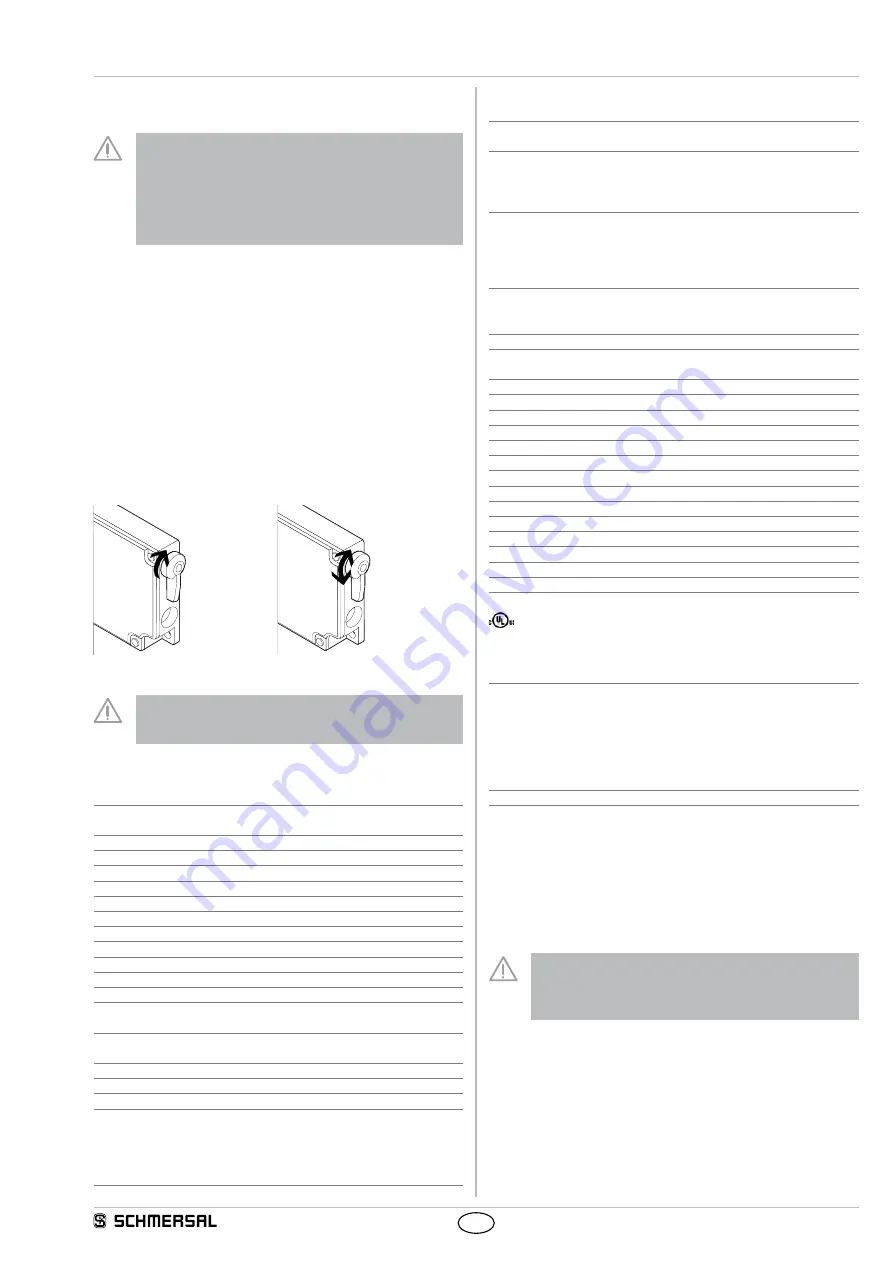
3
AZM 161 AS
Operating instructions
Solenoid interlock
EN
Emergency release
(Mounting and actuation only outside of the safety guard)
The emergency release should only be used in an
emergency. The solenoid interlock should be installed and/
or protected so that an inadvertent opening of the interlock
by an emergency release can be prevented. The emergency
release must be clearly labelled that it should only be used
in an emergency. The label can be used that was included in
the delivery.
To realise an emergency release, turn the orange lever by 180° in the
direction shown by the arrow until it hits the end stop. In this position,
the safety guard can be opened. The lever is latched and cannot be
turned back. To cancel the blocking condition, the central mounting
screw must be loosened to such extent that the lever can be turned
back into its original position. Return the lever to its original position and
firmly retighten the screw.
Emergency exit
(Fitting and actuation only from within the hazardous area)
To realise an emergency exit, turn the orange lever by 180° in the
direction shown by the arrow until it hits the end stop. In this position,
the safety guard can be opened. The blocked position is cancelled by
turning the lever in the opposite direction. In unlocked position, the
safety guard is protected against unintentional closing.
Emergency release (N)
Emergency exit (T)
The user must evaluate and design the safety chain in
accordance with the relevant standards and the required
safety level.
2.4 Technical data
Standards:
IEC 60947-5-1, ISO 14119, EN 62026-2,
ISO 13849-1, IEC 61508
Enclosure:
glass-fibre reinforced thermoplastic,
self-extinguishing
Actuator and locking bolt:
stainless steel 1.4301
Mechanical life:
> 1 million operations
Holding force F:
2000 N
Latching force:
30 N, only for option R
Coding level according to ISO 14119:
low
Protection class:
IP67 to IEC 60529
Insulation Protection class:
II
X
Overvoltage category:
III
Degree of pollution:
3
Termination:
Connector M12 x 1, 4 pole
Electrical data AS-Interface:
Operating voltage range:
18.0 ... 31.6 VDC, through AS-Interface,
reverse polarity-proof
AS-interface power consumption:
max. 0.25 A,
- ordering suffix „P“:
max. 0.1 A
Rated insulation voltage U
i1
:
32 VDC
Rated impulse withstand voltage U
imp1
:
800 V
Device insulation:
internal short-circuit proof
Specification (V 2.1):
AS-i slave profile: S-7.B.E,
IO code: 0x7,
ID code: 0xB,
ID code1: 0xF,
ID code2: 0xE
AS-interface inputs:
Databits D0...D3: condition static 0 or dynamic
code transmission SaW
AS-interface outputs:
Bit 0: magnet control solenoid interlock;
Bit 1 ... Bit 3: no function
Parameter port:
P0: actuator identified
P1: solenoid interlock locked
P2: magnet voltage in tolerance range
P3: error message "locking/unlocking of the solenoid interlock blocked"
Diagnostic information:
LED yellow: Channel 1 / AS-i SaW Bit 0,1
LED green / red (AS-i Duo LED): AS-Interface supply voltage /
AS-Interface communication error
slave address = 0 or periphery error
LED yellow: Channel 2 / AS-i SaW Bit 2,3
Input module address:
preset to address 0,
can be changed through AS-interface bus master
or hand-held programming device
Auxiliary voltage magnet:
only ordering suffix "P"
Operating voltage range:
24 VDC -15% / +10%
(stabilised PELV units)
Power consumption AUX:
max. 0.5 A
Rated insulation voltage U
i2
:
32 VDC
Rated impulse withstand voltage U
imp2
:
800 V
Device fuse rating:
≤ 4 A when used to UL 508
Magnet:
100% ED
Ambient conditions:
Ambient temperature:
−25 °C ... +60 °C
Storage and transport temperature:
−25 °C ... +85 °C
Relative humidity:
30 ... 95 %, no condensation
Resistance to vibration:
10 ... 150 Hz, amplitude 0.35 mm
Resistance to shock:
30 g / 11 ms
Switching frequency f:
≤ 1 Hz
Switch-off delay:
< 100 ms
Actuating speed:
≤ 2 m/s
Use Type 4X (Indoor Use) and 12 connector fittings.
2.5 Safety classification of the interlocking function
Standards:
ISO 13849-1, IEC 61508
Intended structure:
- If a fault exclusion of a hazardous damage to the 1-channel
mechanics is authorised and sufficient protection against tampering is
ensured:
applicable up to cat. 3 / PL d / SIL 2
- PFH:
1.01 x 10
-7
/ h for ≤ 100,000 operations / year
- Basically:
applicable up to cat. 1 / PL c / SIL 1
- PFH:
1.14 x 10
-6
/ h for ≤ 100,000 operations / year
Mission time:
20 years
2.6 Safety classification of the guard locking function
If the device is used as an interlock for personal safety, a safety
classification of the guard locking function is required.
When classifying the guard locking function, a distinction must be
made between monitoring of the interlocking function and control of the
release function.
The following classification of the release function is based on the
principle of isolating the supply of power to the solenoid.
The safety classification for the release function only applies
to devices with monitored interlock function, in power to
unlock version and with solenoid supply from 24 VDC (AUX)
(see ordering code).
By reliably isolating the power externally, it can be assumed that no
errors can occur with regard to actuation of the release function. In that
case, the device does not contribute towards the failure probability of
the release function.
The level of safety of the release function relies, therefore, exclusively
on reliable external deactivation of the power.