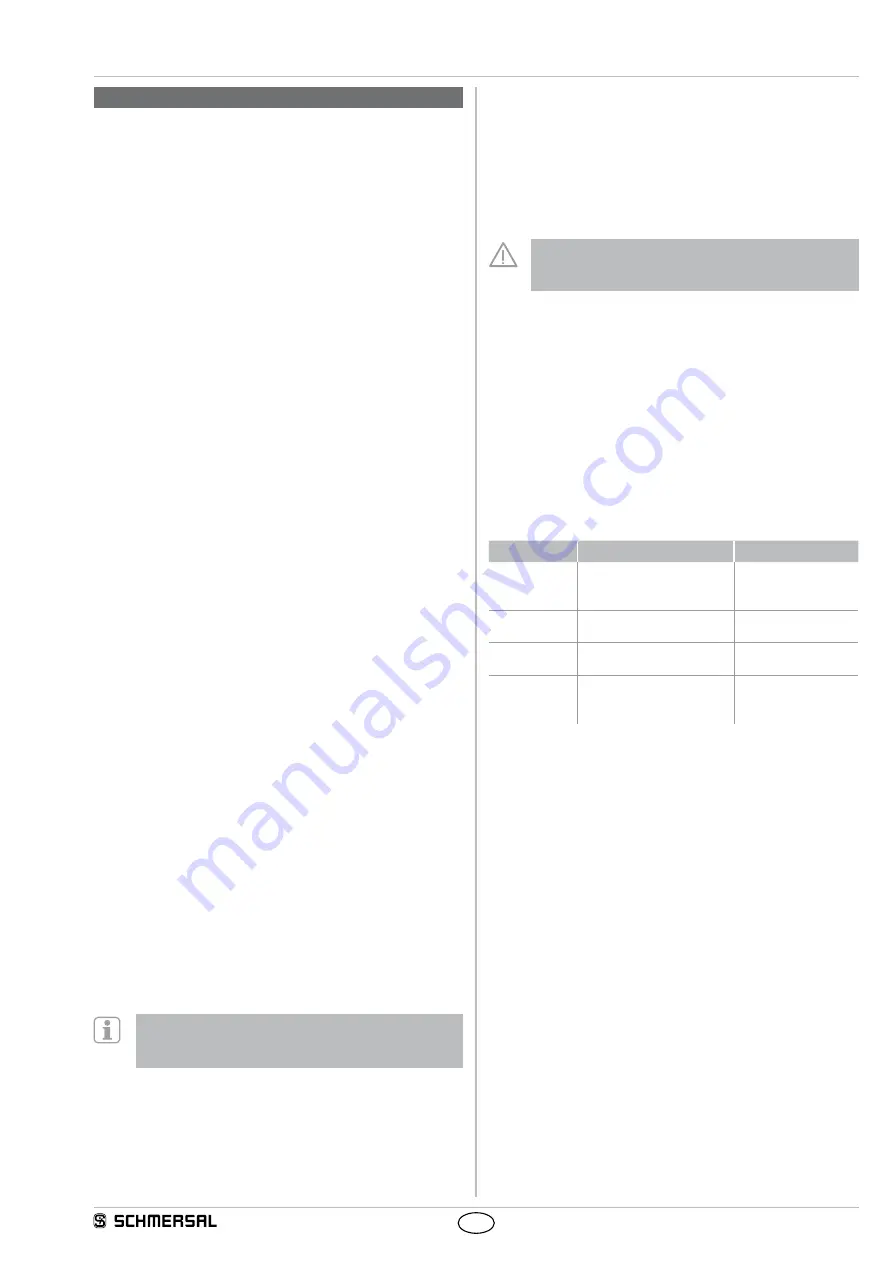
5
AZM 161 AS
Operating instructions
Solenoid interlock
EN
5. Functions and configuration
5.1 Mode of operation of the safety outputs
AZM 161 Z ST-AS
The safety outputs of the AS-i safety monitor are enabled, when the
following conditions are met:
• the actuator is inserted
• the solenoid interlock is locked
AZM 161 B ST-AS
The safety outputs of the AS-i safety monitor are enabled, when the
following conditions are met:
• the actuator is inserted
AZM 161 BZ ST-AS
The safety outputs of the AS-i safety monitor are only activated, when
both AS-i half-codes are enabled.
Half-code 1 (AS-i SaW bit 0,1) is enabled, when:
• the actuator is inserted
The solenoid interlock now can be locked.
Half-code 2 (AS-i SaW bit 2,3) is enabled, when:
• the solenoid interlock is additionally locked.
5.2 Magnet control
The control system with the AS-Interface Master can lock and unlock
the solenoid interlock through the output bit 0 of the addressed AS-i
slave AZM 161 AS. In the power to lock variant of the AZM 161 AS,
the functional set of output bit 0 will cause the solenoid interlock to be
locked. In the power to unlock variant of the AZM 161 AS, the functional
set of output bit 0 will cause the solenoid interlock to be unlocked.
5.3 Programming the slave address
The slave address is programmed through the M12 connector. Any
address from 1 to 31 can be set by means of the AS-i bus master or a
hand-held programming device.
5.4 Configuration of the safety monitor
Depending on the component used, the AZM 161 AS can be configured
in the ASIMON configuration software with the following monitoring
devices (also refer to the ASIMON manual).
Double channel dependent with filtering
Suitable for: AZM 161 B ST-AS
The use of this monitoring device is especially advantageous on safety
guards where bounce or vibration against the mechanical stop upon
closing is a problem.
• Optionally with startup test
• Stabilisation time typically 0.5 up to 1.0 s
• Synchronisation time typically 5.0 up to 10 s
The safety-monitoring module is only released after expiration of the
stabilising time; the synchronization time always must exceed the
stabilising time.
Double channel conditionally dependent
Suitable for: AZM 161 BZ ST-AS
• Independent: In - 1
As long as the actuator remains inserted, the safety guard can be
relocked at any time, in which case the safety outputs are reactivated.
The safety guard must not be opened.
The redundancy and the "Safety guard closed" signal are not
tested in this configuration. To test these conditions, additio-
nal measures must be taken beyond the safety monitor .
Double channel dependent
Suitable for: AZM 161 Z ST-AS, AZM 161 B ST-AS, AZM 161 BZ ST-AS
• Synchronisation time typically: 0.1 s;
for AZM 161 BZ ST-AS infinite (∞)
• Optionally with startup test
• Optional with local acknowledge
When the AZM 161 BZ ST-AS is used together with this monitoring
device for conducting the start-up test prior to every restart, the safety
guard must be opened.
The configuration of the safety monitor must be tested and
confirmed by a qualified and authorised safety expert/safety
engineer.
5.5 Status signal "safety release"
The "safety release" status signal from a Safety at Work slave can be
cyclically queried by the control system through the AS-i master. To that
effect, the 4 input bits with the varying SaW code of a Safety at Work slave
are evaluated through an OR operation with 4 inputs in the control system.
5.6 Read-out of the parameter port
The parameter port P0 to P3 of a solenoid interlock can be read
out through the control interface of the AS-i master (see component
description) by means of the "Write parameter" instruction (with
hexadecimal value F). This non-safe diagnostic information from the
reflected parameters or the answer to a "Write parameter instruction" can
be used by the user for diagnostic purposes or for the control programme.
Parameter bit Condition = 1
Condition = 0
0
Actuator inserted. The
actuator can now be locked.
No actuator detected
1
Actuator inserted and
locked
Actuator not locked
2
Magnet voltage available
Magnet voltage not
available
3
Locking/unlocking of the
solenoid interlock blocked
Locking/unlocking of
the solenoid interlock
not blocked
Error message "locking/unlocking of the solenoid interlock blocked"
This error is transmitted, when the solenoid interlock no longer can be
correctly locked or unlocked. The causes for this error can be: the safet
yguard is not correctly closed, the actuator is deformed, the manual
release is not correctly reset or the auxiliary voltage is missing. This
error is transmitted as "periphery error" to the control system through
the AS-i Master. A "periphery error" is shown on the AS-i device by the
alternating red/green flashing of the AS-i Duo LED.
AZM 161 Z ST-AS .A.
Z-variant, power to lock
(magnet-operated locking)