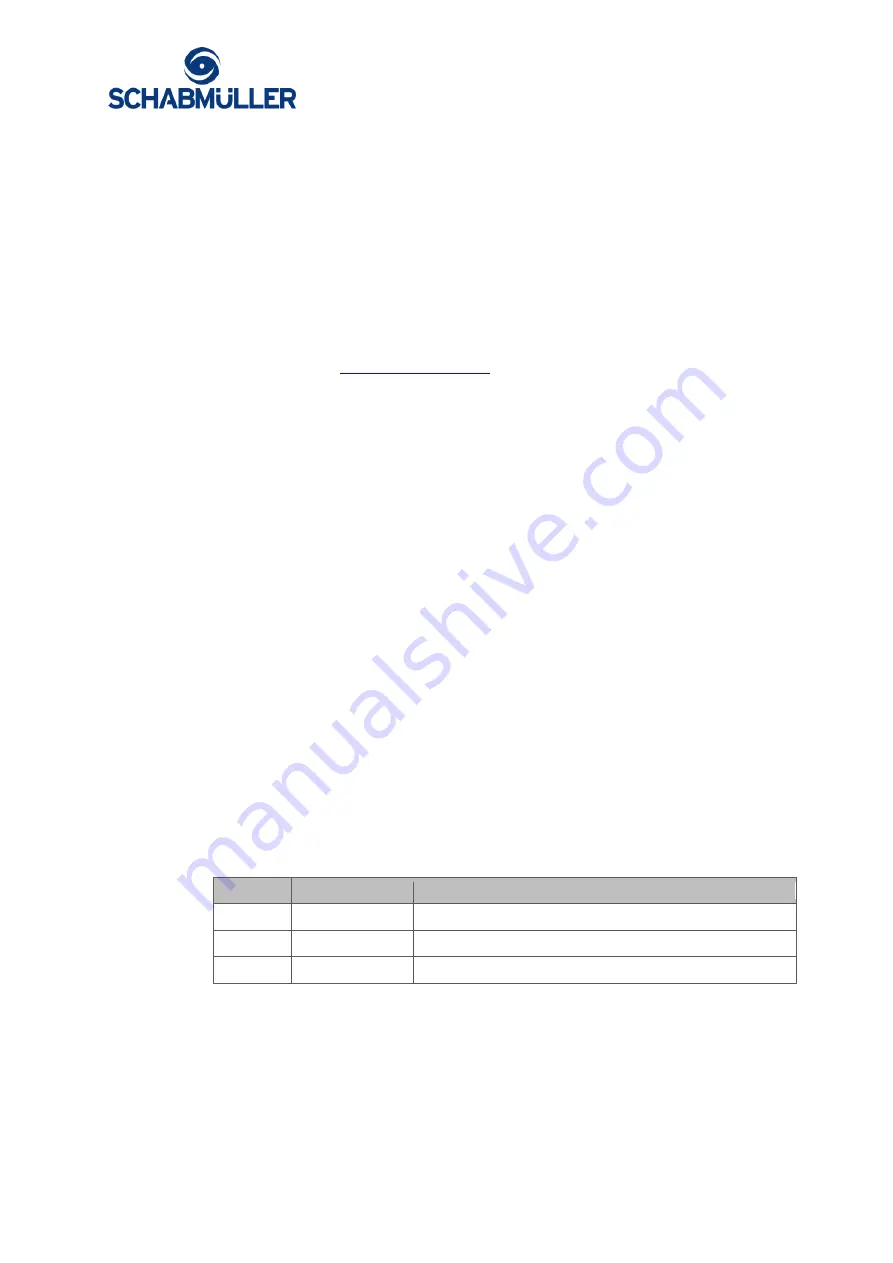
Operating and maintenance instructions
Imprint
Version 1.0
Page 2 of 56
Imprint
Schabmüller GmbH
Industriestraße 8
92334 Berching
Germany
Tel.: +49 8462 204-0
Fax: +49 8462 1841
E-mail:
Homepage:
www.schabmueller.de
© Schabmüller GmbH 2019
Distribution as well as duplication of the instructions, use and communication of the
contents are forbidden. Violation will result in claims for damages. All rights reserved
in the event of patent or utility model registration.
Technical changes
We reserve the right to make technical changes in production, processing and
appearance of all editions.
Record of changes
Version
Date
Changes
1.0
22/03/2019
New creation