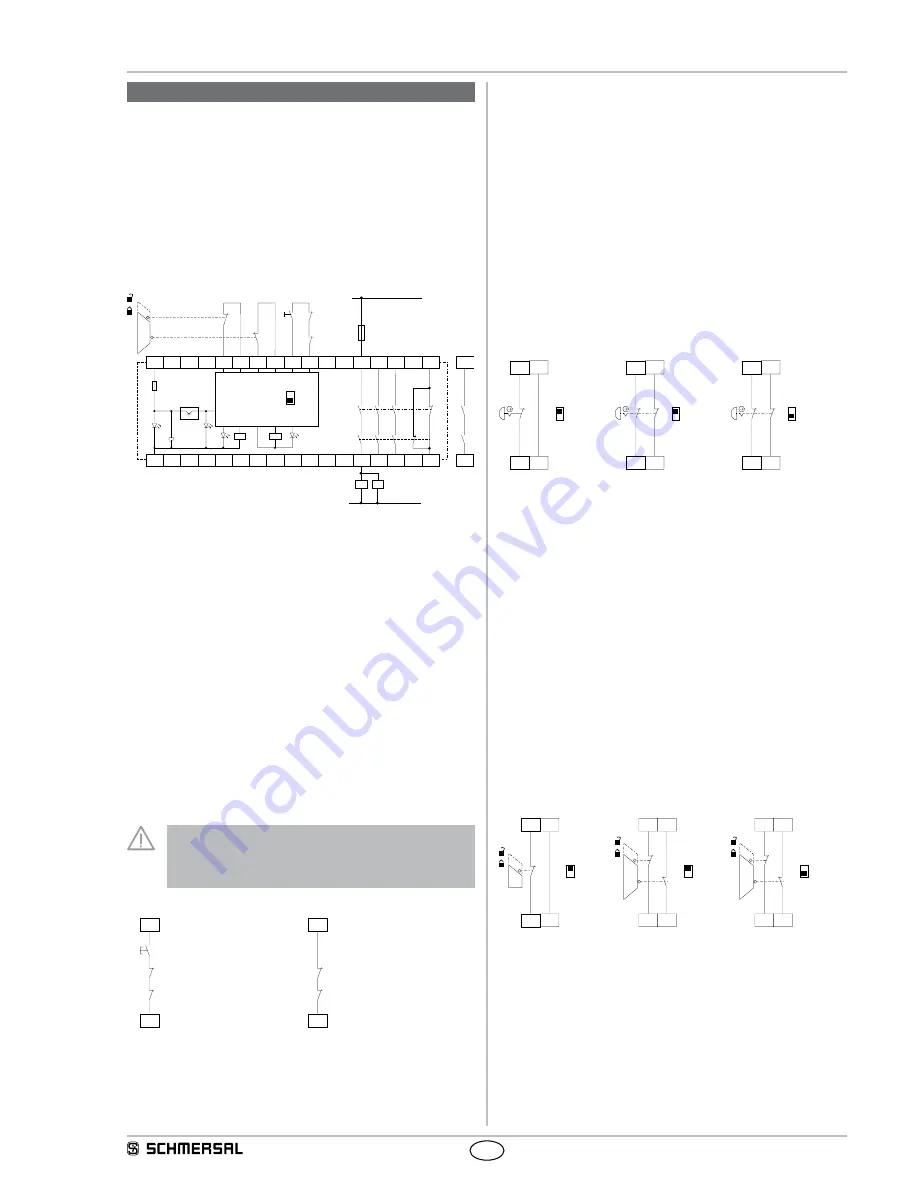
5
SRB 301MC
SRB 301MC-ST
Operating instructions
Safety-monitoring module
EN
8. Appendix
8.1 Wiring examples
Dual-channel control, shown for a guard door monitor with
two position switches where one has a positive break contact;
with external reset button
J
(Fig. 4)
• Relay outputs: Suitable for 2-channel control, for increase in capacity
or number of contacts by means of contactors or relays with
positive-guided contacts.
• The control system recognises wire-breakage, earth faults and
cross-wire shorts in the monitoring circuit.
•
S
= Feedback circuit
K
A
K
B
K1
K2
F1
UB
Ui
A1
S12 S11 S21
K
A
K
B
L1
N
K
A
K
B
K1
K2
13
23
S22 X1
A2
14 24
33
34
41
X2
a)
nQS
QS
S
J
42
Fig. 4
a) Logic
8.2 Start configuration
External reset button (Fig. 5)
• The external reset button is integrated in the feedback circuit in series.
• The manual start or the activation of the module occurs when the
button is pressed (not when it is released!).
Automatic start (see Fig. 6)
• The automatic start is programmed by connecting the feedback circuit
to the terminals X1-X2. If the feedback circuit is not required, establish
a bridge.
•
Caution: Not admitted without additional measure due to the
risk of gaining access by stepping behind
!
• When the SRB 301MC safety-monitoring module is used with
the operating mode "Automatic start", an automatic restart after a
shutdown in case of emergency must be prevented by the upstream
control to EN 60204-1 paragraph 9.2.5.4.2.
Due to the operating principle of the electronic fuse,
the customer must check that no hazard is caused by
an unexpected restart in circuits without reset button
(automatic reset).
X2
X1
K
A
J
K
B
X2
X1
K
A
K
B
Fig. 5
Fig. 6
8.3 Sensor configuration
Single-channel emergency stop circuit with command devices
to ISO 13850 and IEC 60947-5-5 (Fig. 7)
• Wire breakage and earth leakage in the control circuits are detected.
• Category 1 – PL c to ISO 13849-1-1 possible.
Dual-channel emergency stop circuit with command devices
to ISO 13850 and IEC 60947-5-5 (Fig. 8)
• Wire breakage and earth leakage in the control circuits are detected.
• Cross-wire shorts between the control circuits are not detected.
• Control category 4 – PL e to ISO 13849-1-1 possible.
Dual-channel emergency stop circuit with command devices
to ISO 13850 and IEC 60947-5-5 (Fig. 9)
• Wire breakage and earth leakage in the control circuits are detected.
• Cross-wire shorts between the control circuits are detected.
• Category 4 – PL e to ISO 13849-1-1 possible.
S12
S11
S22
S12
nQS
QS
S12
S11
S22
S21
nQS
QS
S12
S11
S22
S21
nQS
QS
Fig. 7
Fig. 8
Fig. 9
Single-channel guard door monitoring circuit with interlocking
devices to ISO 14119 (Fig. 10)
• At least one contact with positive break required.
• Wire breakage and earth leakage in the control circuits are detected.
• Category 1 – PL c to ISO 13849-1-1 possible.
Dual-channel guard door monitoring circuit with interlocking
device to ISO 14119 (see Fig. 11)
• At least one contact with positive break required.
• Wire breakage and earth leakage in the control circuits are detected.
• Cross-wire shorts between the monitoring circuits are not detected.
• Control category 4 – PL e to ISO 13849-1-1 possible.
Dual-channel guard door monitoring circuit with interlocking
device to ISO 14119 (see Fig. 12)
• At least one contact with positive break required.
• Wire breakage and earth leakage in the control circuits are detected.
• Cross-wire shorts between the guard monitoring circuits are detected.
• Category 4 – PL e to ISO 13849-1-1 possible.
S12
S11
S22
S12
nQS
QS
S12
S11
S22
S21
nQS
QS
S12
S11
S22
S21
nQS
QS
Fig. 10
Fig. 11
Fig. 12