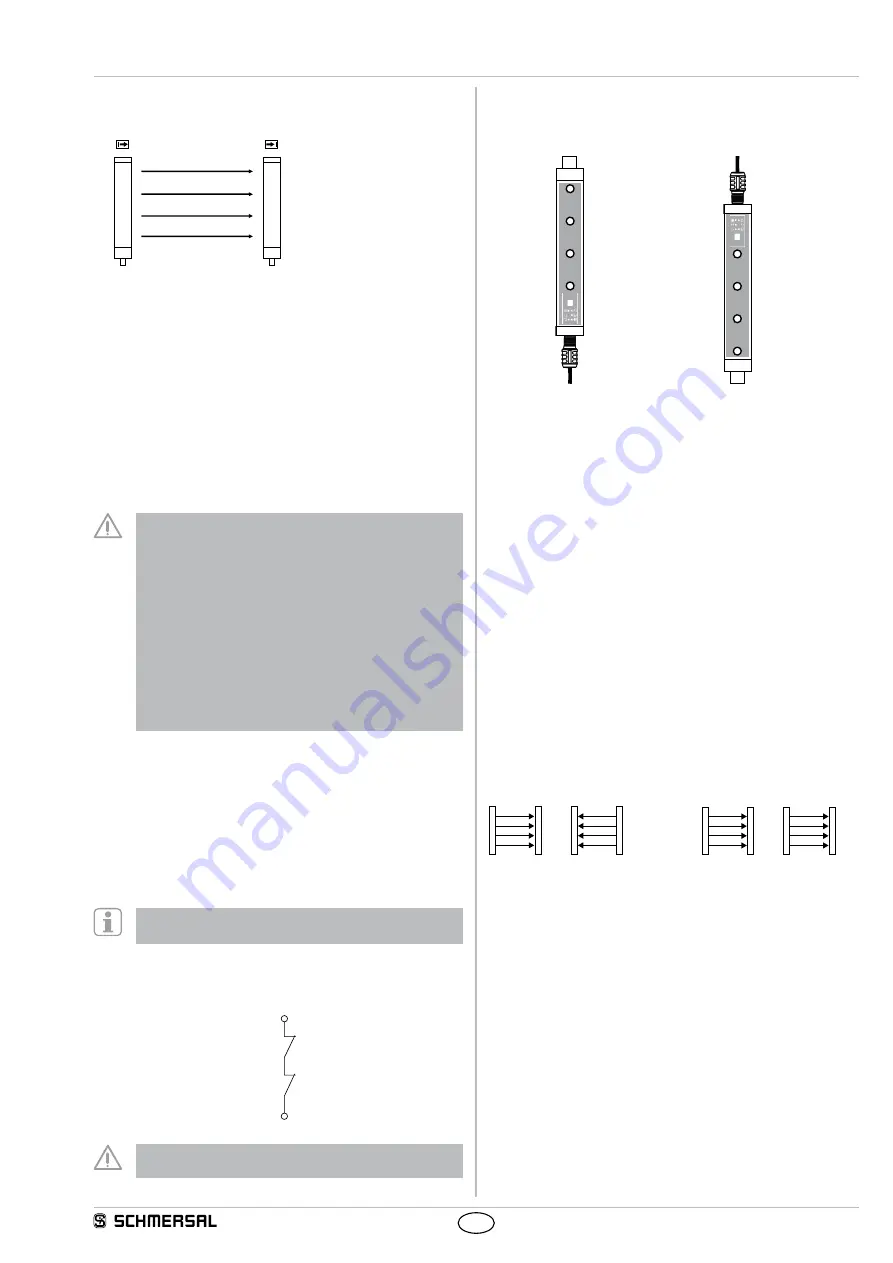
5
SLG440
Operating instructions
Safety light grids
EN
2.8.4 Blanking of moving objects
The SLG440 can blank movable objects in the protection field
4
3
2
1
R1
E1
The moving blanking range is authorised for individual beams in case of
obstacles, taking the protective function into account
The function enables an arbitrary floating blanking of partial areas in the
protection field The first beam, which is located immediately behind
the diagnostic window, cannot be blanked
This function allows for an interruption of maximum 1 light beam
without the outputs being disabled in case of material movement in the
protection field, eg ejection of material or process-controlled material
movement
The operating mode is only available, when the parameter setting P 3 is
activated See chapter Parameter setting
• The variable blanking of one beam is not authorised with
the 2-beam SLG440!
• The blanking of one beam at the most in the SLG440
3-beam version or the SLG440 4-beam version is
authorised, provided that the protective function is taken
into account
• The restart interlock (manual reset) function of the safety
light grid or the machine must be activated
• The protection field must be checked with a test rod by a
qualified person after the configuraiton
• The standard IEC/TS 62046 includes information, which
describes possibly required additional measures to prevent
a person from reaching a hazard through the beam blanking
of a protection field
2.8.5 Contactor control (EDM)
The contactor control monitors the controlled switching elements
(auxiliary contacts of the contactors) of both outputs This monitoring
is realised after each interruption of the protection field and prior to the
restart (enabling) of the outputs In this way, malfunctions of the contac-
tors are detected, eg contact welding or contact spring breakage If
the light curtain detects a malfunction of the switching elements, the
outputs are locked
After elimination of the error, a power reset is required
The contactor control is not activated upon delivery The
function is activated in parameter setting mode (P 4)
Connection EDM
Wiring of the receiver
- Kn1, Kn2 = auxiliary contact
of the last switching relay
+24VDC
Kn1
Pin 8
Kn2
The auxiliary contacts must only be connected, when the
function is activated!
2.8.6 Rotating the display through 180 degrees
The orientation of the 7 segment display can be rotated through 180
degrees via the software option This ensures that the display remains
readable in rotated mounting positions of the AOPD
Parameter
P 7 –
Display normal orientation
Parameter
P 7 A
Display rotated
2.9 Self-test
The system performs a complete self-test and safety test within 2 sec-
onds after the operating voltage has been switched on If the protection
field is free, the system switches to the ON condition (automatic mode)
In case of an error, the outputs at the receiver do not switch to the ON
state An error message is emitted in the form of an error code For
more information, refer to chapter Fault diagnosis
During operation, the system executes a cyclic self-test Safety-rele-
vant faults are detected within the reaction time and cause the outputs
to be switched off and an error code to be emitted
2.10 Beam coding A
The preset beam coding of the safety light grid must be adjusted, when
systems operating in each other's vicinity and a set-up as shown in the
image below (no interference) is impossible When supplied, the beam
coding A is
not active
A receiver with activated beam coding A can dis-
tinguish the beams of the transmitter with the same beam coding, which
are destined to this particular receiver, from foreign beams
If adjacent systems are operated without beam coding A, the user is at
risk
E
E
R
R
E
R
R
E
No interference
Interference:
beam coding A required!
• The beam coding A avoids mutual interference of adjacent systems.
• The beam coding A is permanently shown by the transmitter and the
receiver by means of flashing LED's (refer to LED status information)
• The beam coding A must be set for
each sensor
(receiver and
transmitter) individually
• The function at the receiver is activated in parameter setting
mode (P 6)