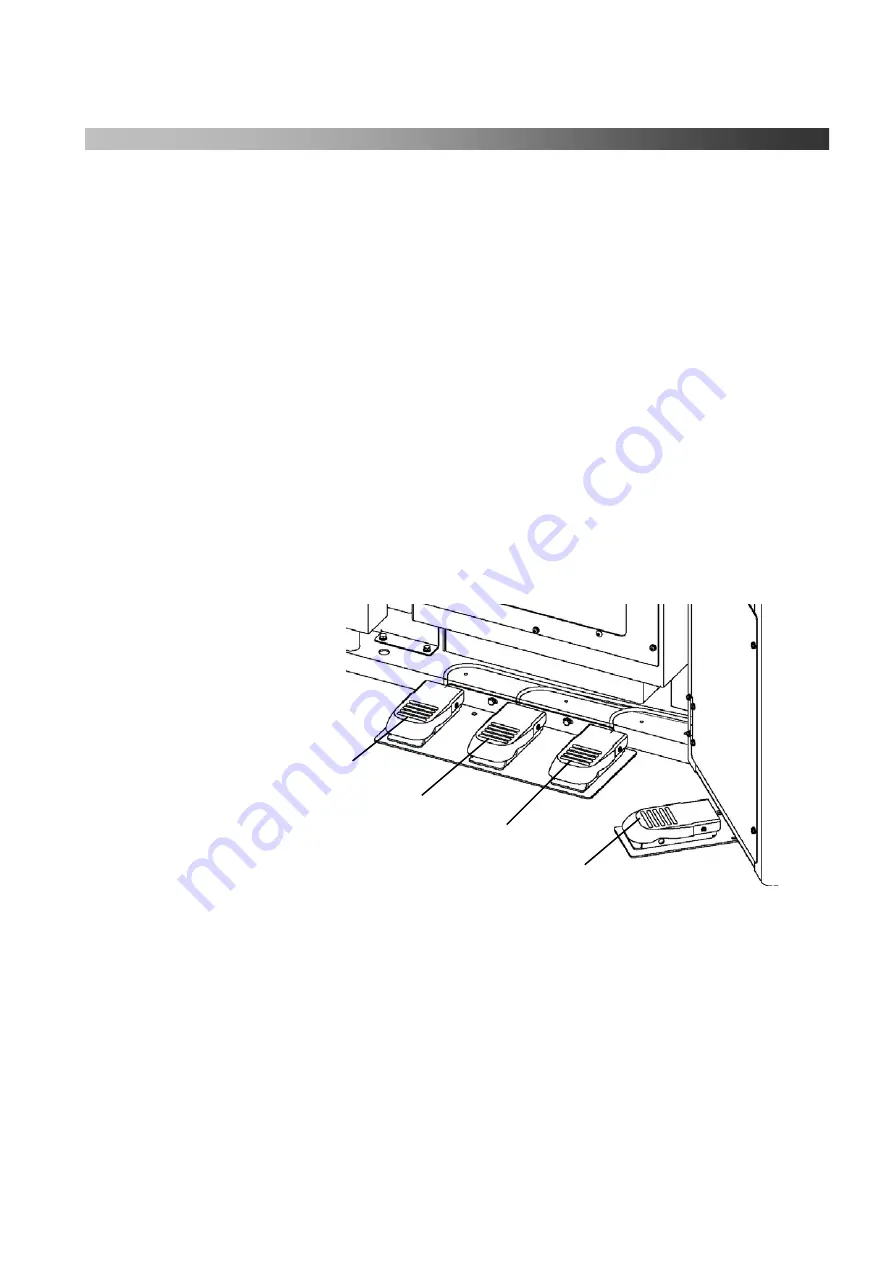
15
Foot pedal
①
Shoulder Expander Foot Pedal
When you press this pedal, Shoulder area will expand and you can adjust clothes.
Shoulder size returns when you press again.
②
Body Down Foot Pedal
When you keep on pressing this pedal, body will move down.
③
Body Up Foot Pedal
When you keep on pressing this pedal, body will move up.
④
Multi Function Foot Pedal
When you press this pedal, you can advance operation process.
Process number will be displayed on the display window.
Process is Rear clamp(-1-)
⇒
Front clamp(-2-)
⇒
Side expander(-3-)
⇒
Side Clamp(-4-)
⇒
Auto operation.
①
Shoulder Expander Foot Pedal
②
Body Down Foot Pedal
③
Body Up Foot Pedal
④
Multi Function Foot Pedal
Summary of Contents for DF-100E-V3
Page 40: ...40 ...
Page 42: ...42 Front Diagram 1 Front Diagram REV 3 ...
Page 44: ...44 Rear Diagram 2 Rear Diagram REV 3 ...
Page 46: ...46 Switch Solenoid Valve Diagram 3 Switch Solenoid Valve Diagram REV 3 315 301 ...
Page 48: ...48 Switch Solenoid Valve Diagram 3 Switch Solenoid Valve Diagram REV 3 315 301 ...
Page 50: ...50 Steam Piping Diagram 4 Steam Piping Diagram REV 3 ...
Page 52: ...52 Cover Diagram 5 Cover Diagram REV 3 513 ...
Page 56: ......
Page 57: ......
Page 58: ......
Page 59: ......
Page 61: ......
Page 62: ...DF 100E V3 Rev 6 2019 1 ...