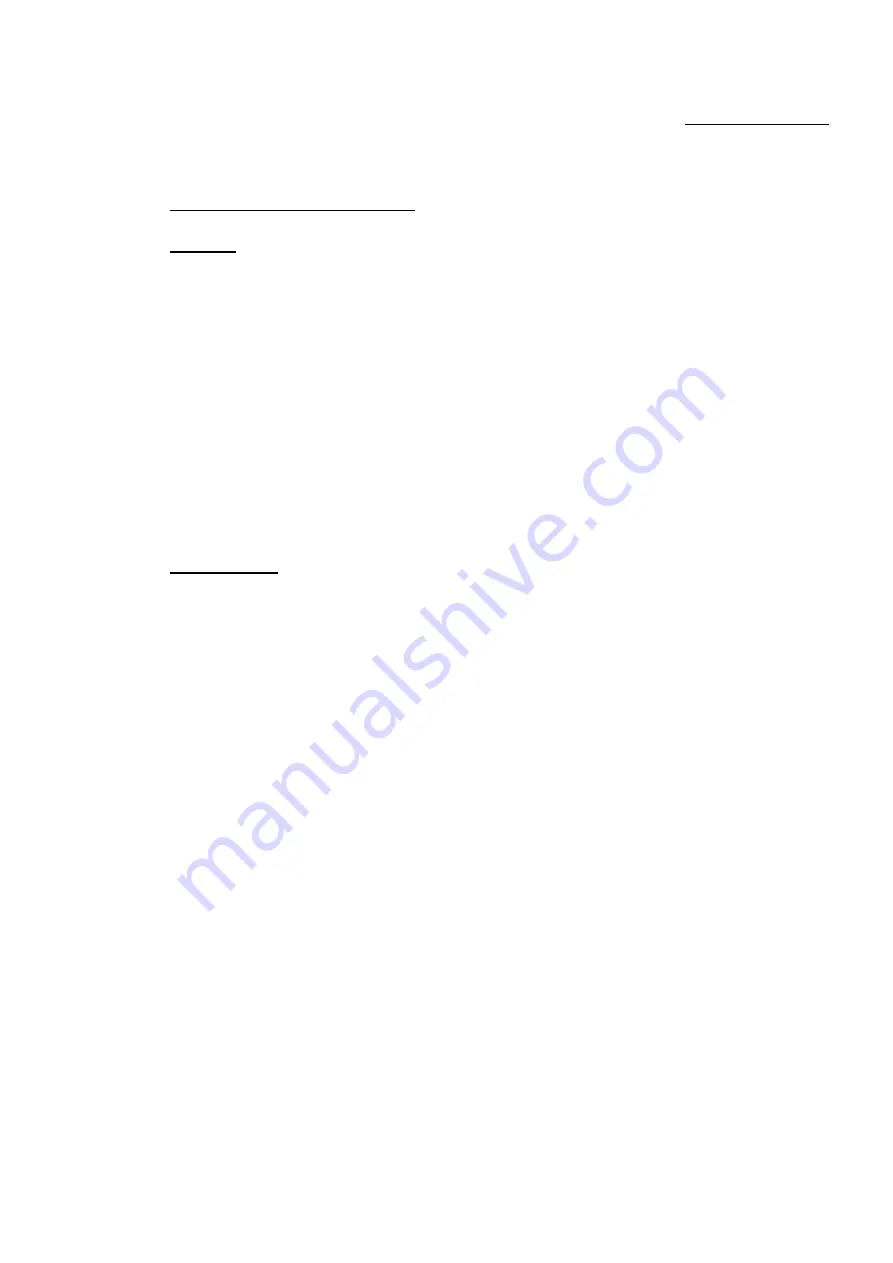
SCHEMPP-HIRTH FLUGZEUGBAU GmbH., KIRCHHEIM/TECK
Arcus M
FLIGHT MANUAL
2.13 Aerotow and winch launch
Aerotow (propeller retracted)
Only permissible on the nose tow release and with retracted propeller!
Maximum towing speed:
180 km/h
(97 kts, 112 mph)
Weak link in tow rope:
max. 850 daN (1911 lb)
Minimum length of tow rope:
30 m
(98 ft)
Tow rope material
Hemp or Nylon
Winch launch (propeller retracted)
Only permissible on the c/g tow release and with retracted propeller!
Maximum launching speed:
150 km/h
(81 kts, 93 mph)
Weak link in winch cable:
max. 1000 daN (2248 lb)
October 2011
Revision --
appr. 2.13