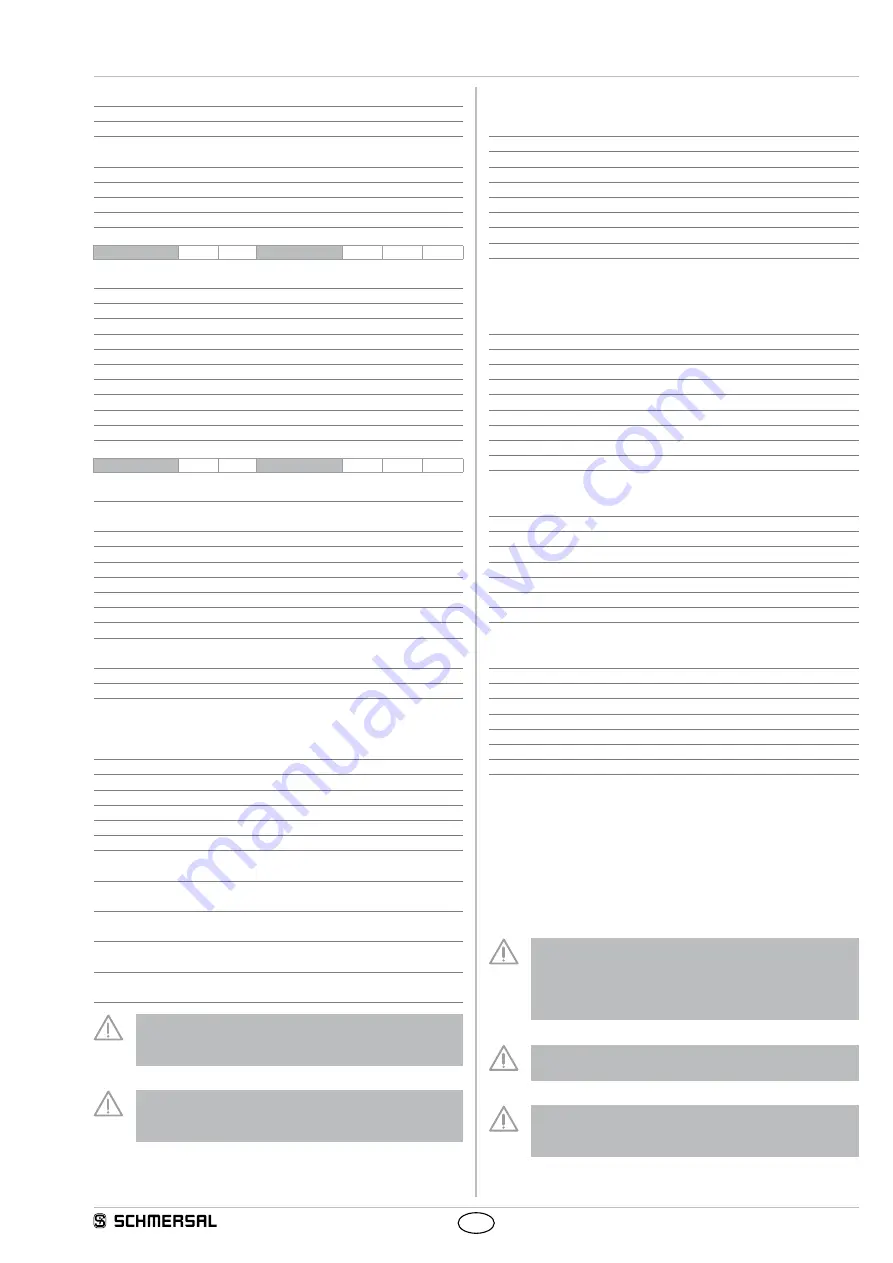
3
SFB-PN-IRT-8M12-IOP
Operating instructions
Safety fieldbox
EN
Test pulse outputs:
Y1 and Y2
Switching elements:
p-type, short-circuit proof
Rated operating voltage U
e
:
24 VDC
Rated operating current I
e
:
Y1: 15 mA
Y2: 10 mA at 24 V/30 mA at GND
Leakage current I
r
:
≤ 0.5 mA
Voltage drop U
d
:
≤ 3 V
Test pulse duration:
≤ 1 ms
Test pulse interval:
500 ms
Classification:
ZVEI CB24I
Source:
C1
Sink:
C1
Digital output:
DO
Switching elements:
2 p-type, short-circuit proof
Utilisation category:
DC-12 / DC-13
Rated operating voltage U
e
:
24 VDC
Rated operating current I
e
:
0.8 A
Leakage current I
r
:
≤ 0.5 mA
Voltage drop U
d
:
≤ 1 V
Inductive load:
≤ 400 mH
Switching frequency output:
≤ 1 Hz
Test pulse duration:
≤ 1 ms
Test pulse interval:
15 … 250 ms
Classification:
ZVEI CB24I
Source:
C1
Sink:
C1
Diagnostics input/FB interface:
DI
Switching thresholds:
−3 V … 5 V (Low)
13 V … 30 V (High)
Current consumption per input:
< 12 mA / 24 V
Permissible residual drive current:
< 1.0 mA
Input debounce filter:
10 ms
FB interface data transmission rate:
19.2 kBaud
Power supply devices:
A1 and A2
Rated operating voltage U
e
:
24 VDC
Rated operating current I
e
:
0.8 A
Device port line fuse:
1.5 A
(integrated automatic resettable fuse)
Electrical data – PROFINET P1/P2
Field bus protocol:
PROFINET / PROFIsafe
Specification:
- PROFINET:
V2.3, Conformance class C
- Supported options:
MRP, fast start-up
- PROFIsafe
V2.4
Network load class, PROFINET:
3
Transmission rate:
100 Mbit/s Full Duplex
PROFINET addressing:
via DCP
Integrated switch:
Dual port, 100 Mbit/s, IRT-capable
Supported PROFINET services:
I&M0 to I&M3, SNMP, LLDP
Service interface:
Web interface HTTP
LED indications
8 x LED green/red 'E':
Error LED, device port
8 x LED yellow 'I':
Input LED, device port
2 x LED green 'L':
Link LED, Ethernet port
2 x LED green 'A':
Activity LED, Ethernet port
1 x LED green/red 'SF':
System fault LED
1 x LED red 'BF':
Bus fault LED
1 x LED green/red 'Err':
Error LED, fieldbox
1 x LED green 'Pwr':
Power LED, fieldbox
The sum of the total current of the individual device ports
X0 – X7 for outputs A1 (power supply to devices) and DO
(digital output) should not exceed 850 mA.
Protection class IP67 is only reached if all M12 connectors
and blanking plugs, as well as the viewing window are
properly fastening with screws.
2.4 Safety classification
- Safety inputs, 2-channel:
Standards:
IEC 61508, IEC 62061, ISO 13849-1
PL:
e
Control Category:
4
DC:
99 %
PFH:
2.9 x 10
-9
/h
PFD
avg
:
2.5 x 10
-4
SIL:
suitable for SIL 3 applications
Mission time:
20 years
Response time of local safety input > PROFINET:
20 ms
The SFB fulfills the requirements as PDDB according to IEC 60947-5-3
in combination with magnetic sensors (2 NC contacts) up to PL e / SIL 3.
- Safety inputs, 1-channel:
Standards:
IEC 61508, IEC 62061, ISO 13849-1
PL:
d
Control Category:
2
DC:
90 %
PFH:
2.3 x 10
-7
/h
PFD
avg
:
2.0 x 10
-2
SIL:
suitable for SIL 1 applications
Mission time:
20 years
Response time of local safety input > PROFINET:
20 ms
Test interval for error detection:
10 s
- Safety outputs, 1 cable (PL d):
Standards:
IEC 61508, IEC 62061, ISO 13849-1
PL:
d
Control Category:
3
PFH:
1.0 x 10
-7
/h
PFD
avg
:
8.8 x 10
-3
SIL:
suitable for SIL 2 applications
Mission time:
20 years
PROFINET reaction time > local safety output:
50 ms
- Safety outputs, 2 cables (PL e):
Standards:
IEC 61508, IEC 62061, ISO 13849-1
PL:
e
Control Category:
4
PFH:
2.9 x 10
-9
/h
PFD
avg
:
2.5 x 10
-4
SIL:
suitable for SIL 3 applications
Mission time:
20 years
PROFINET reaction time > local safety output:
50 ms
Safety response times, SFB
The overall reseponse time of a safety function is made up of the
following:
• Response time of the connected safety switchgear
• Delay time of the safety fieldbox SFB-PN (WCDT_Input ≤ 20 ms)
• PROFINET/PROFIsafe transmission time
• Cycle time F runtime group F-PLC
• Response time of safety shut-off element (actuator)
In addition to the maximum response time of the SFB-PN,
the response times of the connected safety switchgear, the
transmission time from PROFINET and the response times
of additional PROFIsafe components (if applicable) must be
taken into consideration.
The maximum acceptable response times of the safety
functions are defined in the risk analysis of the machine.
The safety functions, configuration of the safety fieldbox
and correct installation must be checked by a responsible
safety specialist/safety representative.