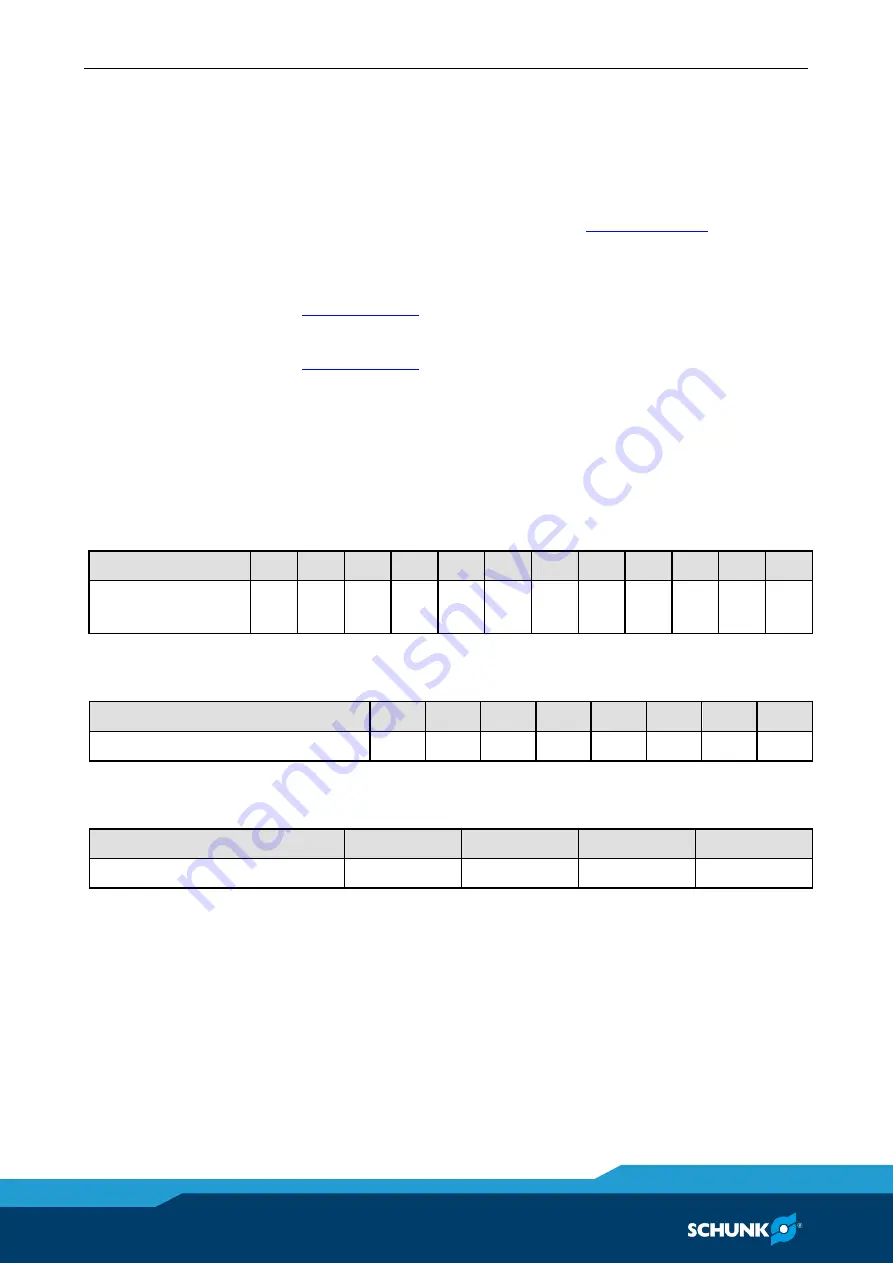
Scope of delivery
16
02.00|ROTA NC plus 2 / ROTA NCF plus 2 |en
Warranty
If the product is used as intended, the warranty is valid for 24
months from the ex-works delivery date under the following
conditions:
•
Observe the applicable documents,
•
Observe the ambient conditions and operating conditions
•
Observe the maximum number of clamping cycles
•
Observe the specified maintenance and lubrication intervals,
Parts touching the workpiece and wear parts are not included in
the warranty.
Torques per screw
Tightening torques for mounting screws used to clamp the chuck
on lathes or other suitable technical equipment
(screw quality
10.9)
Screw size
M6 M8 M10 M12 M14 M16 M18 M20 M22 M24 M27 M30
Admissible torque
M
A
(Nm)
13
28
50
88
120 160 200 290 400 500 1050 1500
Tightening torques for mounting screws used to attach top jaws
onto the chuck
(screw quality 12.9)
Screw size
M6
M8
M10 M12 M14 M16 M20 M24
Max. admissible torque M
A
(Nm) 16
30
50
70
130
150
220
450
Tightening torques for the protection sleeve mounting screws
(screw quality 8.8)
Screw size
M3
M4
M5
M6
Tightening torques M
A
(Nm)
1.3
3.0
5.5
9.0
Scope of delivery
1
Power chuck
3
Mounting screws
6
T-nuts with screws or 3 combi T-nuts
1
Mounting wrench
(from size 260 and up)
1
Eye bolt
from size 260 and up
1
Operating manual
3
4
5