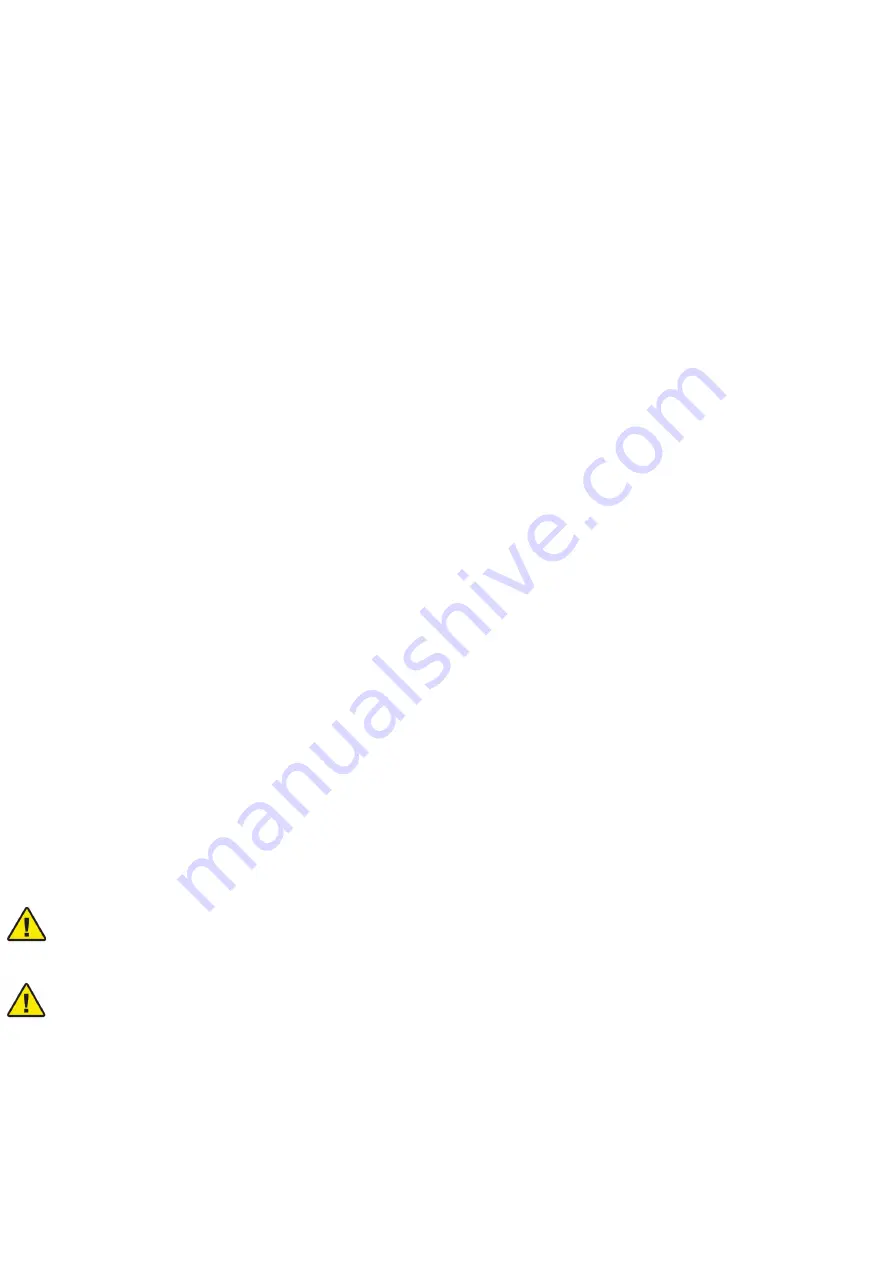
SP-MAN-INSTALL-01
Revision 2 21-12-21
3
CAUTION
CAUTION
Information and General Warnings
In the first instance
Contact the Sapphire Agent who installed and commissioned the appliance to ensure that the fault does not lie with the system compo-
nents or any incorrect setting of the system controls that falls outside of the manufacturer’s guarantee otherwise a service charge could
result. EOGB Energy Products Ltd will not be liable for any charges arising from this process.
If a fault covered by the manufacturer’s guarantee is found
Ask your Sapphire Agent to contact EOGB Energy Products Ltd Service Department on +44 (0)1480 477066 who will arrange for
a competent service engineer to rectify the fault.
Remember - before you contact EOGB Energy Products Ltd
• Ensure the appliance has been installed, commissioned and serviced by a Sapphire Approved Agent and in accordance with the
installation and servicing instructions.
• Ensure there is liquid fuel to supply the burner.
• Ensure the problem is not being caused by the heating system or its controls. Consult the appliance handbook for guidance.
Free of charge repairs
During the guarantee period no charge for parts or labour will be made provided that the appliance has been installed and
commissioned correctly in accordance with the manufacturer’s installation and servicing instructions, it was registered with EOGB Energy
Products Ltd within thirty days of installation and for appliances over twelve months old, full details and reports of annual service is availa-
ble on request.
.
The following documents must be made available to EOGB Energy Products Ltd Limited on request:
• Proof of purchase
• CD10 Installation Completion Form (or equivalent document)
• CD11 Commissioning Report Form (or equivalent document)
• Service documents (CD11 or equivalent document)
Chargeable repairs
A charge may be made (if necessary following testing of parts) if the breakdown is due to any fault(s) caused by the plumbing
or heating system, e.g. contamination of parts due to system contamination, sludge, scale, debris or trapped air. Refer to ‘Extent of manu-
facturer’s guarantee’.
Extent of manufacturer’s guarantee
The manufacturer’s guarantee does NOT cover the following:
• If the appliance has not been installed, commissioned, by a Sapphire Approved Agent in accordance with the installation and servicing
instructions.
• Instances where the serial number has been removed or made illegible.
• Fault(s) due to accidental damage, tampering, unauthorised adjustment, neglect, misuse or operating the application contrary to the
manufacturer’s installation and servicing instructions.
• Damage due to external causes such as bad weather conditions (flood, storms, lightning, frost, snow, or ice), fire, explosion, accident or
theft.
• Fault(s) due to incorrectly sized expansion vessel(s), incorrect vessel charge pressure or inadequate expansion on the system.
• Fault(s) caused by external electrics and external components not supplied by EOGB Energy Products Ltd
• Problems caused by lack of liquid fuel or faults with the fuel storage and supply system.
• Fault(s) due to contamination of the liquid fuel storage and supply system, e.g. water or debris.
• Bleeding or removing liquid fuel storage tank contamination or blockages from liquid fuel lines.
• Problems due to the flue system being incorrectly fitted or not installed to meet installation requirements.
• Application servicing, de-scaling or flushing.
• Cleaning out condensate traps/discharge pipes or thawing out frozen condensate pipework.
• Checking and replenishing system pressure.
• Liquid fuel supply pipelines, electrical cables and plugs, external controls not supplied by EOGB Energy Products Ltd.
• Heating system components, such as radiators, pipes, fittings, pumps and valves not supplied by EOGB Energy Products Ltd.
• Instances where the appliance has been un-installed and reinstalled in another location.
• Use of spare parts not authorised by EOGB Energy Products Ltd
• Consumable items including, but not limited to, liquid fuel nozzles, liquid fuel hoses, gaskets and seals.
IMPORTANT
The nozzle supplied on the burner are only covered for the period up to the time of the first service (twelve months). and must be
changed on the first service and on every annual service thereafter.
IMPORTANT
A suitable liquid fuel filter with a minimum 15µ filtration must be installed in the liquid fuel supply line.
Do not wait until the fuel supply runs out before you re-order. Sludge in the bottom of the tank may be drawn into the fuel lines.
It is recommended that the appliance is switched off when the new liquid fuel supply is delivered and that the fuel is allowed to settle for
an hour before restarting the appliance.
Terms of manufacturer’s guarantee
• The Company shall mean EOGB Energy Products ltd.
• The appliance must be installed by a Sapphire approved agent and in full accordance with the relevant Codes of Practice, Regulations
and Legislation in force at the time of installation.
• The appliance is guaranteed for 5/10 years from the date of installation, providing that every twelve months the annual service has been
completed and the appliance registered with the Company within thirty days of installation. Any work undertaken must be authorised by
the Company and carried out by a Sapphire approved service engineer.