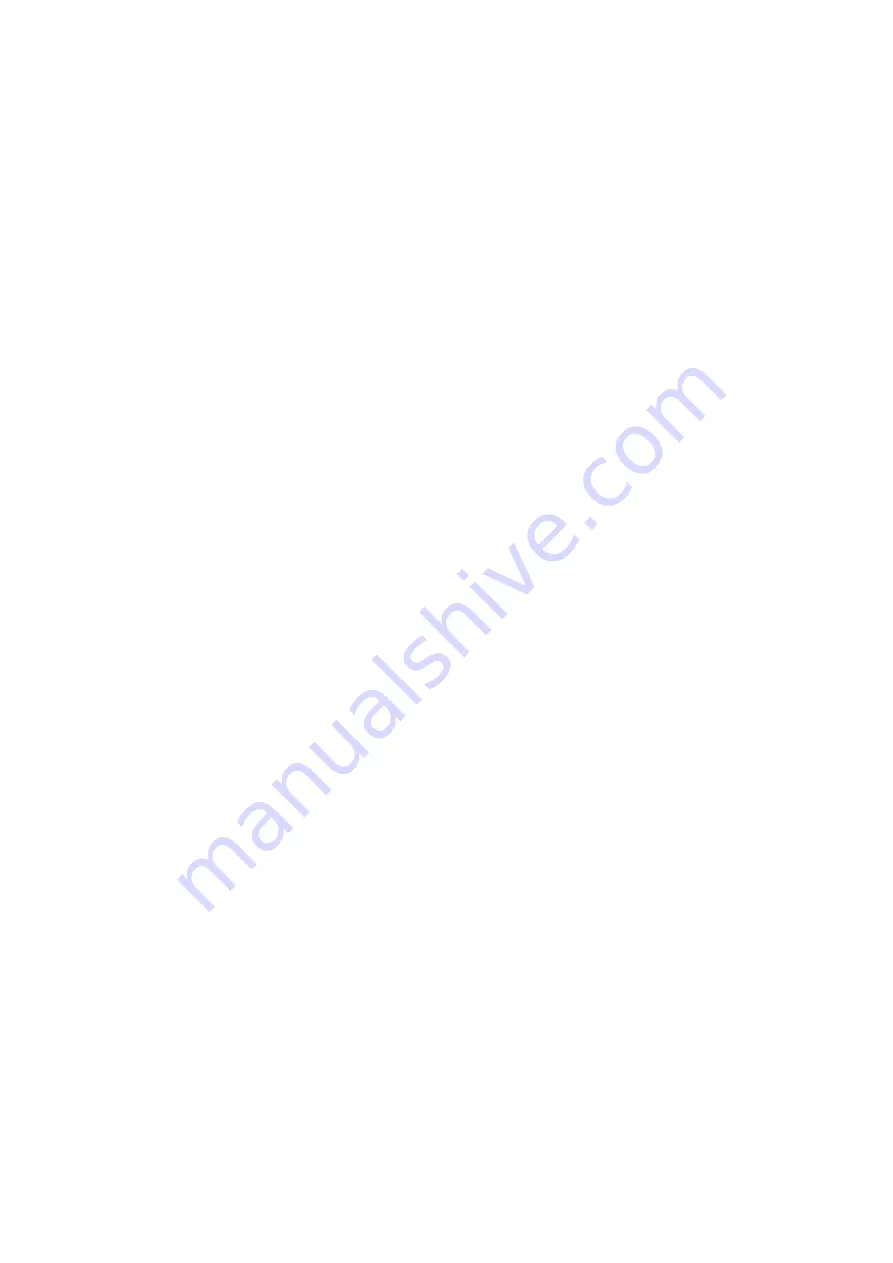
19
Avoid excessive pressure as this will tend to decrease the wheel speed and the amount of
stock removal, cause uneven wear on the grinding wheel, and overload the motor.
Avoid grinding on the side face of the wheel.
Do not arrest the wheel by applying pressure to it at the conclusion of the grinding
operation. Always allow the machine to run down freely to rest.
The machine can be operating max. 30 min/hour.
3. WHEEL CARE
Store spare grinding wheels flat on a firm surface with a layer of compressible material
between the wheels and the storage surface. Similar material should be placed between
wheels when a number are being stored.
As the grinding wheel is used it will wear. it is recommended that the wheel is replaced
when the diameter has been reduced approximately 25% below the original size (e.g. 300
mm to 225 mm : 200 mm to 150 mm : 150 mm to 112 mm : and 12.5 mm to 94 mm).
Wear on the wheel can cause eccentricity leading to machine vibration and »bouncing« of
the work piece.
Unless this condition is corrected it can result in further damage to the wheel and possible
harm to the rotor bearings. To obtain wheel balance and good efficient grinding action the
wheel must be redressed. A suitable wheel dressing tool is available under the part
number 1168.
Summary of Contents for SC 150
Page 8: ...8 5 TEKNISKE DATA 5 1 Splittegning af SCANTOOL SC 150 200 T E ...
Page 11: ...11 5 4 Splittegning af båndarm 50x800 ...
Page 22: ...22 5 TECHNICAL DATA 5 1 Drawing of SCANTOOL SC 150 200 T E ...
Page 25: ...25 5 4 Drawing of belt arm 50x800 ...
Page 36: ...36 5 TECHNISCHE DATA 5 1 Split Zeichnung vom SCANTOOL SC 150 200 T E ...
Page 39: ...39 5 4 Split Zeichnung vom Bandschleifvorrichtung 50x800 ...