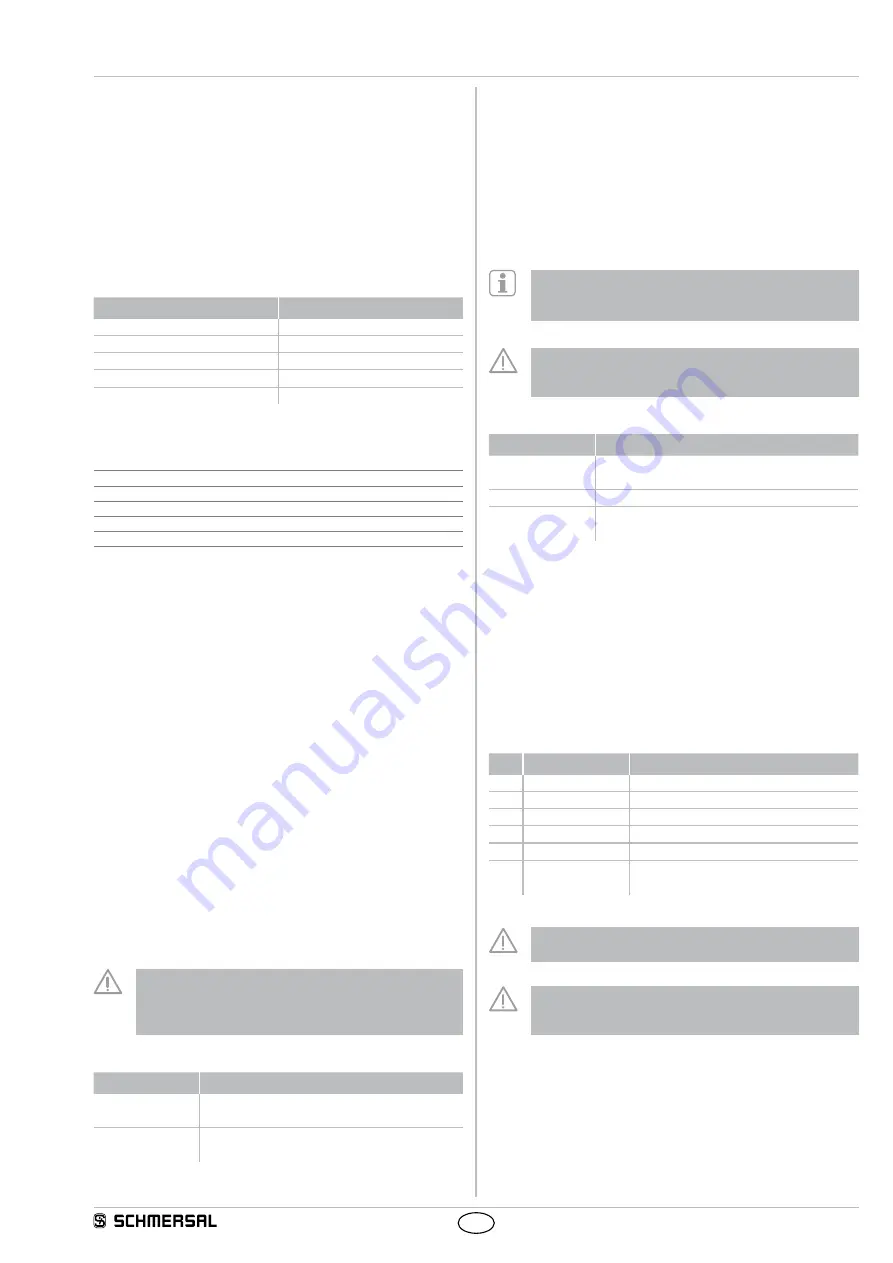
3
SLB240
Operating instructions
Safety light barriers
EN
1)
Detection capability is reduced with moving test body Further
information available from technical sales department
2)
To IEC 61131-2
3)
In case of failure, OSSD leakage current
The downstream control element must recognise this state as LOW
A safety PLC must detect this state
4)
The load inductivity generates an induced voltage during the switch-off,
which compromises the downstream components (spark quenching
element)
2.6 Response time (reaction time)
The response time depends on the number of light beams and the
beam coding A
Beam coding
Response time [ms]
1
10
2
14
3
18
4
22
5
7
2.7 Safety classification
Standards:
EN ISO 13849-1, EN 62061
PL:
up to c
Control category:
up to 2
PFH:
15 x 10
-8
1/h
SIL:
up to 1
Service life:
20 years
2.8 Modes of operation / functions
All of the described functions can be executed without safety monitoring
modules A command unit is needed for diagnosis and function
selection (button, adapter cable, see section on parameterisation)
The system has the following operating modes:
• Protection mode with automatic start after release of the protection
field (factory setting)
• Protection mode with restart interlock
The system has the following functions:
• Parameter setting with selection of beam coding and type of protection
mode
• Alignment aid, diagnosis
Factory setting
When delivered (factory setting) automatic mode is active
2.8.1 Protection mode with automatic (automatic)
In automatic mode the safety switching outputs
(OSSD) are switched to the ON state if the protection zone is
uninterrupted This is done without any authorization from a command
device
This operating mode initiates an automatic restart of the machine if the
protection zone is not interrupted
This operating mode may only be chosen in conjunction
with the restart interlock (manual reset) of the machine
This operating mode must not be chosen, when persons
can step behind the protection field
Display
Diagnostic lamp Status
Red
OFF state (protection zone interrupted,
OSSD signal low)
Green
ON state (protection zone uninterrupted,
OSSD signal high)
2.8.2 Protection mode with restart interlock
In the operating mode restart interlock, the safety switching outputs
(OSSD) remain in the OFF condition after the power supply is applied
or after the protection zone has been interrupted
The AOPD switches the OSSDs to the ON state once the restart input
signal impulse is applied with a duration of 100 ms < T < 1500 ms using
a command device (push button)
The receiver indicates the readiness for authorized operation with a
yellow signal on the end cap If the protection zone is interrupted, the
signal will indicate red
The AOPD changes to alignment aid mode if the enabling
button is pressed for at least 2 seconds when the operating
voltage is applied, see chapter Alignment aid
The command device (enabling button) must be installed
outside of the hazardous area The hazardous zone must
be easily visible to the user
Display
Diagnostic lamp Status
Red
OFF state (protection zone interrupted,
OSSD signal low)
Green
ON state (OSSD signal high)
Yellow
Restart interlock is active,
SLB waiting for enabling signal
2.8.3 Test input
The AOPD has a machine test function The test input is provided for
periodic test by a safety related control system Connecting the input to
0 V switches off the safety device and receiver outputs are switched to
the OSSD OFF-state For machine test duration longer than 150 ms a
restart interlock function needs to be provided
2.8.4 Parameter setting
In parameterisation mode, individual adaptation of the operating
parameters for transmitter and receiver can be carried out
Possible options are:
No. Option
Description
P1
active / not active Beam coding 1 (response time 10 ms)
P2
active / not active Beam coding 2 (response time 14 ms)
P3
active / not active Beam coding 3 (response time 18 ms)
P4
active / not active Beam coding 4 (response time 22 ms)
P5
active / not active Beam coding 5 (response time 7 ms)
P6
active / not active active = restart interlock
not active= automatic mode
The beam coding 5 may only be used if no other SLBs
are operated in parallel
The response time of the system changes with the
selected beam coding The safety distance must be
adapted accordingly See section on reaction time