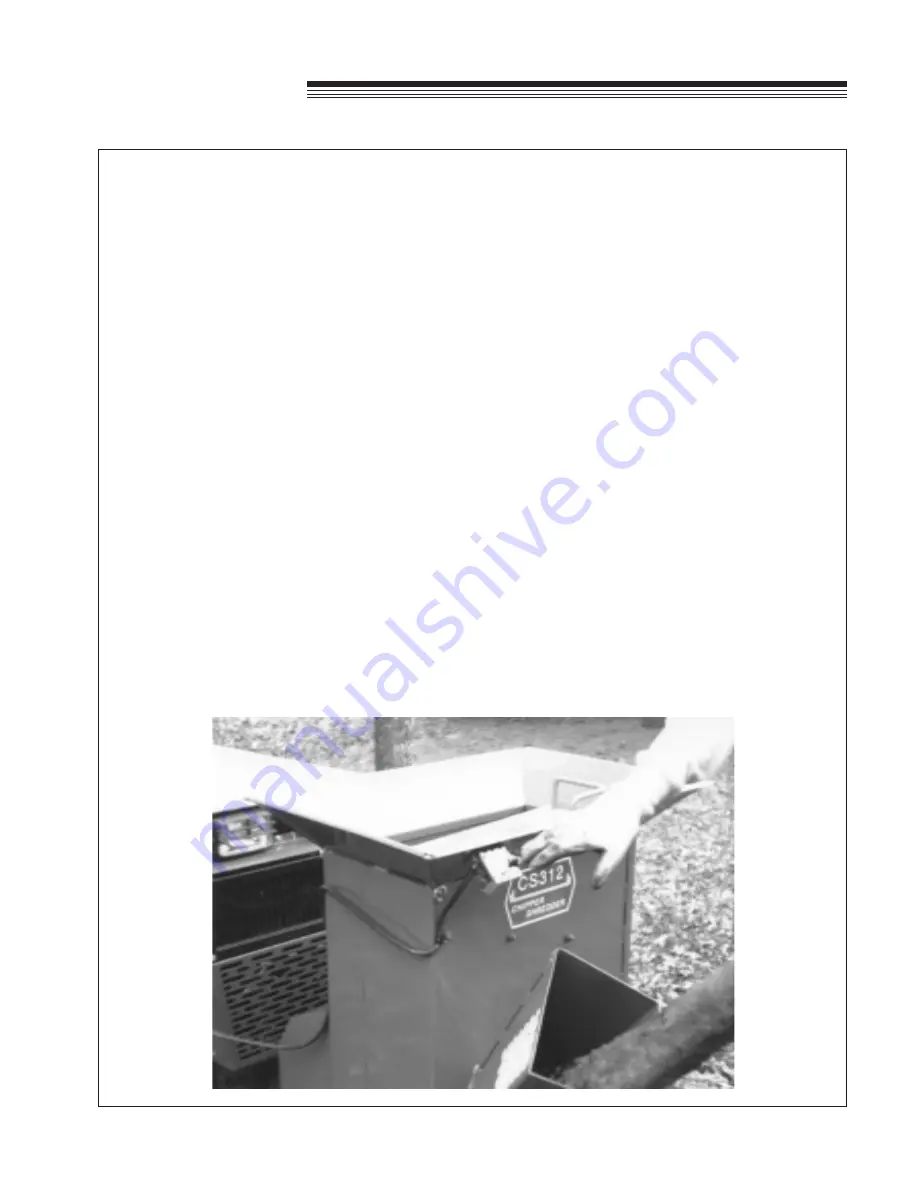
7
CHIPPER/
SHREDDER
INSTALLATION
MOUNTING INSTRUCTIONS
The chipper/shredder should be used only on the Steiner 420, 425 and 525 power units equipped
with the required chipper/shredder electrical outlet. (This electrical outlet is shipped with each chipper/
shredder. See Page 27 for electrical outlet installation.)
NOTE:
The PTO drive line is subject to shock loads while using the chipper/shredder. Therefore, the
chipper/shredder is not recommended for use on the Steiner 220 power unit. Damage to the hydrostatic
pump may result.
To mount the Chipper/Shredder do the following steps:
1. Open quick hitch latches. Drive tractor into position, aligning the quick hitch. Be sure that both latches
are fully engaged and locked.
2. Stop engine! Do not attempt to install drive belt with engine running.
3. Release double idler assembly to facilitate easy installation of the B-41 drive belt. Put belt over drive
pulley and engage or adjust double idler assembly. (See Power Unit Operator’s Manual for PTO belt
tension adjustment.)
4. Plug emergency stop cable into chipper/shredder electrical outlet on tractor. Be certain the Emergency
Stop Switch is pulled out for normal operation. Do not operate the Chipper/Shredder without this cable
plugged in.
5. Remove clip pin and rotate stand to highest position. Reinsert clip pin.
6. A rear weight bar with 4 weights is recommended to provide additional stability in transport.
7. Start engine, engage PTO and check operation of Emergency Stop Switch. (See photo below)
Summary of Contents for 73-70900
Page 23: ...21 CHIPPER SHREDDER PARTS SECTION PARTS SECTION ...
Page 24: ...22 CHIPPER SHREDDER HITCH DRIVE PARTS FIGURE 1 ...
Page 26: ...24 CHIPPER SHREDDER FRAME PARTS FIGURE 2 ...
Page 28: ...26 CHIPPER SHREDDER EMERGENCY STOP SWITCH PARTS FIGURE 3 ...
Page 30: ...28 CHIPPER SHREDDER CHIPPER SHREDDER BLOWER PARTS FIGURE 4 ...