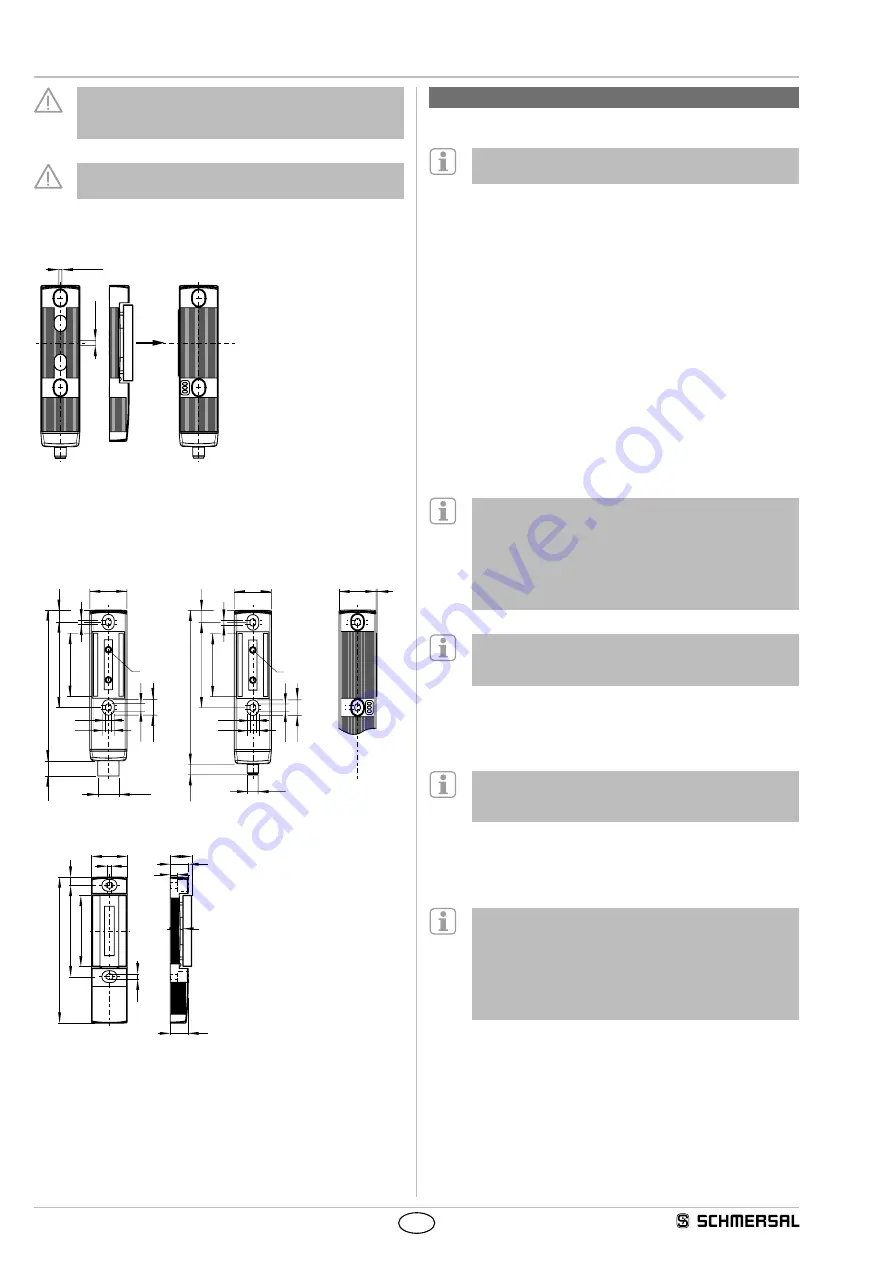
4
Operating instructions
Solenoid interlock
MZM 100
MZM 100 B
EN
At an ambient temperature of ≥ 50 °C, the safety
component must be fitted so that it is protected against
unintentional contact with persons
The safety component must be operated in the operating
direction of the latching force (refer to image)
Axial misalignment and operating direction of the latching force
±
5m
m
±
3 mm
3.2 Dimensions
All measurements in mm
Solenoid interlock
40
6.2
68
92
162.5
16.3
13
5
40
1
M
M23
15.6
10.6
ST2
11.2
40
M12
68
92
165.5
11.8
13
5
M
6.2
15.6
10.6
11.2
ST
Actuator
40
24
20
5
3
10
0
16
0
9
78
20
6.2
8
Key
M Permanent magnet
4. Electrical connection
4.1 General information for electrical connection
The electrical connection may only be carried out by
authorised personnel in a de-energised condition
The voltage inputs A1, X1, X2 and IN must have a protection against
permanent overvoltage supply units according to IEC 60204-1 is
recommended
The safety outputs can be integrated into the safety circuit of the control
system For applications of PL e / control category 4 to ISO 13849-1,
the safety outputs of the safety switchgear or the chain of components
must be connected to a safety-monitoring module of the same category
Requirements for the connected safety-monitoring module:
• Dual-channel safety input, suitable for 2 p-type semi-conductor
outputs
• Digital inputs to EN 61131-2, Table "Standard operating ranges for
digital inputs (current sinking)"
•
Test function
The safety-monitoring module must tolerate internal functional tests
of the solenoid interlock with cyclic switch-off of the safety outputs for
max 2 ms (typically < 1 ms) The switch-off stage of the test cycle is
temporarily reduced by an active ohmic discharge of the cable
If the safety sensor is connected to electronic safety-
monitoring modules, we recommend that you set a
discrepancy time of min 100 ms The safety inputs of the
safety-monitoring module must be able to blank a test impulse
of approx 1 ms The safety-monitoring module does not need
to have a cross-wire short monitoring function, if necessary,
the cross-wire short monitoring function must be disabled
Information for the selection of suitable safety-monitoring
modules can be found in the Schmersal catalogues or in the
online catalogue on the Internet: wwwschmersalnet
If the solenoid interlock is wired to relays or to non-safety relevant
control components, a new risk analysis must be carried out
Cable design in case of serial diagnostics
On wiring SD devices, pay attention to the voltage drop on
the cables and the current carrying capacity of the individual
components
The wiring capacity of the connecting cable of the solenoid interlock
must not exceed 50 nF Depending on the strand structure, normal
unshielded 30 m long control cables LIYY 025 mm² to 15 mm² have a
wiring capacitance of approx 3 … 7 nF
Accessories for the series-wiring
For convenient wiring and series-wiring of SD components,
the SD junction boxes PFB-SD-4M12-SD (variant for the
field) and PDM-SD-4CC-SD (variant for control cabinet on
carrier rail) are available along with additional comprehensive
accessories Detailed information available on the internet at
wwwschmersalnet