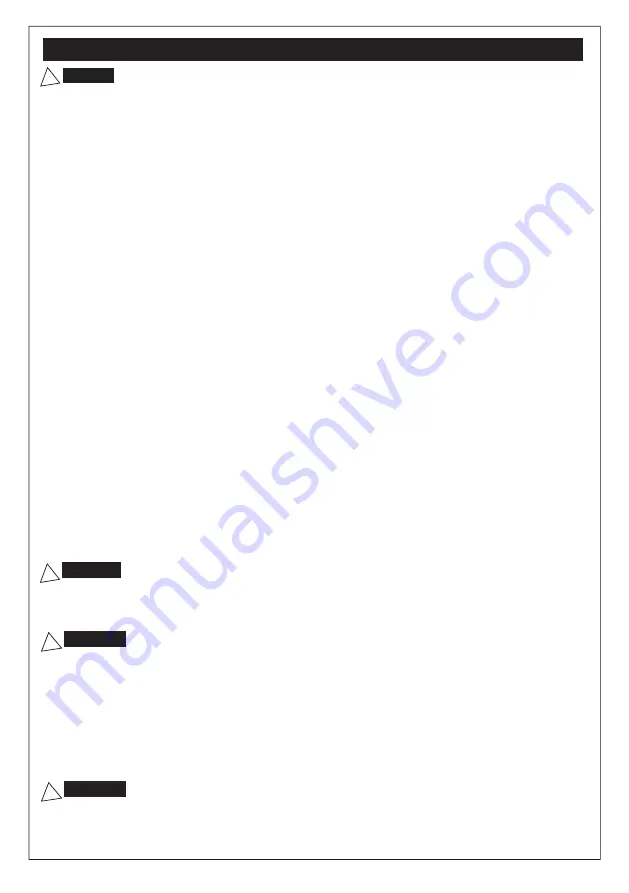
Installation of pipeline:
!
Warning:
The installation of all the pipes should be operated by qualified plumbers with
corresponding operation certificate in accordanceance with national requirements:
1. Use joints when connecting pipes.
2. Use brass pipes or copper hoses only.
3. Do not use black and galvanized or PVC pipes.
Water supply pipe (1/2'')
1. Connect hot water or cold water pipes. It had better be hot water pipe with a temperature no
more than 70°C.
2. Install stop valve in the water supply pipe. The stop valve should be installed in a place where it is
easily operated in emergency.
3. Clean the water supply pipe completely before connecting the water pipe to the steam engine.
4. It is suggested that filter and anti-furring equipment in the water supply pipe.
5. The water pressure should be at best between 15 and 20 pounds/square inch. If necessary,
decrease the pressure accordingly.
6. If necessary, install equipment to prevent the water producing sound.
Steam pipe (4.5kW pipe size:1/2''; 6kw & above:3/4'')
1. Do not install any valves in the steam pipes. The steam can never be obstructed.
2. Install a brass steam pipe(4.5kW pipe size: 1/2''
Ј
6kw & above:3/4'') between the steam outlet
and the steam nozzle.
3. The heat insulation material used to insulate the steam pipe should be resistant to temperature as
high as 120°C or higher.
4. The horizontal part of the steam pipe should be installed inclining to the steam outlet or in the
direction of steam engine. Do not bend it in a hape to make sure that the cooled water will not
stay in the curved pipe of the steam pipe.
5. The shorter the steam pipe, the better. Try to decrease the number of elbows and avoid abrupt
turns.
!
Attention:
Do not install the steam pipe in an upper or lower direction now and then, which will affect
the output of steam.
Steam nozzle (4.5kW pipe size: 1/2''
Ј
6kw & above:3/4'')
!
Attention:
Since the steam nozzle and steam outlet are very hot, try to avoid install the steam
nozzle in the position which will easily come into contact with the person in a bath in case the steam
should splash to scald the user.
1. Install the steam nozzle in the position 6-12 inches above the ground. If the steam bath is in the
bathtub or bathroom, install the steam nozzle 6 inches above the bathtub. If the steam room
above adopts materials like acryl or non-heat-resistant sheet, install additional heat insulator.
2. The steam spray outlet should be installed face down. Wind a few circles of green material belt
around the whorl of the steam pipe, install the steam nozzle and tighten with hands.
!
Attention:
In order to protect the steam nozzle, do not use the spanner or other tools to tighten,
use a little soap water and soft sponge to wipe, and do not use erosive chemical solutions or crude
cleaning tool.
Summary of Contents for BAGNODESIGN BAGNOSPA BDD-SPA-GEN6-3-A
Page 19: ...Note ...