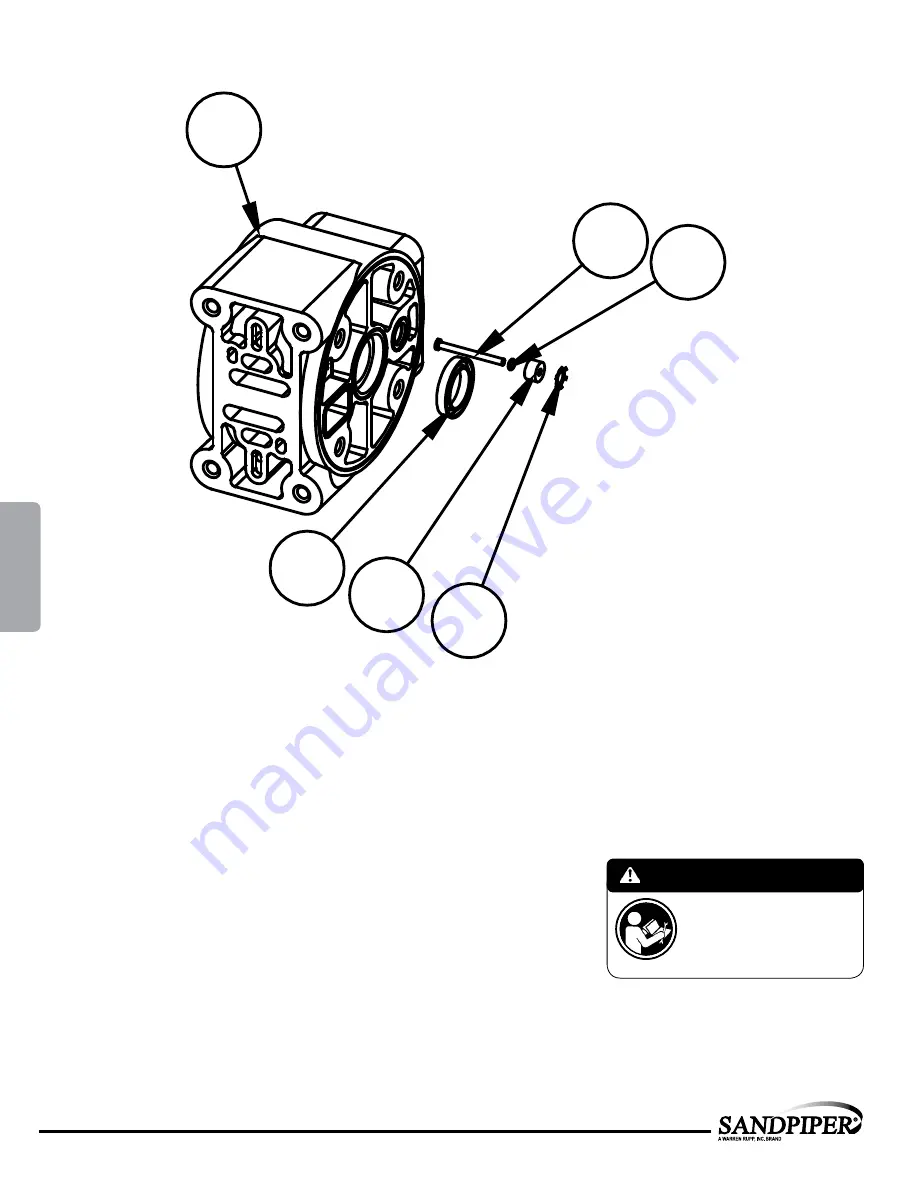
s15nmdl3sm-rev0316
sandpiperpump
.
com
15
• Model S15 Non-Metallic
IMPORTANT
When the pumped product source is at a higher
level than the pump (flooded suction condition),
pipe the exhaust higher than the product source
to prevent siphoning spills. In the event of a
diaphragm failure a complete rebuild of the
center section is recommended.
Intermediate Assembly Drawing
Intermediate Assembly Drawing
Step 1:
Remove plunger, actuator (28) from center of
intermediate pilot valve cavity.
Step 2:
Remove Ring, Retaining (30), discard.
Step 3:
Remove bushing, plunger (6), inspect for wear
and replace if necessary with genuine parts.
Step 4:
Remove O-Ring (25), inspect for wear and
replace if necessary with genuine parts.
Step 5:
Lightly lubricate O-Ring (25) and insert into
intermediate.
Step 6:
Reassemble in reverse order.
Step 7:
Remove Seal, Diaphragm Rod (32).
Step 8:
Clean seal area, lightly lubricate and install new Seal,
Diaphragm Rod (32).
4
34 6
32
30 27
MODEL SPECIFIC
4: AIR
END