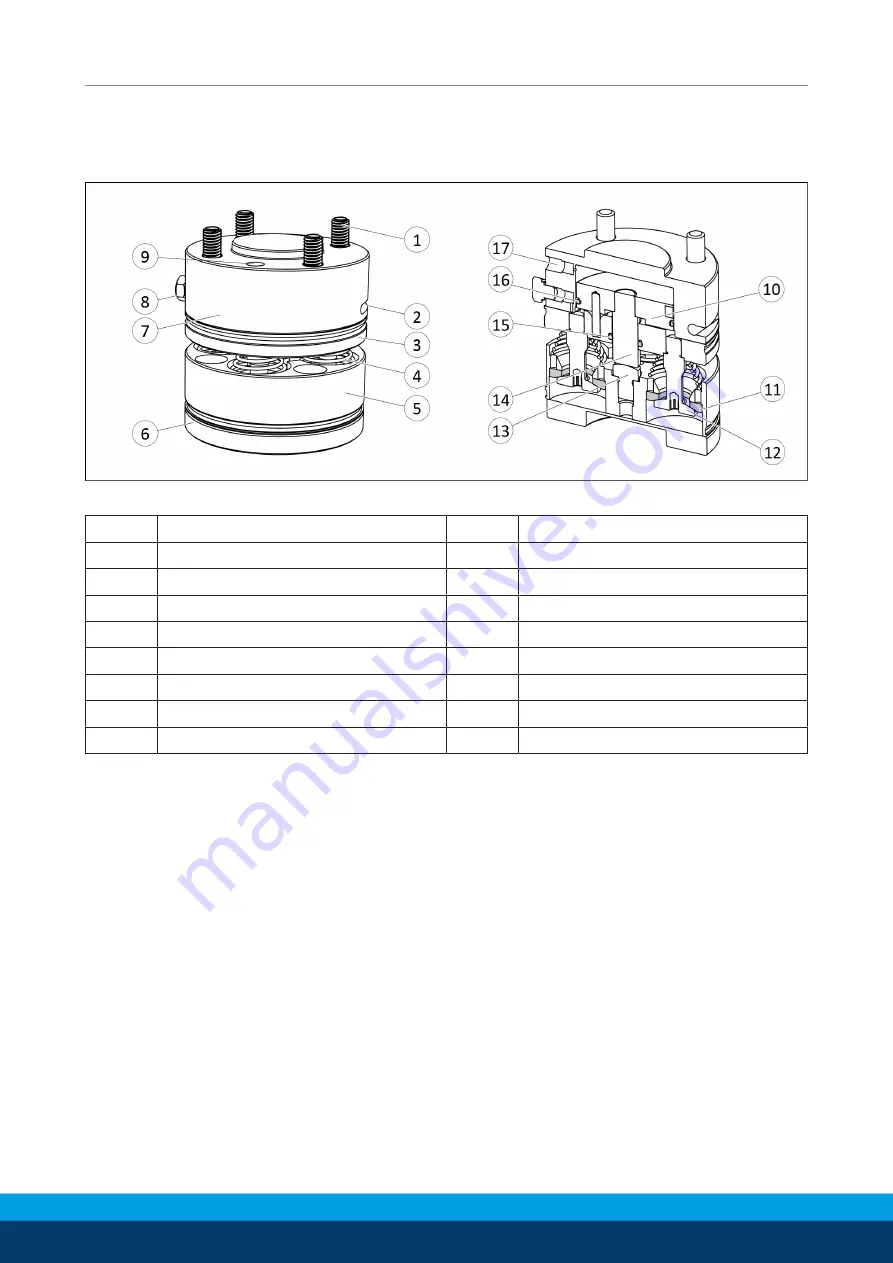
Design and description
16
01.00 | AGE-U | Assembly and Operating manual | en | 1393226
4 Design and description
4.1 Design
Design and Sectional view
1
Screw for mounting on robot
10
Piston
2
Groove for sensor
11
Washer, beveled
3
Piston cover
12
Overload pin
4
Compression spring
13
Workpiece stop
5
Housing, tool side
14
Piston rod
6
Tool plate
15
O-ring
7
Housing, robot side
16
O-ring
8
Air-relief valve
17
Compressed air connection
9
Bore hole for alignment pin