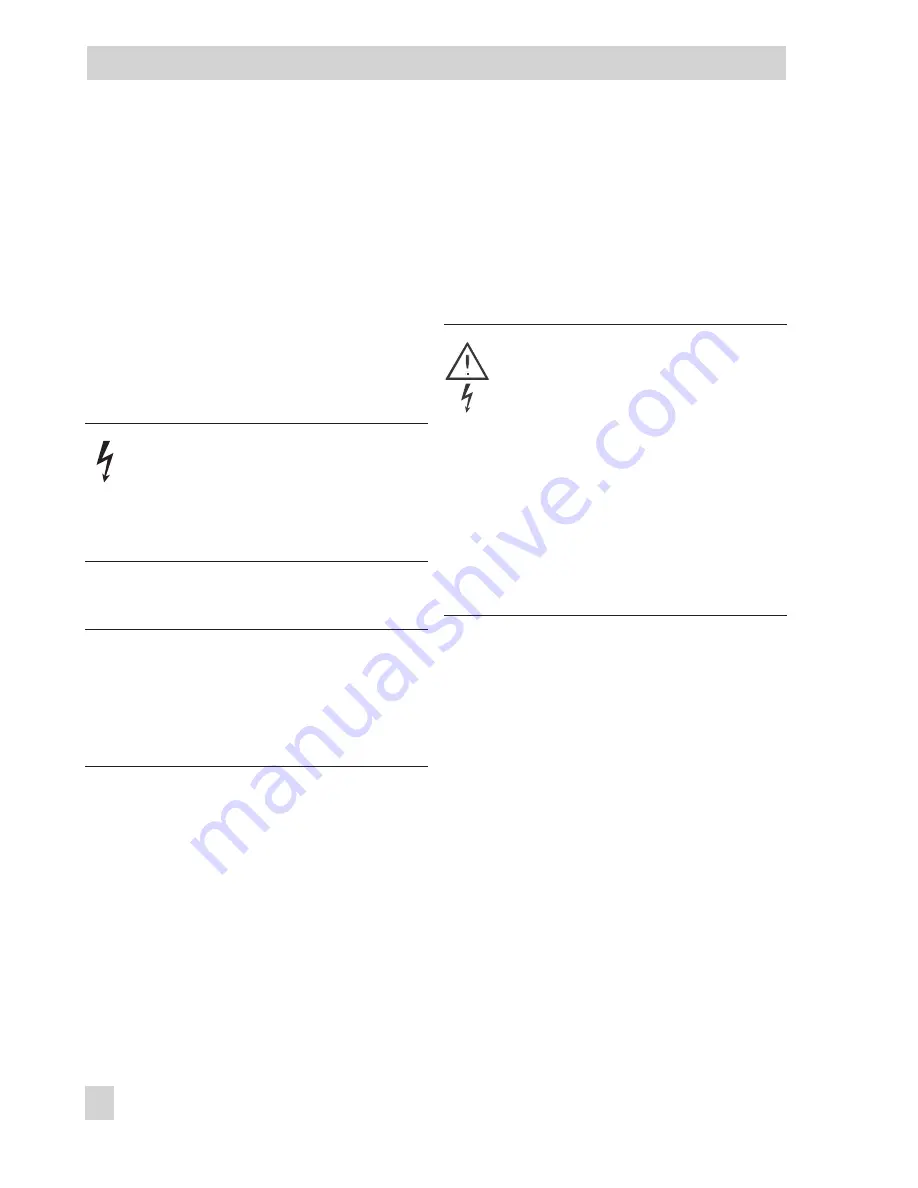
If there is no control signal, the actuator
can be adjusted manually. For manual
adjustment, remove the front case cover.
Insert a 4 mm hex wrench into the red
actuating shaft and turn it.
Only turn the shaft counterclockwise and
only up to the point at which the torque
switch in the actuator is activated. Once
the magnet has been released, the spring
mechanism will push the actuator stem
back to the fail-safe position.
Caution!
Observe the relevant safety
regulations on connecting the electric
actuator or performing any
maintenance on it.
2. Continue as described in section 4.1.
Note!
The flow rate indicated in the diagram is re-
duced by approximately 20 % for valves in
sizes DN 32 to 50 which are combined with
Type 5821/5822 Actuators.
4
Maintenance–Replacing parts
The flow regulator is maintenance free. Nev-
ertheless, it is subject to natural wear, partic-
ularly at the seat, plug, and operating dia-
phragm.
Depending on the operating conditions that
prevail, inspect the regulator at regular inter-
vals to avoid possible malfunctions.
If the valve does not close tightly, this may be
caused by a dirty seat and plug or due to
natural wear.
If the flow rate deviates considerably from
the adjusted set point, e.g. rapidly increasing
flow rate, check the operating diaphragm for
ruptures and replace it, if necessary.
Prior to carrying out any mainte-
nance work on the flow regulator, it
must be removed from the pipeline.
For this purpose, make sure the rele-
vant section of the pipeline is
depressurized and drained as well
before removing the regulator from
the pipeline.
Before removing the actuator from
the valve, switch off the power supply
and protect it from being reconnected
unintentionally.
4.1
Replacing the orifice
1. Unscrew the coupling nut (10.2). Remove
the actuator from the valve.
2.
Note!
For sizes DN 15 to 25, unscrew the
adjustment screw (8.3) first.
Use a socket wrench (order no.
1280-3001, or a self-made wrench (re-
fer to section 4.2, step 4) to unscrew the
adapter (8) of the orifice. Then pull it out
of the valve body.
3. Replace parts with new ones and reas-
semble in reverse order. Observe the
tightening torques specified in Fig. 2.
8
EB 3135-1 EN
Maintenance–Replacing parts