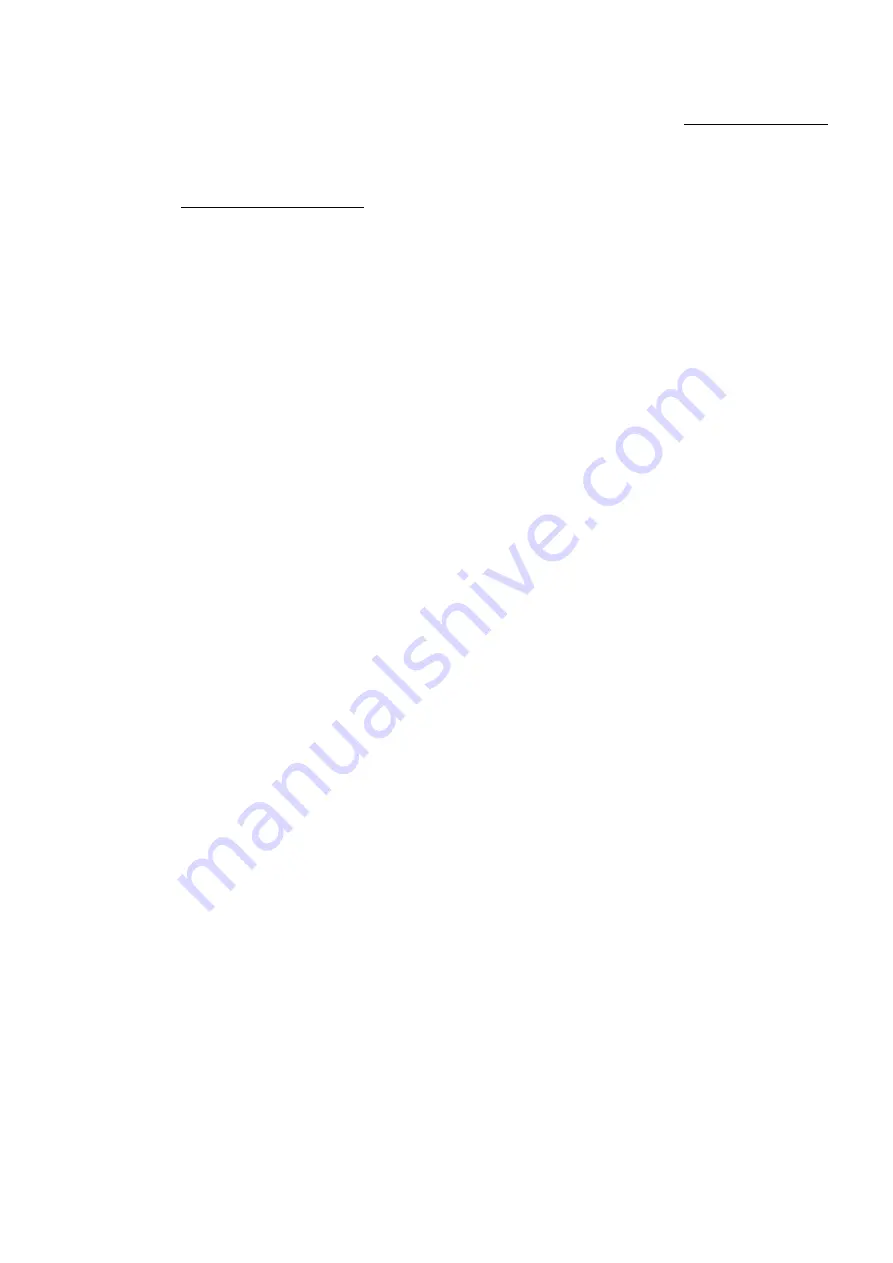
SCHEMPP-HIRTH FLUGZEUGBAU GmbH., KIRCHHEIM/TECK
Ventus-2cM
FLIGHT MANUAL
Cruising on own power
As clearly shown by the figures of section "Flight Performances", the longest
range results from the
"sawtooth"-method,
which consists of the following flight sections being repeated as required:
•
a climb at a speed of about 95 – 100 km/h (51 – 54 kt, 59 – 62 mph)
•
a glide in "clean" sailplane configuration.
Thereby the height to be consumed in glide should not be less than 500 m
(1640 ft).
The maximum range in glide is achieved at a speed of about 100 to 110 km/h
(54-59 kt, 62-68 mph), resulting in an average speed of about 100 km/h (54 kt,
62 mph).
Should the "sawtooth"-method be impracticable due to low cloud ceiling or
because of airspace restrictions, then cruising in level flight at a speed of about
149 km/h (80 kt, 93 mph) is also possible. The range, however, is then
considerably less – see page 5.3.2.3.
For cruising flight, the "sawtooth" method should always be preferred, as besides
the longer range the pilot is much less exposed to engine noise (RPM’s in climb
are less than in level flight).
November
2003
LBA-app.
Revision --
4.5.3.7
Summary of Contents for Ventus-2cM
Page 11: ......