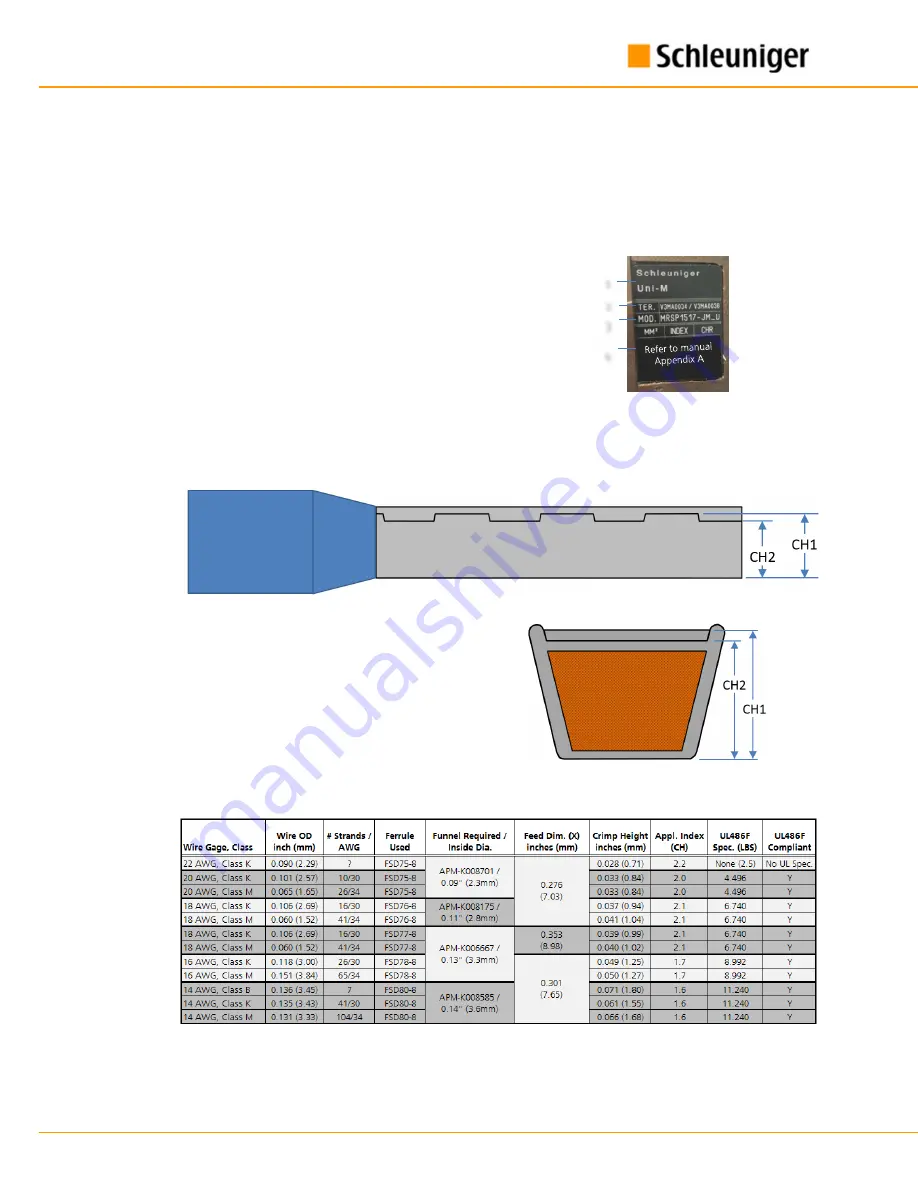
12 Electrical schematics
Operating Instructions | Version 1.0 (05-2018) | Uni-M Ferrule
30 | 32
10
APPENDIX A: PANDUIT END FERRULE SPECIFICATIONS
10.1
IDENTIFICATION PLATE – PANDUIT FERRULE APPLICATORS
The rating plate with serial number is on the right side of the product and contains the following information.
(Note: The identification plate shown here is only an example. Please refer to the delivered product for accu-
rate settings and readings.)
1.
Name of supplier and product name
2.
Terminal number
3.
Applicator model and serial number
4.
Reference for crimp parameters.
5.
``
10.2
VERIFY/ADJUST CRIMP HEIGHT
1.
Typically in a ferrule crimp there are low spots (CH1) and high spots (CH2) as seen in Fig. 4.
Fig. 4
2.
When using
Panduit end ferrules
, crimp
height should be measured at the high
spot (CH1) using standard micrometers.
10.3
CRIMP PARAMETERS AND SETTINGS FOR PANDUIT FERRULES
1
2
3
4