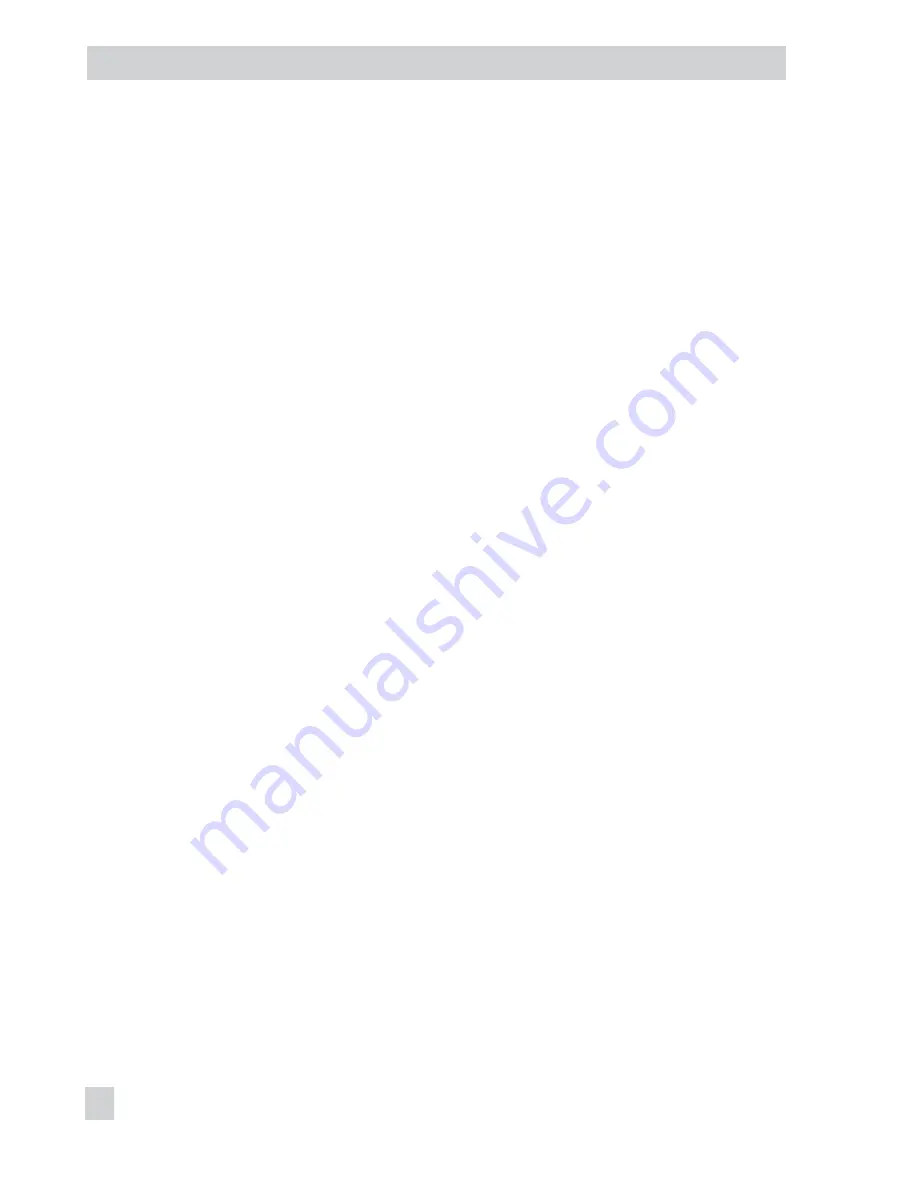
10
Maintenance
The positioner does not require any mainte-
nance.
There are filters with a 100 µm mesh size in
the pneumatic connections for supply and
output which can be removed and cleaned,
if required.
The maintenance instructions of any up-
stream supply air pressure reducing stations
must be observed.
11
Servicing explosion-
protected devices
If a part of the device on which the explo-
sion protection is based needs to be ser-
viced, the device must not be put back into
operation until a qualified inspector has as-
sessed it according to explosion protection
requirements, has issued an inspection cer-
tificate or given the device a mark of confor-
mity.
Inspection by a qualified inspector is not re-
quired if the manufacturer performs a rou-
tine test on the device prior to putting it back
into operation. The passing of the routine
test must be documented by attaching a
mark of conformity to the device. Replace
explosion-protected components only by
original, routine-tested components from the
manufacturer.
Devices that have already been operated
outside hazardous areas and are intended
for future use inside hazardous areas must
comply with the safety requirements placed
on serviced devices. Before being used in-
side hazardous areas, test the devices ac-
cording to the specifications for servicing
explosion-protected devices.
Read section 13 for maintenance, calibra-
tion and adjustment work inside and outside
hazardous areas.
12
Firmware update (serial
interface)
Firmware updates on positioners currently in
operation can be performed as follows:
When updates are performed by a service
employee appointed by SAMSON, the up-
date is confirmed on the positioner by the
test mark assigned by SAMSON’s Quality
Assurance.
In all other cases, only persons from the
plant operator with written approval may
perform updates. This person must confirm
the update on the positioner.
Laptops and PCs connected to the power
supply must use an additional safety barrier.
This does not apply to laptops in battery op-
eration. In this case, it is assumed that a bat-
tery-powered laptop runs briefly for soft-
ware programming or for testing purposes.
a) Updates outside the hazardous area:
Remove the positioners from the plant
and update them outside the hazardous
area.
b) Updates on site:
Updates on site are only permitted after
the plant operator has presented a sig-
ned hot work permit.
84
EB 8384-4 EN
Maintenance
Summary of Contents for 3730-4
Page 2: ...2 EB 8384 4 EN...
Page 127: ......
Page 188: ...188 EB 8384 4 EN...
Page 189: ...EB 8384 4 EN 189...
Page 190: ...190 EB 8384 4 EN...
Page 191: ...EB 8384 4 EN 191...
Page 192: ...192 EB 8384 4 EN...
Page 193: ...EB 8384 4 EN 193...
Page 194: ...194 EB 8384 4 EN...
Page 195: ...EB 8384 4 EN 195...
Page 196: ...196 EB 8384 4 EN...
Page 197: ...EB 8384 4 EN 197...
Page 198: ...198 EB 8384 4 EN...
Page 199: ...EB 8384 4 EN 199...
Page 206: ...206 EB 8384 4 EN...
Page 207: ...EB 8384 4 EN 207...
Page 208: ...208 EB 8384 4 EN...
Page 209: ...EB 8384 4 EN 209...
Page 210: ...210 EB 8384 4 EN...
Page 211: ...EB 8384 4 EN 211...