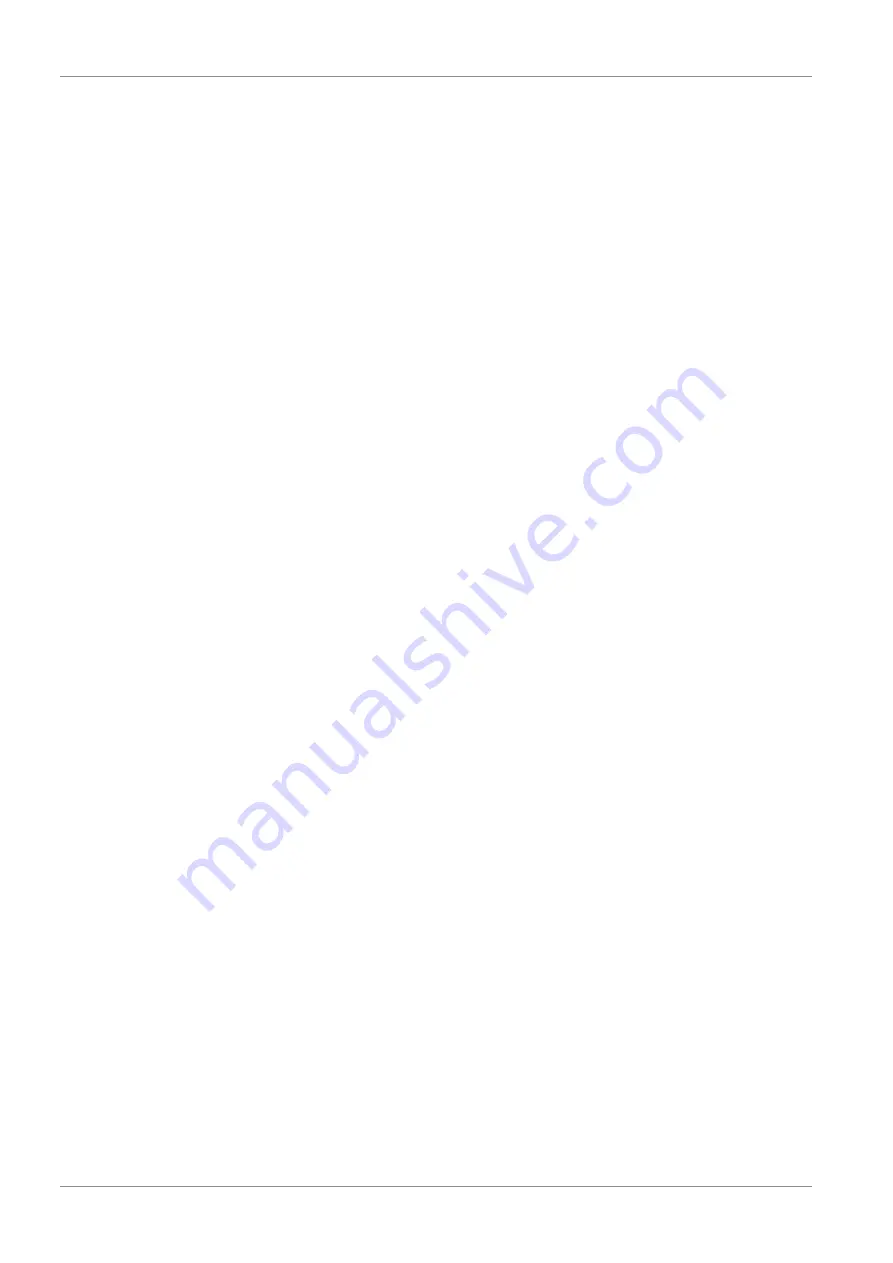
Operating Modes
22 / 72
EN-US · 30.30.01.02084 · 02 · 12/20
6.2.1 Process Data
The cyclical process data is used to control the ejectors and receive current information reported from the
ejector. There is a difference between the input data (Process Data In) and the controlling output data
(Process Data Out).
The input data Process Data In is used to report the following information cyclically:
•
Vacuum limit values H1 and H2
•
CM-Autoset acknowledgment
•
EPC-Select acknowledgment
•
The ejector device status in the form of a status traffic light
•
Multifunctional EPC values
The output data Process Data Out is used to control the ejector cyclically:
•
Vacuum on/off
•
Blow off active
•
Setup mode
•
CM Autoset
•
EPC-Select: switching the multifunctional EPC values
•
Switching production setup profiles P0–P3
•
Inlet pressure in 0.1 bar (measured value from external pressure sensor, 0 = function inactive)
A detailed description of the process data can be found in the data dictionary.
The corresponding device description file (IODD) is available for integration into a higher-level control
unit.
6.2.2 Parameter Data
In addition to the process data that is exchanged automatically, the IO-Link protocol provides an acyclical
data channel for identification data, setting parameters or general feedback from the device. The avail-
able data objects are referred to as ISDU with IO-Link and are to be uniquely addressed within a device
through their index and subindex.
Controller manufacturers usually provide a specialized function module – e.g. the “IOL_CALL” module for
Siemens controllers – to enable these parameters to be accessed from a control program.
Information about which parameter data the device provides and how this data is displayed as ISDU ob-
jects can be found in the “Data Dictionary”.
6.2.3 IO-Link
The ejector can be operated in IO-Link mode to enable intelligent communication with a controller. The
ejector’s parameters can be set remotely using IO-Link mode. The energy and process control (EPC) func-
tion is also available in IO-Link mode. It is divided into 3 modules:
•
Condition monitoring (CM): Condition monitoring to increase system availability
•
Energy monitoring (EM): Energy monitoring to optimize the vacuum system’s energy consumption
•
Predictive maintenance (PM): Predictive maintenance to increase the performance and quality of the
gripping systems