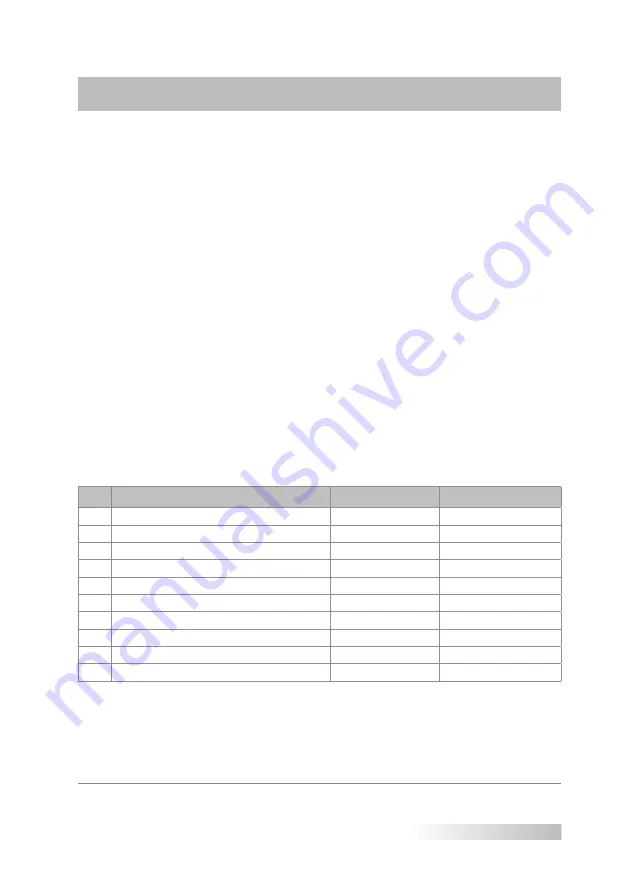
23
6. FUEL
* In particular, during fuel loading or replenishment attention should be paid to presence of wood pieces, stones or unde-
sirable objects that may block the feeder mechanism.
Seamless operation of the SAS BIO SOLID boiler with SAS MULTI FLAME
pellet burner depends on the application of the respective fuel.
The fuel for SAS
BIO SOLID boilers is the biomass is in the form of pressed granules of pellet-
-type wood, acc. to EN 14961-2 Class C1 or by PN-EN ISO 17225-2:2014-07p
class A1.
Do not use fuel with granulation thicker than specified*, since such fuel
may hinder the operation of the feeder and lead to its damage. SAS BIO SOLID
boiler equipped with automatic pellet burner is not a device for the combustion
of fossil fuels.
NOTE! The use of other fuels than recommended by the manufacturer
may cause damage to the burner, leading to loss of warranty on the burner.
It is forbidden to burn plastic materials; this may result in damage to the fur-
nace. Contamination of the heat exchanger surface leads to reduced boiler effi-
ciency and deterioration in the burning process. It is forbidden to use flammable
materials (such as petrol, kerosene, or solvents) for boiler firing, as this may result
in a fire or explosion.
Boilers fired with biogenic class „C1” fuel according to Chapter 1 of PN-EN
303-5:2012 standard.
No.
Parameter
Unit
Scope
1
Diameter
mm
6 - 8
2
Length
mm
5 - 35
3
Bulk density
kg/m
3
≥
600
4
Calorific value
MJ/kg
16,5 - 19
5
Abrasiveness
%
≤
2,5
6
Ash content
%
≤
0,5
7
Sulphur content
%
≤
0,03
8
Nitrogen content
%
≤
0,3
9
Chlorine content
%
≤
0,02
10
Water content
%
≤
12
Table 3
Basic parameters of pellets intended for SAS BIO SOLID boilers:
The density determines the durability of fuel, abrasiveness, pulp formation and
in result too low density may cause jamming of locking mechanism of the feeder.
It is forbidden to use fuel with a humidity higher than specified in the table
above. Fuel with high humidity can impede the combustion process and cause
damage to the auger feeder, feeder tubes, fuel reservoir (premature corrosion).