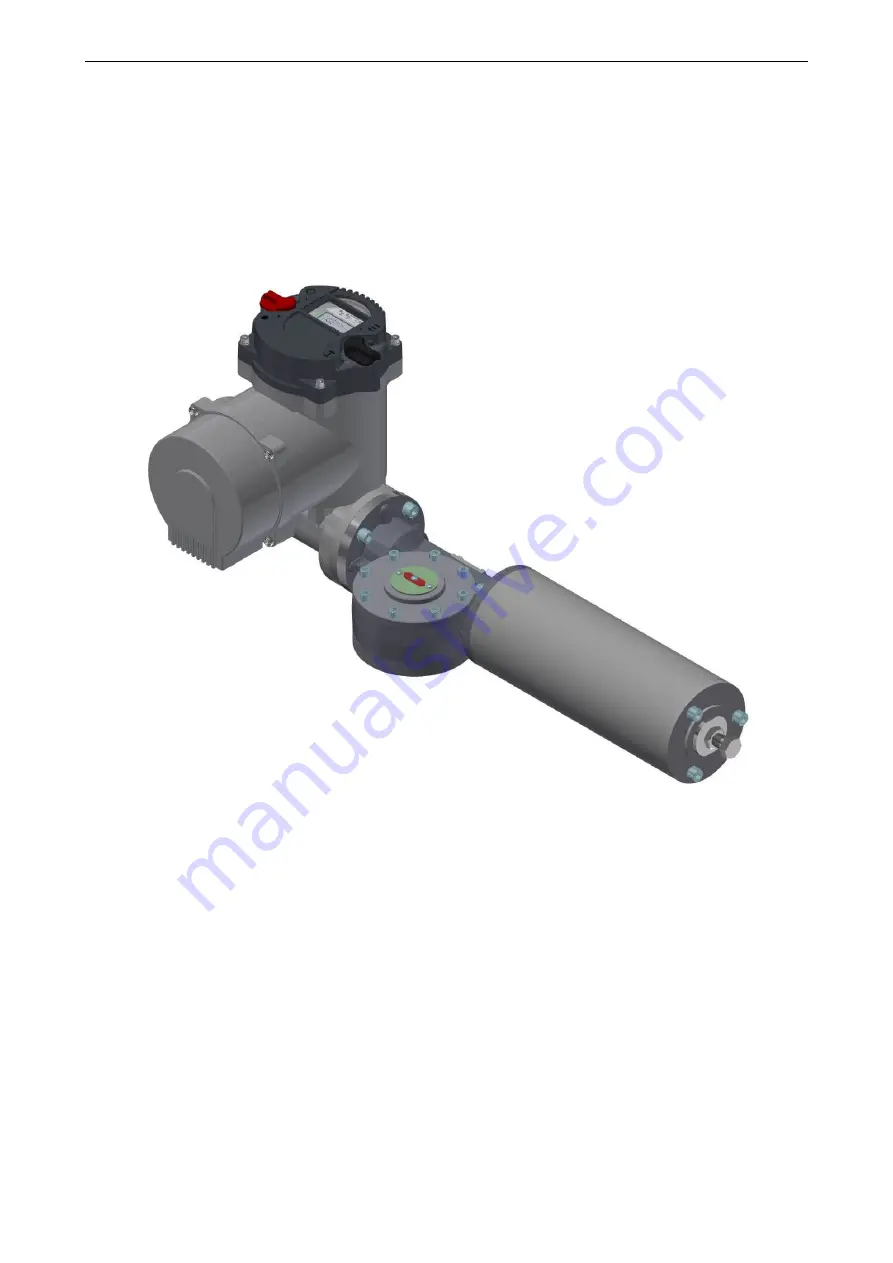
2 Introduction
Operating Manual 90° ACTUSAFE CMF(S)QT
OM-ENGLISH-Failsafe-QT-16xx-V2.00-2022.03.01
2
Introduction
NOTE:
Also consider the Operating Manual for ACTUSMART CM.V1.2 starting at page 22!
90° ACTUSAFE actuators are designed to operate appropriate fittings when a Failsafe functionality is required.
Appropriate fittings are all kinds of fittings that require a 90° movement to operate (butterfly valves, ball valves, taps in
general, etc.).
In the event of a power failure or if the Failsafe function is triggered deliberately, the 90° ACTUSAFE actuator shifts the
fitting to the Failsafe position, using the built-in energy storage device.
Figure 1:
CMF(S)QT - Actuator
6