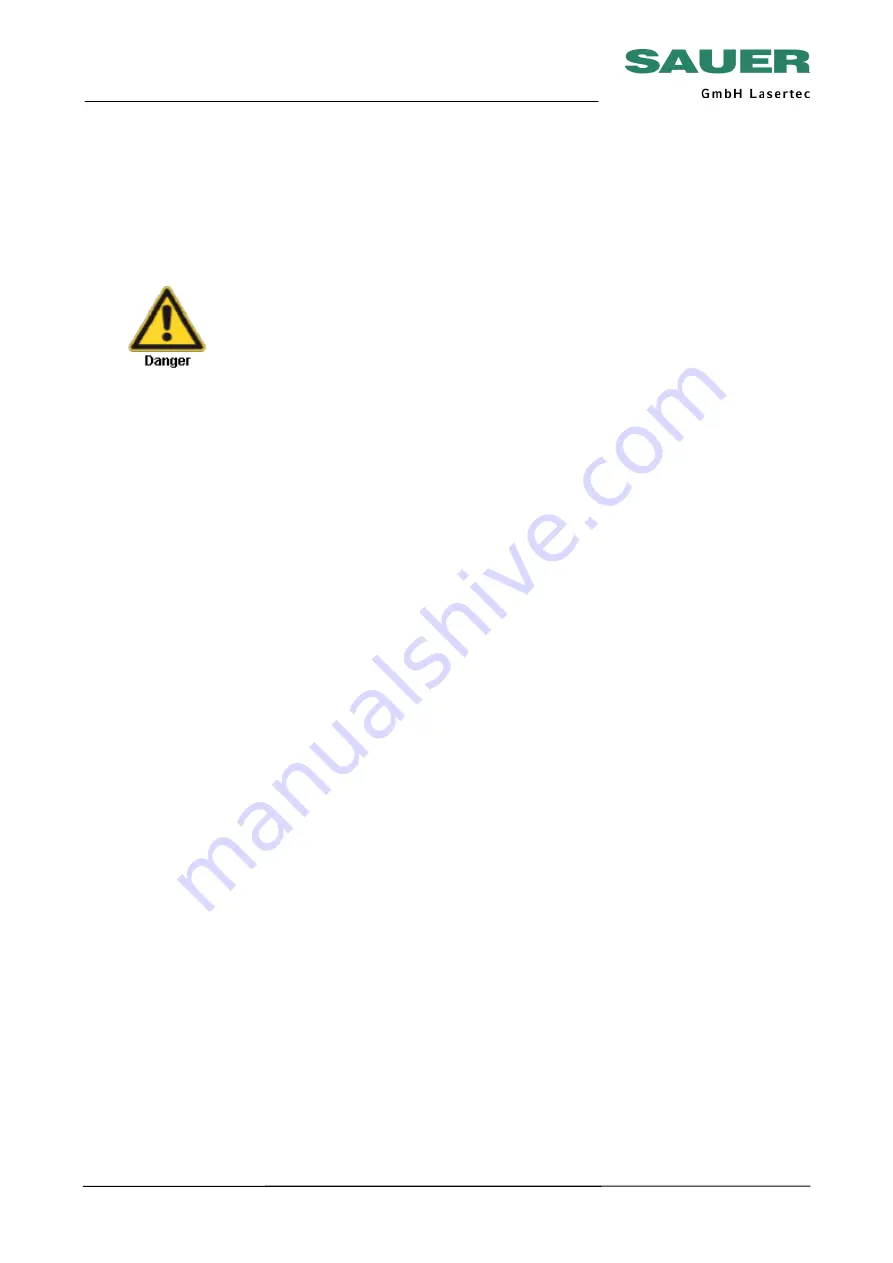
Planning, transport, installation
LASERTEC 40
Page 7
Service / maintenance
"As per and in addition to the general installation conditions, VDW
502 A and LMW 188 A, the operating organisation undertakes the
obligation to provide technical support during installation and repair
work, in particular the provision of suitable ladders, platforms,
scaffolding, heavy tools, lifting gear etc.".
The master switch on the machine is only allowed to be switched on
in the presence of the authorised service engineer!