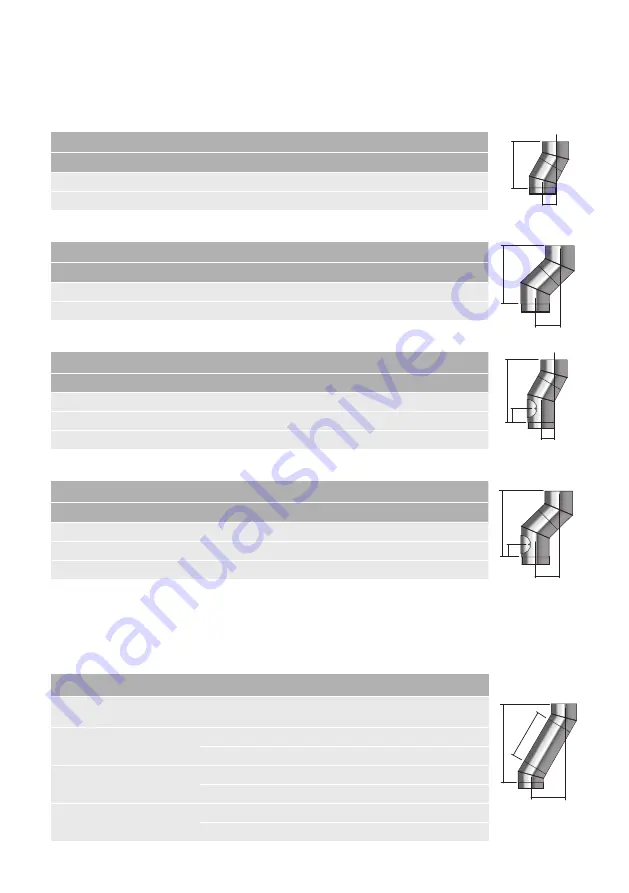
14
Offset Dimensions
(Made by assembling 2 Bends)
Offset Dimensions
(Made by assembling 2 Bends and a Standard Pipe Section)
Offsets 30˚
Int
Ø
125
150
180
200
A
276
276
276
276
B
74
74
74
74
30˚ Offset using Inspection Bend
Int
Ø
125
150
180
200
A
407
407
407
407
B
74
74
74
74
C
100
100
100
100
45˚ Offset using Inspection Bend
Int
Ø
125
150
180
200
A
415
415
415
415
B
138
138
138
138
C
94
94
94
94
Offsets 45˚
Int
Ø
125
150
180
200
A
333
333
333
333
B
138
138
138
138
A
C
B
A
C
B
A
B
A
B
A
Eff Pipe
B
30˚ Offset with standard Pipe lengths
Nom
Ø
mm
125
150
180
200
Effective Pipe 950
A
1099
1099
1099
1099
B
549
549
549
549
Effective Pipe 450
A
666
666
666
666
B
299
299
299
299
Effective Pipe 200
A
449
449
449
449
B
174
174
174
174