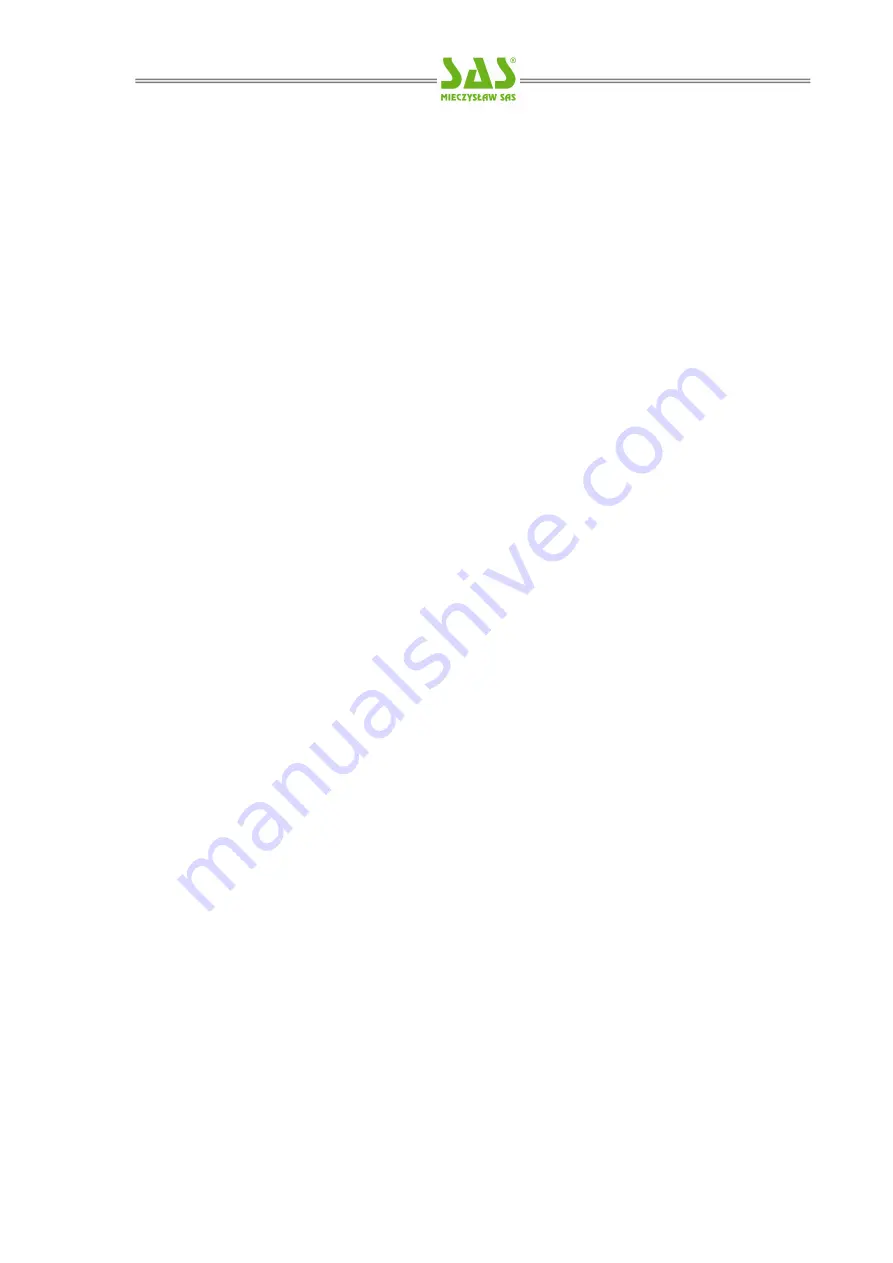
- 6 -
failure, but also makes it possible to utilize different types of fuels
occasionally (see chapter. 4), or to perform short term cycles of so called „burn out”
during the heating season, as well as before and after it.
Special three-duct design of boiler’s combustion channel helps in full utilization
of gases heat. In addition, the upper part of combustion chamber is closed with a
water jacket. Gases are being led to the chimney through the smoke conduit (pos.
21) placed at the back of a boiler. The smoke conduit is equipped with smoke throttle
(pos. 20), with in case in to high chimney draught allows for its throttling. On the
smoke conduit sidewall there is washout whole (pos. 19).
Front charge-cleaning door (pos.6), furnace door (pos. 11) and ash box door (pos.
13) are placed on the boiler’s front. For periodic cleaning operations and also for firing
up a boiler, the retort may be accessed through furnace door.
Front charge-cleaning door and in the upper part of boiler, under the cover, there is a
flap of upper washout hole cover (pos.18). It renders easy access to perform cleaning
operation of the heat exchanger cassettes. Lateral washout door (pos. 26) are used
for dust removing if accumulated.
To the upper part of the heat exchanger a hot water connector (pos. 17) is welded. To
the lower part of it, on the back wall, a return water connector (pos. 5) is welded.
Blowdown connection (pos.31) is placed on the boiler’s lateral wall.
The entire constructions is wrapped with insulation material ( pos. 2), a mineral wool,
which fills the space between a head exchanger and boiler’s casing (pos. 1).