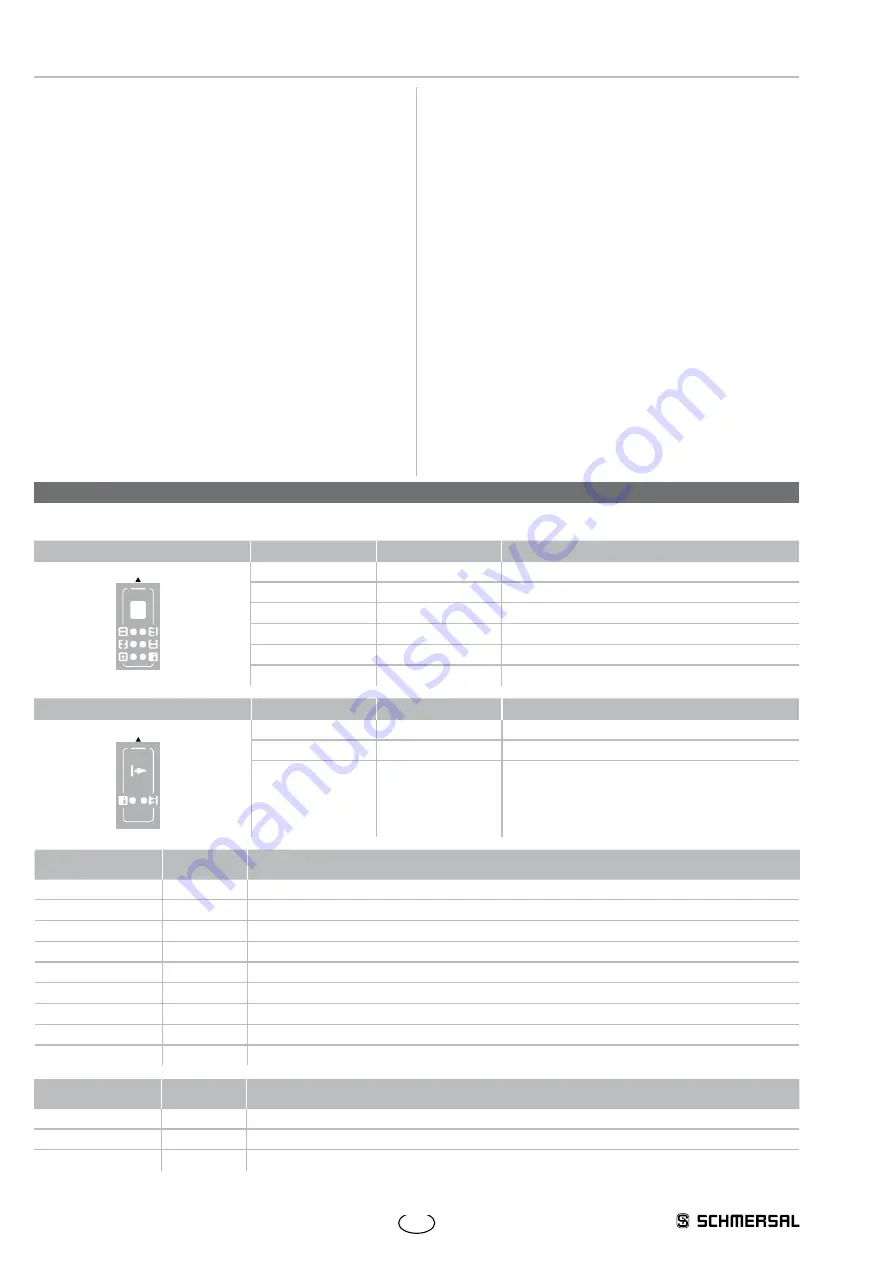
14
Operating instructions
Safety light grids
SLG440
EN
5.3 Regular check
A regular visual inspection and functional test, including the following
steps, is recommended:
1 The component does not have any visible damages
2 The optics cover is not scratched or soiled
3 Hazardous machinery parts can only be accessed by passing
through the protection field of the SLG
4 The staff remains within the detection area, when works are con-
ducted on hazardous machinery parts
5 The safety distance of the application exceeds the mathematically
calculated one
Operate the machine and check whether the hazardous movement
stops under the hereafter-mentioned circumstances.
1 Hazardous machine parts do not move when the protection field is
interrupted
2 The hazardous machine movement is immediately stopped, when
the protection field is interrupted with the test rod immediately before
the transmitter, immediately before the receiver and in the middle
between the transmitter and the receiver
3 No hazardous machine movement when the test rod is within the
protection field
4 The hazardous machine movement comes to standstill, when the
voltage supply of the SLG is switched off
5.4 Half-yearly inspection
The following items must be checked every six months or when a ma-
chine setting is changed
1 Machine stops or does not inhibit any safety function
2 No machine modification or connection change, which affects the
safety system, has taken place
3 The outputs of the SLG are correctly connected to the machine
4 The total response time of the machine does not exceed the re-
sponse time calculated during the first putting into operation
5 The cables, the connectors, the caps and the mounting angles are in
perfect condition
5.5 Cleaning
If the optics cover of the sensors is extremely soiled, the OSSD outputs
can be disabled Clean with a clean, soft cloth with low pressure
The use of agressive, abrasive or scratching cleaning agents, which
could attack the surface, is prohibited
6. Diagnostic
6.1 Status information LED
Receiver
Function
LED colour
Description
OSSD ON
OSSD OFF
Restart
Signal reception
Blanking
Information
Protection field
OSSD ON
green
Safety outputs Signal condition ON
OSSD OFF
red
Safety outputs Signal condition OFF
Restart
yellow
Input for command device
Signal reception
orange
Safety-monitoring module of Signal reception
Blanking
blue
Protection field(s) inactive (blanking)
Information
yellow-green
Beam coding A
Transmitter
Function
LED colour
Description
Information
Transmitting
Protection field
Information
green
Function display, Beam coding A
Transmitting
orange
Transmitter active
Receiver
LED
Status LED
Description
OSSD ON
On
Protection field clear
OSSD OFF
On
Protection field interrupted, system or configuration error
On
Error output refer to Fault diagnostic table
Restart
On
Restart interlock (manual reset) active, signal expected at input restart interlock
Signal reception
ON/flashing
Signal reception too low, check alignment and installation height between transmitter and receiver
Cleaning the black profile cover
OFF
Alignment between transmitter and receiver OK, when the OSSD are enabled
Blanking
2 flash
Floating blanking, max 1 beam
Information
flashing
Beam coding A is active
Transmitter
LED
Status LED
Description
Transmitting
On
Standard operation, transmitter active
flashing
Configuration error
Information
flashing
Beam coding A is active