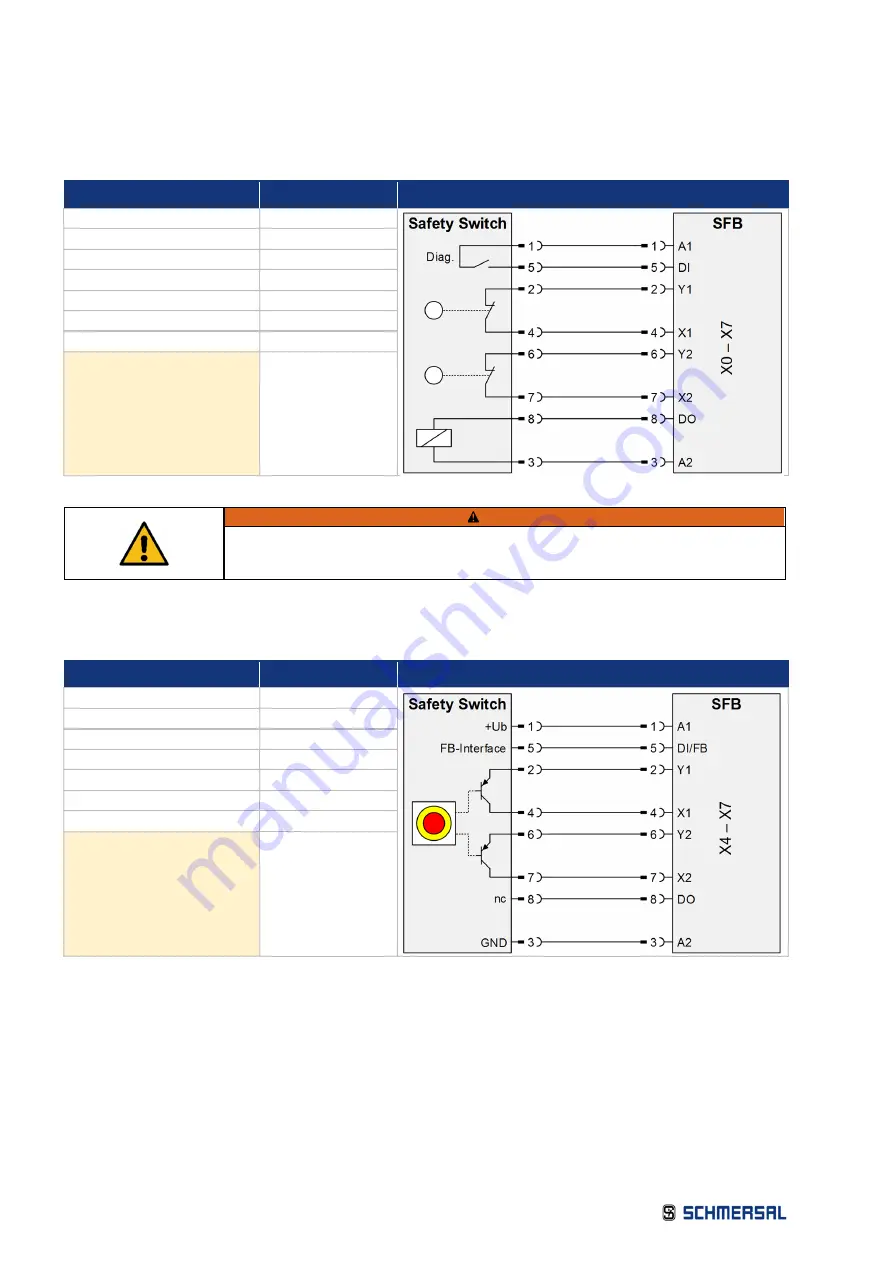
22
2 Product description
2.3.5
Electromechanical safety interlock, interlock function via 1 wire
Solenoid interlock with dry contacts equivalent, monitoring 1oo2
Parameters
Value
Connection example
Safety inputs
2 channels
Cross-fault detection
ON
Safety outputs
1 wire (PL d)
Monitoring time
10 s
Stable time
0.7 s
Safety classification
Inputs X1 & X2
−
up to Cat 4 / PL e / SIL 3
Output DO:
−
up to Cat 3 / PL d / SIL 2
SCHMERSAL devices: AZM 161-FB, AZM 170-FB, …
WARNING
For safety switchgear with dry contacts,
cross-fault detection must be activated !
Set Stable time 0.7 s and Monitoring time 10 s.
2.3.6
Electronic E-STOP and control panels with FB-Interface, 8-pole M12 connector
E-STOP pushbuttons with electronic OSSD and FB-Interface, monitoring 1oo2
Parameters
Value
Connection example
Safety inputs
2 channels
Cross-fault detection
OFF
Safety outputs
1 wire (PL d)
Monitoring time
2 s
Stable time
0.1 s
Safety classification
Inputs X1 & X2
−
up to Cat 4 / PL e / SIL 3
Output DO:
−
SCHMERSAL devices: BDF 200-FB, …