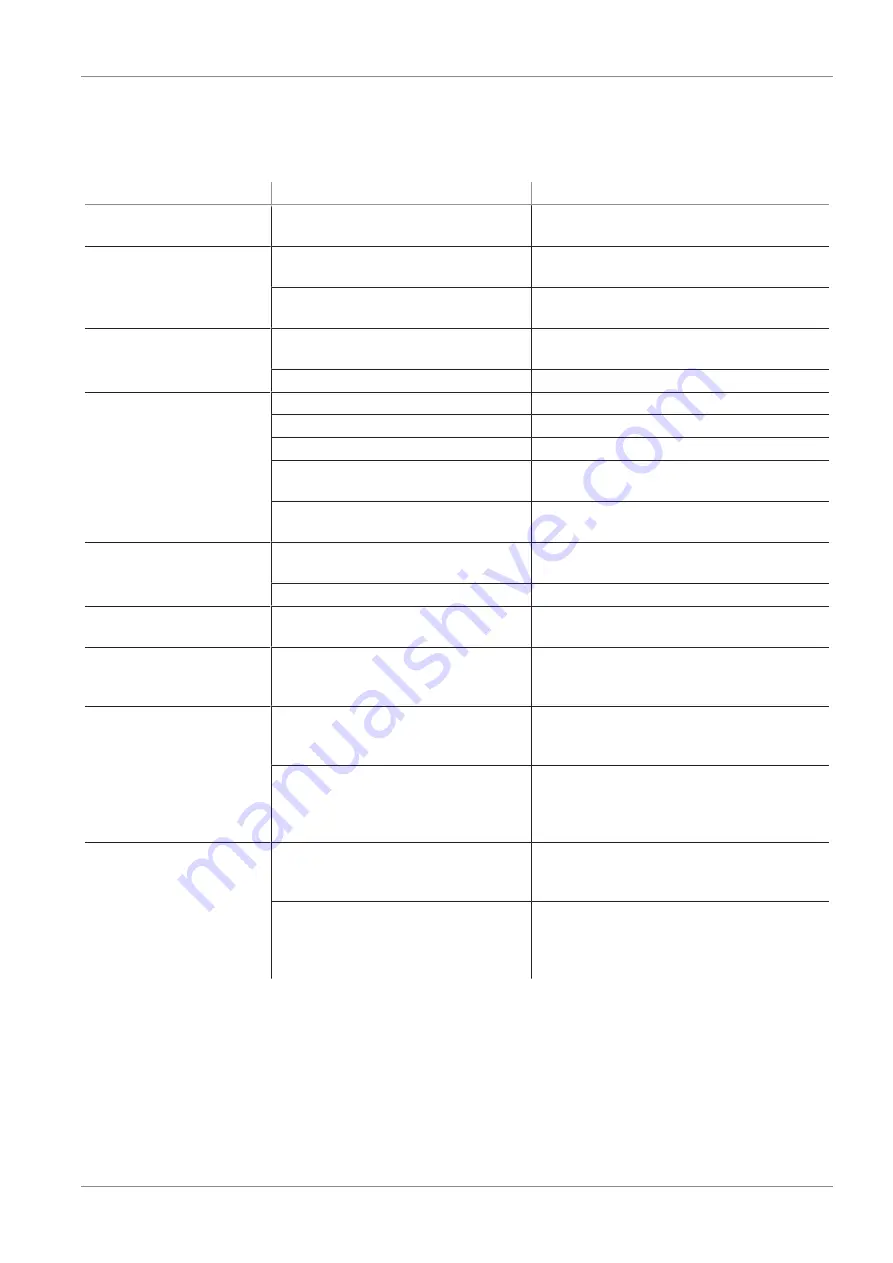
Troubleshooting
EN-US · 30.30.01.01963 · 00 · 05/19
41 / 52
10 Troubleshooting
10.1 Help with Malfunctions
Malfunction
Possible cause
Solution
Power supply disrupted
Electrical connector
4
Make sure device is properly con-
nected to power
No communication
Incorrect electrical connection
4
Check electrical connection and pin
assignment
Higher-level controller not cor-
rectly configured
4
Check the controller configuration
Ejector does not re-
spond
No power supply
4
Check electrical connection and pin
assignment
No compressed air supply
4
Check the compressed air supply
Vacuum level is not
reached or vacuum is
built up too slowly
Silencer is dirty
4
Replace the silencer
Leakage in hose line
4
Check hose connections
Leakage at suction cup
4
Check suction cup
Operating pressure too low
4
Increase operating pressure. Note
the maximum limits!
Internal diameter of hose line too
small
4
Observe recommendations for hose
diameter
Load cannot be held
Vacuum level too low
4
Increase the control range for the
air saving function
Suction cup too small
4
Select a larger suction cup
No display on the
screen
Faulty electrical connection
4
Check electrical connection and pin
assignment
Display shows error
code
See "Error codes" table
4
See "Error Codes" table in the fol-
lowing chapter
Warning message
“Leakage too high”
even though handling
cycle is working opti-
mally
Limit value -L- (permissible leak-
age per second) set too low
4
Determine typical leakage values in
a good handling cycle and set as
limit value
Limit values SP1 and rP1 for leak-
age measurement set too low
4
Set limit values in such a way that
there is a clear differentiation be-
tween the neutral and suction sys-
tem states.
Warning message
“Leakage too high”
does not appear al-
though there is high
leakage in the system
Limit value -L- (permissible leak-
age per second) set too high
4
Determine typical leakage values in
a good handling cycle and set as
limit value
Limit values SP1 and rP1 for leak-
age measurement set too high.
4
Set limit values in such a way that
there is a clear differentiation be-
tween the neutral and suction sys-
tem states.