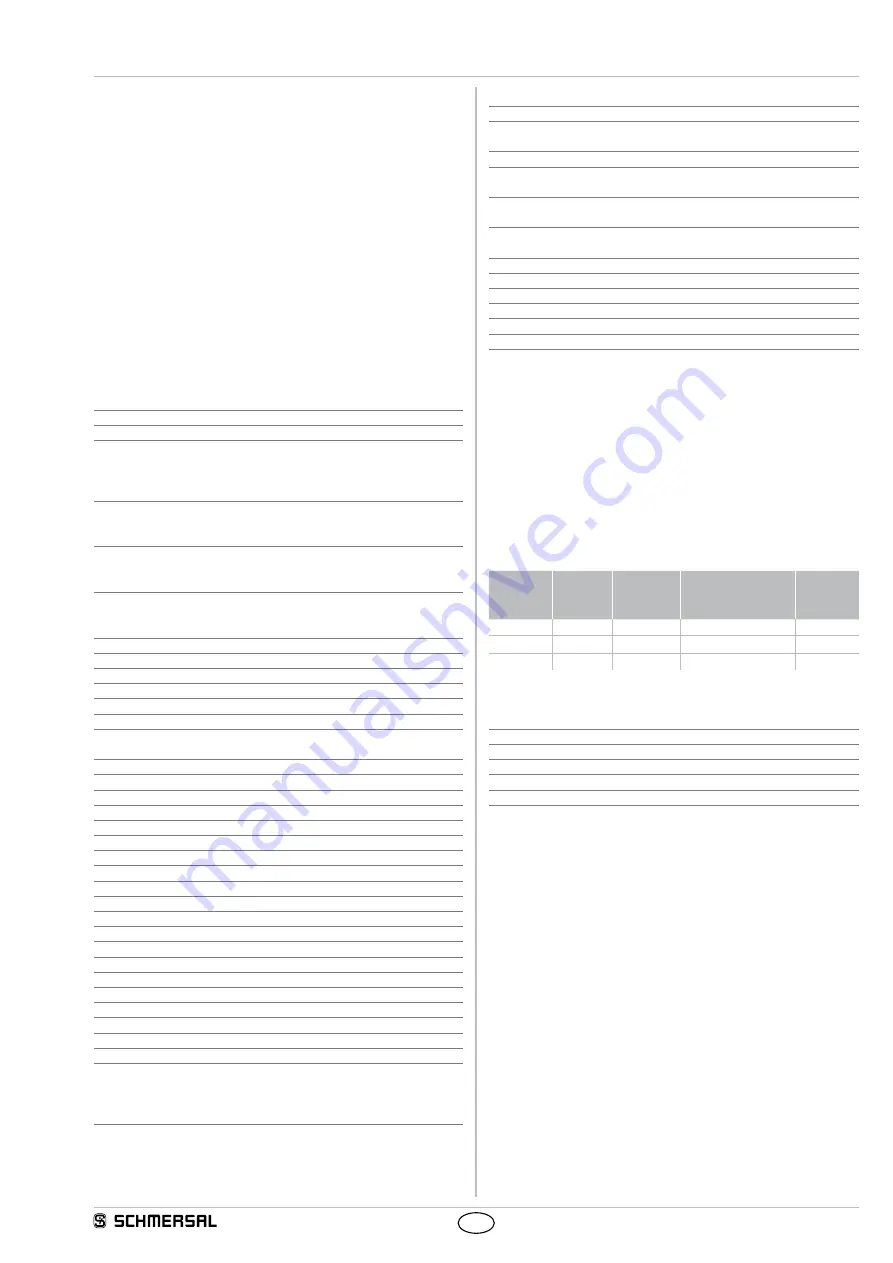
3
SLG440
Operating instructions
Safety light grids
EN
MSD4 Vibration damper
Kit consists of: 8 vibration dampers 15 x 20 mm, 8 M5 cylinder head
screws with hexagon socket, 8 spring washers Mounting using MS-1100
The MSD4 vibration damper kit is recommend to be used for damping
vibrations and oscillations on the SLG440 For applications with higher
mechanical stresses, eg presses, punching machines, we recommend
the MSD4 kit In this way, the availability of the SLG440 is increased
Spacer MSD5
The kit consists of 2 spacers The spacers must be used in case of
vibrations
Integrated status indication
The SLG440 series is also available with integrated status indication
(red/yellow/green) installed onto the receiver (See ordering code)
2.5 Technical data
Standards:
EN 61496-1; EN 61496-2;
EN ISO 13849; EN 62061
Material of the enclosure:
Aluminium
Protection field heights:
500 mm, 800 mm, 900 mm
Detection ability for test bodies:
2 beams with resolution 500 mm *3
3 beams with resolution 400 mm *3
4 beams with resolution 300 mm *3
Range of the protection field:
- Standard
03 … 12 m
- Height range (H)
30 … 20 m
Response time:
- Beam coding (normal)
2 - 4 beams = 10 ms
- Beam coding A
2 - 4 beams = 15 ms
Rated operating voltage:
24 VDC ±10% (PELV) supply unit
I
max
20 A, to EN 60204
(power drop ≤ 20 ms)
Rated operating current:
250 mA max + 2 x 025 A each OSSD
Wavelength of the infrared radiation:
880 nm
Transmitter, infrared emitted radiation
- to DIN EN 12198-1:
Category 0
- to DIN EN 62471:
free group
Safety outputs
OSSD1, OSSD2:
2 x short-circuit proof PNP
semi-conductor outputs
Test impulse cycle OSSD:
750 ms
Test impulse length:
100 µs
Switching voltage HIGH¹:
15 … 264 V
Switching voltage LOW¹:
0 … 2 V
Switching current each OSSD:
0 … 250 mA
Leakage current²:
1 mA
Load capacity:
0 … 22 µF
Load inductance
4
:
0 … 2 H
Admissible conduction resistance between OSSD and load:
2.5 Ω
Admissible conduction resistance of the supply cable:
1.5 Ω
Contactor control (EDM)
Input voltage HIGH (inactive):
11 … 30 V
Input voltage LOW (active):
0 … 20 V
Input current HIGH:
3 … 10 mA
Input current LOW:
0 … 2 mA
Input release restart interlock/restart interlock 2
Input voltage HIGH (active):
11 … 30 V
Input voltage LOW (inactive):
0 … 20 V
Input current HIGH:
3 … 10 mA
Input current LOW:
0 … 3 mA
Functions:
automatic mode, restart interlock,
double reset, contactor control,
beam blanking fixed and floating,
beam coding A
Signal times
Contactor control:
max 500 ms
Restart interlock (manual reset):
50 ms … 15 s, signal
transmission in case of trailing edge
LED indications transmitter:
transmitting, status
LED indications receiver:
OSSD ON, OSSD OFF, restart, signal
reception, blanking, information
Connection:
M12 connector plug with metal thread,
receiver 8-pole, transmitter 4-pole
Ambient temperature:
−25° C … + 50° C;
at −25° C: Reduction of range by −10%
Storage temperature:
−25° C … + 70° C
Interface:
Diagnostics and function setting
Protection class:
IP67 (IEC 60529)
Resistance to vibration:
10 … 55 Hz to IEC 60068-2-6
Resistance to shock:
10 g, 16 ms, to IEC 60028-2-29
Year of construction:
as of 2014 version 20
¹) To IEC 61131-2
²) In case of failure, the leakage current at the most flows to the OSSD
cable The downstream control element must recognise this state as
LOW A safety PLC must detect this state
³) resolution = beam di beam diameter 10 mm
4)
The load induction generates an induced voltage during the
switch-off, which compromises the downstream components
(spark quenching element)
2.6 Response time (reaction time)
The response time depends on the number of light beams and the
beam coding A
Beams
[Number]
Beam
distance
[mm]
Response
time
[ms]
Response time
with beam coding
A [ms]
Weight
[kg]
2
500
10
15
090
3
400
10
15
135
4
300
10
15
150
2.7 Safety classification
Standards:
EN ISO 13849-1, EN 62061
PL:
up to e
Control category:
up to 4
PFH value:
514 x 10
-9
/ h
SIL:
up to 3
Service life:
20 years
2.8 Functions
The system consists of a receiver and a transmitter For the described
functions, no further switching elements are required The diagnostic
and function selection takes place with a command device (key re-
lease), refer to the chapter on parameterisation
The system has the following features:
• Protective mode automatic
(automatic start after release of the protection zone)
• Restart Interlock (manual reset)
• Double acknowledgement/reset
• Contactor control (EDM)
• Beam coding A
• Blanking of movable objects