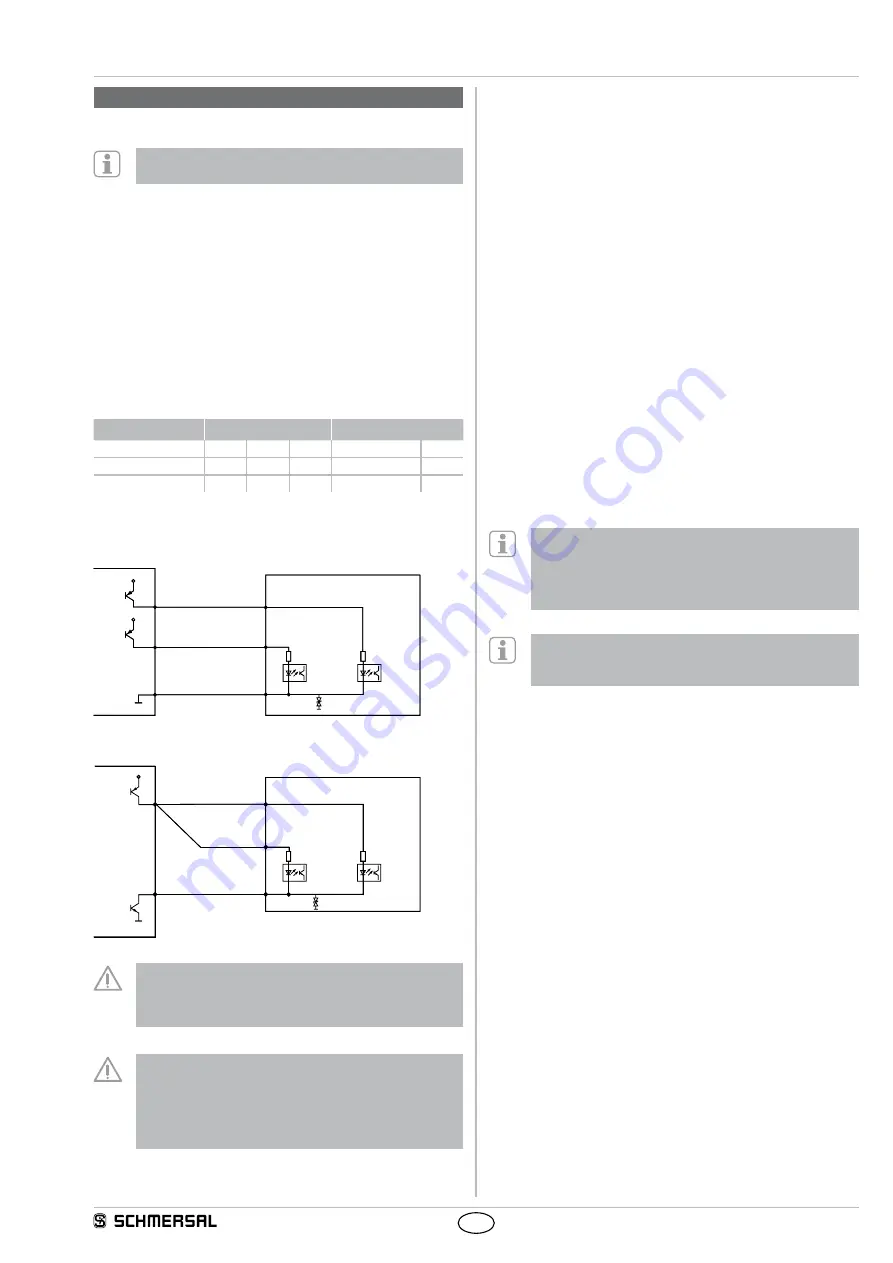
7
AZM400
Operating instructions
Solenoid interlock
EN
4. Rear side Electrical connection
4.1 General information for electrical connection
The electrical connection may only be carried out by
authorised personnel in a de-energised condition.
The voltage inputs A1 (and H1 with the AZM400Z-ST2..), and the
control inputs E1, E2 and E3 must have a permanent protection against
over-voltage. The use of PELV supply units according to IEC 60204-1
is recommended. The safety outputs can be integrated into the safety
circuit of the control system.
4.2 Control options in the normal operating mode
Due to the control inputs E1, E2 and E3 for controlling the guard locking
function it is possible to use different control options to be able to drive
the AZM400 with a different safety controller. The function of the control
inputs is the same for both ST and ST2 versions.
Setting the operational control inputs according to the following table
causes the interlock to unlock.
Input condition
Version P/P
Version P/N
E1
E2
E3
E1 = E2
E3
Lock
open
open
GND
open
open
Unlock
24 V
24 V
GND
24 V
GND
Use of safety outputs of the type P/P:
Safety controller
AZM400
P2
N
E1 (2)
E2 (8)
E3 (6)
Inp 2
Inp 1
P1
GND
24 V
24 V
Use of safety controls of the type P/N:
Safety controller
AZM400
Inp 1
P
N
E1 (2)
E2 (8)
E3 (6)
Inp 2
GND
24 V
The outputs used for the control must correspond to the
Performance Level (PL) of the guard system.
To achieve the PL e the control must have tested outputs as
these are not tested by the AZM400.
Independent of the version used, the notes in the Operating
Instructions of the used controller should be observed.
These could include:
- Shielded installed cable
- Minimum test interval every 24 hours
- etc.
Block drive
If the locking bolt does not reach the "locked" condition with the first
attempt, the AZM400 makes an autonomous attempt. If the second
attempt also fails, the AZM400 signals a fault (comp. table 2).
After a malfunction, condition of the control inputs has to be changed to
allow the locking bolt to be driven out again.
When the guard system closes slowly, a block drive can occur if the
actuator that is opening is not in front of the bolt being driven out (see
Chapter "Operating equipment and distances").
Unlocking after Power On
If after switching on, the AZM400 is already in the locked position, the
device must first be unlocked and then locked again. This is to verify
the causality of the drive signals and to check the sufficient depth of
the locking bolt. The yellow LED flashes after power-on in the locked
position.
4.3 Requirements for the connected safety-monitoring module
• Dual-channel safety input, suitable for 2 p-type semi-conductor
outputs (OSSD)
The solenoid interlock cyclically switch off the safety output to test
them. The safety-monitoring module therefore does not need to be
equipped with a cross-wire short detection. The test impulse time of
≤ 0.4 ms must be tolerated by the evaluation. The test impulse, the
switch-off time of the solenoid interlock can be extended depending on
the cable length and the capacity of the cable used.
Configuration of the safety controller
If the solenoid interlock is connected to electronic safety-
monitoring modules, we recommend that you set a discrepancy
time of 100 ms. The safety inputs of the safety-monitoring
module must be able to blank a test impulse of < 1 ms.
Information for the selection of suitable safety-monitoring
modules can be found in the Schmersal catalogues or in the
online catalogue on the Internet: www.schmersal.net.