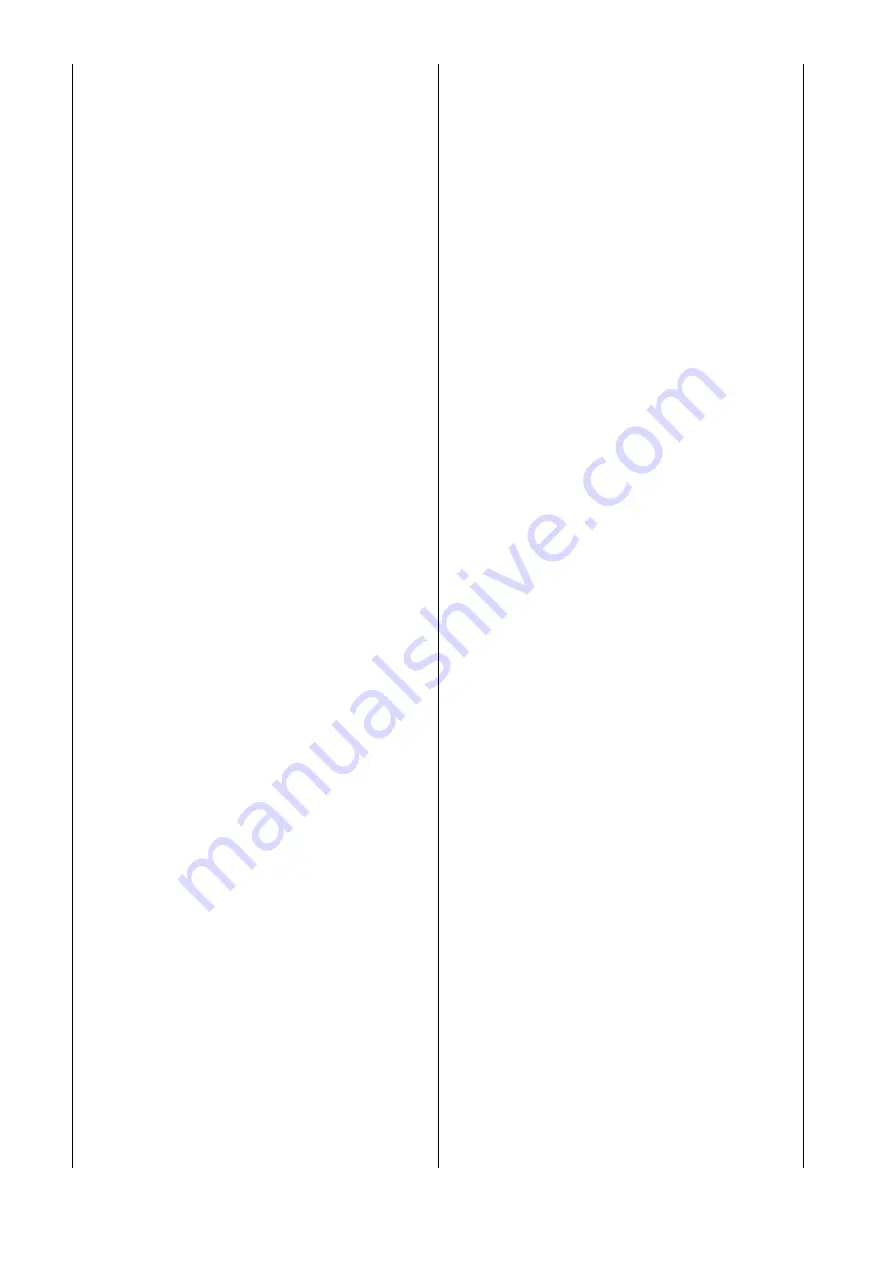
english 21
2 Set the swinging part (3) in the square tube at a
right angle to the sawblade using the hexagon bolt
(2). Use a right-angle gauge to this purpose, and
subsequently make a trial cut.
Crane bow, Fig. 6
The two crane bows (6) are fitted diagonally to each
other. On the two crane bows, carrying belts can be
attached for supporting the machine on a crane.
Sawblade guard, Fig. 7
•
The sawblade guard is fitted ready for use.
• The sawblade guard is a protecting device and must
always be fitted.
• Make sure the guard always lies on the table top by
its own weight, but that the two bolts are tightened
without play.
Setting the riving knife, Fig. 3 + 8
• The clearance between sawblade and riving knife
must not exceed 8 mm.
• After every sawblade change check the clearance
and re-adjust, if necessary. The riving knife tip must
not be lower than the base of the uppermost tooth.
We recommend a maximum setting of 5 mm under-
neath the upper sawing tooth tip.
If necessary, correct as follows (Fig. 8.1):
1 Release the 4 hexagon bolts (2).
2 Adjust the riving knife.
3 Retighten the hexagon bolts (2).
• The riving knife is an important protective device for
guiding the work piece and closing the gap behind
the sawblade, thus avoiding the kick-back of the
work piece. Mind the thickness of the riving knife –
see the embossed figures on the riving knife. The
riving knife must not be thinner than the sawblade
and not thicker than the width of the cutting gap.
Fig. 9
The riving knife must be in line with the sawblade.
Correct any difference as follows:
1 Release two hexagon bolts (1) each on both sides.
2 Align the riving knife vertically.
3 Slightly tighten the hexagon bolts (1).
4 Adjust the riving knife in line with the sawblade, and
retighten the four hexagon bolts.
5 Check the clearance to the sawblade.
Note:
If, at switching off, the brake lacks efficiency, it must
be examined by a specialist or replaced. A defective
push stick must be replaced.
10. Electrical connection
The installed electrical motor is connected ready to
operate. The connection complies with the relevant
VDE- and DIN-regulations.
The power supply as well as the used extension cable
should comply with these regulations.
Motor-brake facility
Your construction circular saw is equipped with an
automatically functioning deadlock brake. The brake
starts functioning after switching off the motor.
Important information
The electrical motor is made for operating mode S 6
/ 40 % .
When the motor gets overcharged, it automatically
switches off. After a short cool-down period (time var-
ies) the motor can be switched on again.
Defective electrical power supply cords
Electrical power supply cords often suffer insolation
damages. Causes are:
• Pressure spots, when power supply cords are being
led through windows or doors.
• Buckling spots by incorrect attachment or guidance
of the power supply cords.
• Cuttings by driving over a power supply cord.
• Insulation damages through pulling out of the sock-
et.
• Cracks in worn-out insulation.
Such defective electrical power supply cords should
not be used and are extremely dangerous because of
the insulation damage.
Check electrical power supply cords for damages on
a regular basis. Please observe that upon checking
the power supply cord is not plugged in. Electrical
power supply cords have to comply with the relevant
VDE - and DIN-regulations. Only use power cables
with the qualification H 07 RN. An imprint of the type
denomination is rule.
Alternating current motor, Page U5
• The supply voltage should be 230 Volt/50 Hz.
• Extension cables must be up to 25 m long, have
a cross cut of 1.5 square millimeter, be over 25 m
long, and have a minimum 2.5 square millimeter.
• The powersupply should be 16 A.
Rotary current motor
• The power supply should be 400 Volt/50 Hz.
• The power supply and the extension cables must
be 5-fold leads = 3 P + N + SL.
• Extension cables must have a minimum cable cross
section of 1.5 square millimeter.
• The power supply should be maximum 16 A.
• In case of connection to the power supply or moving
site the rotary direction should be checked, other-
wise the polarity has to be changed (wall mounted
connector).
• Therefore screw the phase switcher into the plug
surrounding with a screw driver. (See Fig. 10)
Connections and repairs of the electrical equipment
should only be carried out by an electrical specialist.
In case you have further questions, please specify
the following:
• Motor manufacturer
• Current type of the motor
• Information of the machine type label
• Information of the switch type label
When sending back the motor, always return the com-
plete power unit with switch.