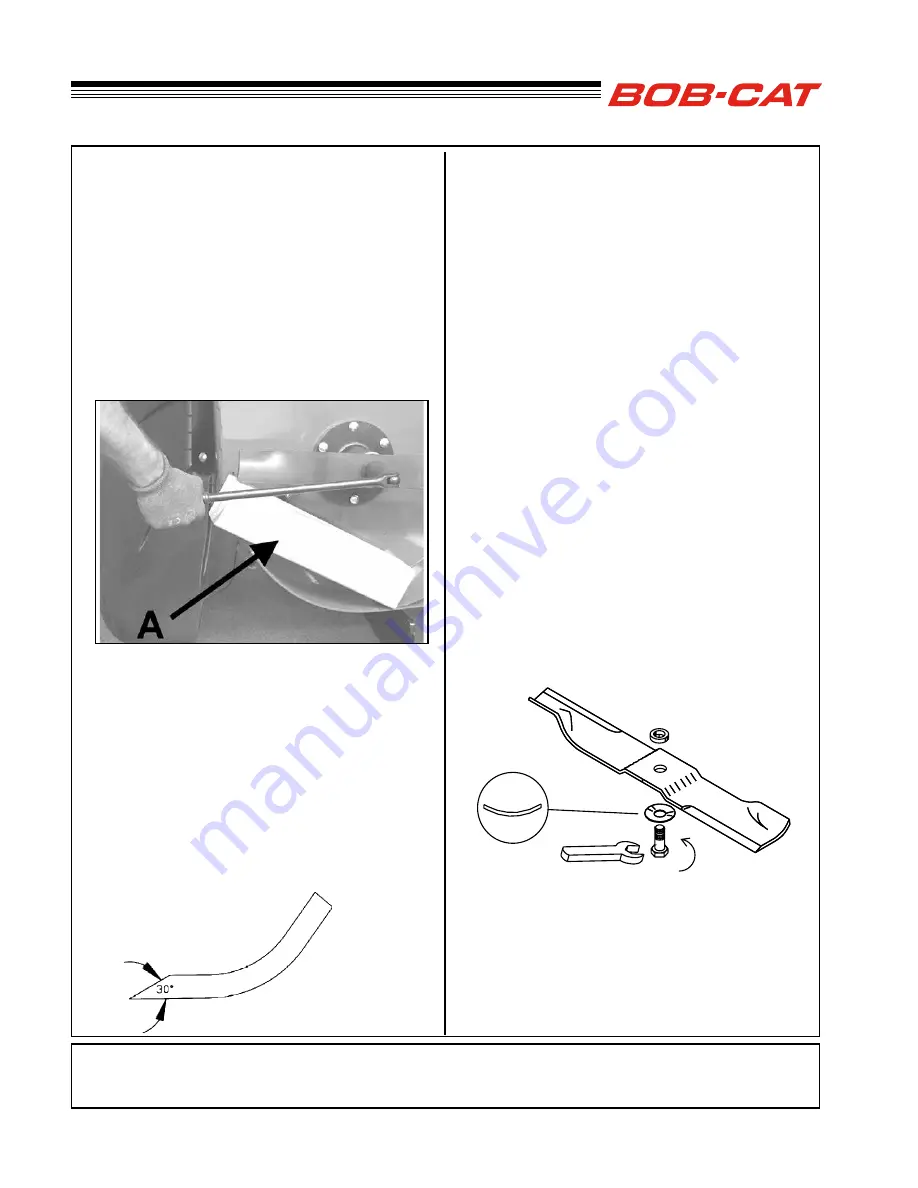
30
BLADE REMOVAL
Follow these instructions to prevent injury during
blade removal:
1. Loosen with a box wrench or a socket and long
breaker bar. To gain additional leverage, slip a
long pipe or thick-walled tube over breaker bar or
wrench.
2. Insert wood block
A
as shown, to prevent blade
from turning when loosening.
3. Wear thickly padded gloves. Keep hands clear
of blade path. Blades may rotate when bolt
releases.
SHARPENING
Blades may be sharpened by filing or grinding.
-
Inspect blades before sharpening.
-
Replace bent or cracked blades.
-
Replace blades when the lift portion has worn
thin.
-
Maintain cut angle at 30
o
.
-
Do not overheat blades when sharpening.
-
Always use BOB-CAT blades. Use of another
manufacturer’s blades may be dangerous.
BLADE BALANCE
Blade balance must be maintained at 5/8 oz-in
(19.4 g-cm) or less. Failure to keep blades balanced
causes excess vibration, wear, and shortened life of
most components of the machine.
To balance a blade:
1. Sharpen blade first.
2. Balance the blade at the center.
3. Attach a 1/8 oz (3.9 g) weight at a distance 5”
(127 mm) from center on the light end. This
should make the light end the heavy end:
- If it does, the blade is balanced.
- If does not, file or grind the heavy end until
the addition of the weight makes the light end
the heavy end.
BLADE INSTALLATION
1. Wear thickly padded gloves to prevent cuts from
the sharp blade.
2. Insert the blade bolt, in order, through the conical
washer (cup side toward the blade, as shown),
the blade, and the blade spacer.
3. Install assembly on the blade spindle.
4. Torque the blade bolt to 70 ft-lbs.
BELTS
All belts are tensioned by spring loaded idlers. No adjustment is required.
MAINTENANCE
BLADE BOLT TORQUE: 70 FT-LBS (95 Nm)
Summary of Contents for 9995010
Page 47: ...45 PARTS SECTION PARTS SECTION ...
Page 50: ...48 FIGURE 2 BUMPER WRAP 4 3 6 2 7 8 9 10 1 5 5 ...
Page 70: ...68 FIGURE 12 FOLDING ROPS 10 7 5 2 6 13 1 14 1 11 3 1 4 9 8 7 5 3 2 9 4 6 12 15 15 ...
Page 82: ...80 FIGURE 18 DECALS 9 7 17 6 10 13 12 11 1 5 4 6 8 2 3 6 6 16 18 14 20 19 15 ...
Page 84: ...82 7 6 5 4 3 2 1 8 8 4 10 11 12 6 9 13 FIGURE 19 DECALS ...