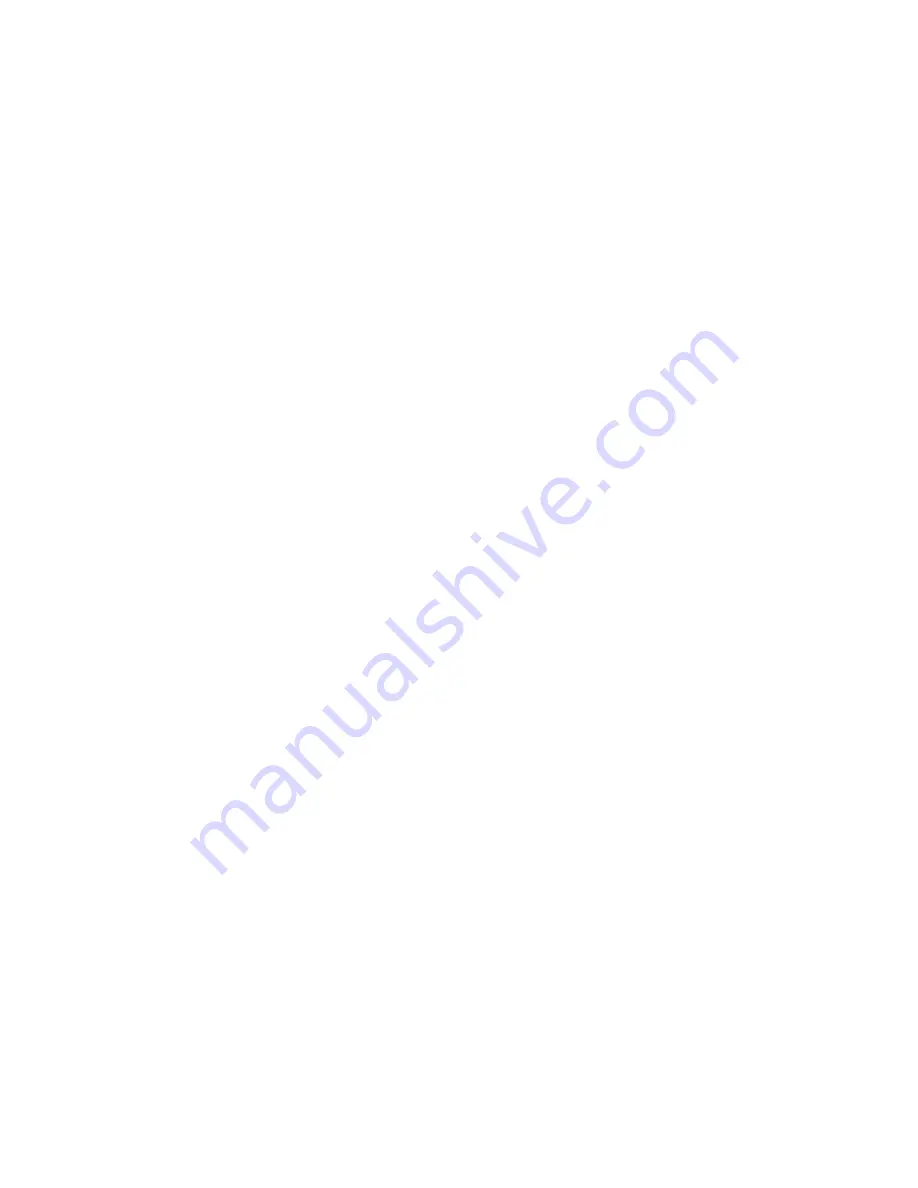
NOTES:
●
If oil fails to appear at oil sender hole within 30 seconds
of starter operation, allow the starter to cool. verify that oil
line routing is correct and that the oil tank is full to the
proper level
●
Oil pressure indicator lamp should light when ignition is
turned on. Lamp will go out after engine is started and there
is oil pressure at the switch in the crankcase.
CAUTION - Avoid excessive time of starter
engagement. Overheating of starter motor will result in
damage. Oil pump should prime and deliver oil to the
oil sender hole within 30 seconds.
J. Exhaust System
NOTE - The engine must be correctly mounted into the
frame before the exhaust system is installed.
1.
Place new woven-metal gasket into exhaust ports
of cylinder heads.
2. Inspect the exhaust pipe header flanges and
retaining rings. Replace if distorted, warped, or
otherwise damaged.
3.
Apply a high-temp. anti-seize lubricant to threads
of exhaust studs at cylinder heads.
4. Install exhausts to cylinder heads. Hand tighten
exhaust stud nuts.
5. Attach exhausts to lower mounting bracket. Shim if
necessary. Hand tighten mounting hardware.
6. Tighten exhaust flange nuts at head to 60-80 in-lbs.
WARNING - In some instances, brake master cylinder
must be spaced out from frame to clear crankcase.
UNDER NO CIRCUMSTANCES SHOULD MASTER
CYLINDER OR BRAKE LINE BE ALLOWED TO
CONTACT EXHAUST PIPE IN FINAL INSTALLATION.
Heat transferred to brake fluid may expand and cause
brakes to seize, resulting in possible fire hazard and
loss of control of motorcycle with injury or death to
rider and others.
NOTE - Make certain that the exhaust system is not pre-
loaded, or in a bind, at the lower mounting points. Make all
spacing adjustments prior to final-tightening of the upper
exhaust mounting hardware at the cylinder heads. Failure
to follow this procedure may cause excessive vibration and
result in failure of exhaust pipes or mounting hardware.
K. Initial Start-Up And Engine Break-In
NOTE - engines are designed for high performance and as
such are not as tolerant of inadequate break-in as stock or
lower performance engines. Correct break-in will assure
longer engine life and will prevent unnecessary engine
damage. Engine damage caused by improper break-in is
not covered under the S&S warranty.
1. Initial
start-up
1. For the initial start up, the fuel and ignition
systems should be adjusted to their baseline
settings. (Baseline settings allow the bike to
start and run, and are the starting point for
tuning.) This is adequate for the initial start-up
and heat-cycling of the engine.
NOTE - Because there are several ignition and fuel system
combinations possible with the S&S Twin Cam style
engine, baseline settings are not listed here. Refer to the
appropriate ignition or fuel system instruction sheet.
2. Run engine approximately one minute at 1250-
1750 rpm. DO NOT crack throttle or subject to
any loads during this period as head gaskets
are susceptible to failure at this time. During
this time, check to see that oil pressure is
normal, and that oil is returning the oil tank.
3. Shut off engine and thoroughly check for any
oil leaks, fuel leaks, or other problems. Let
engine cool to the touch.
4. After engine has cooled, start up again and
allow the motor to build some heat. Engine
should not be run longer than three to four
minutes. When the cylinders become warm/hot
to the touch (approximately 150°) shut the motor
down and let it cool to room temp. Follow the
same cautions as for the initial start-up, and
continue to watch for problems.
5. Repeat this procedure 3 or 4 times. Each
successive time it should take slightly longer to
warm up and you can increase the temperature
slightly each time. You can be more liberal each
time with the rpm, gently vary rpm continuously
from idle up to 2500 rpm in the final cycle. The
motor should not reach full operating
temperature during these cycles. Do not allow
engine temperature to become excessive.
15