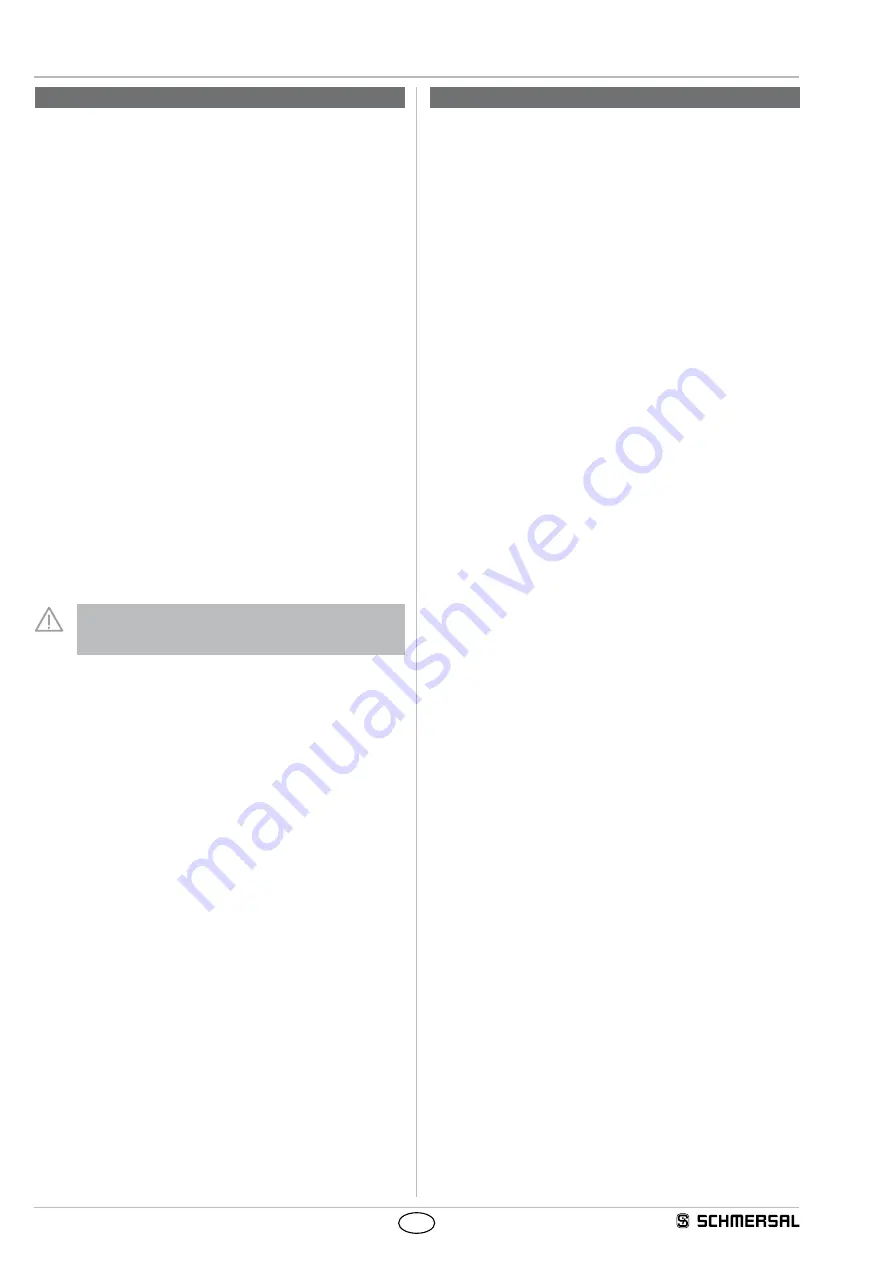
10
Operating instructions
Solenoid interlock
AZM400
EN
7. Set-up and maintenance
7.1 Functional testing
The safety function of the safety components must be tested.
The following conditions must be previously checked and met:
1. Check max. axial misalignment of actuator and solenoid interlock.
2. Check max. angle displacement.
3. Make sure that it is not possible to lift the actuator in the Z axis above
the extended bolt.
4. Check for tight installation of the actuator and the switch.
5. Fitting and integrity of the cable connections.
6. Check the switch enclosure for damage.
7. Remove particles of dust and soiling.
8. For versions with emergency exit, the following should also be
considered: It must be possible to open the guard system from within
the hazardous area; it must not be possible that the guard system is
blocked from the inside.
7.2 Maintenance
In the case of correct installation and adequate use, the safety
switchgear features maintenance-free functionality.
A regular visual inspection and functional test, including the following
steps, is recommended:
1. Check for tight installation of the actuator and the switch.
2. Check max. axial misalignment of actuator and solenoid interlock.
3. Check max. angle displacement.
4. Make sure that it is not possible to lift the actuator in the Z axis above
the extended bolt.
5. Fitting and integrity of the cable connections.
6. Check the switch enclosure for damage.
7. Remove particles of dust and soiling.
Measures must be taken to protect against manipulation or
against the bypassing of safety device, for example, using an
extra actuator.
Damaged or defective components must be replaced.
8. Disassembly and disposal
8.1 Disassembly
The safety switchgear must be disassembled in a de-energised
condition only.
8.2 Disposal
The safety switchgear must be disposed of in an appropriate manner in
accordance with the national prescriptions and legislations.