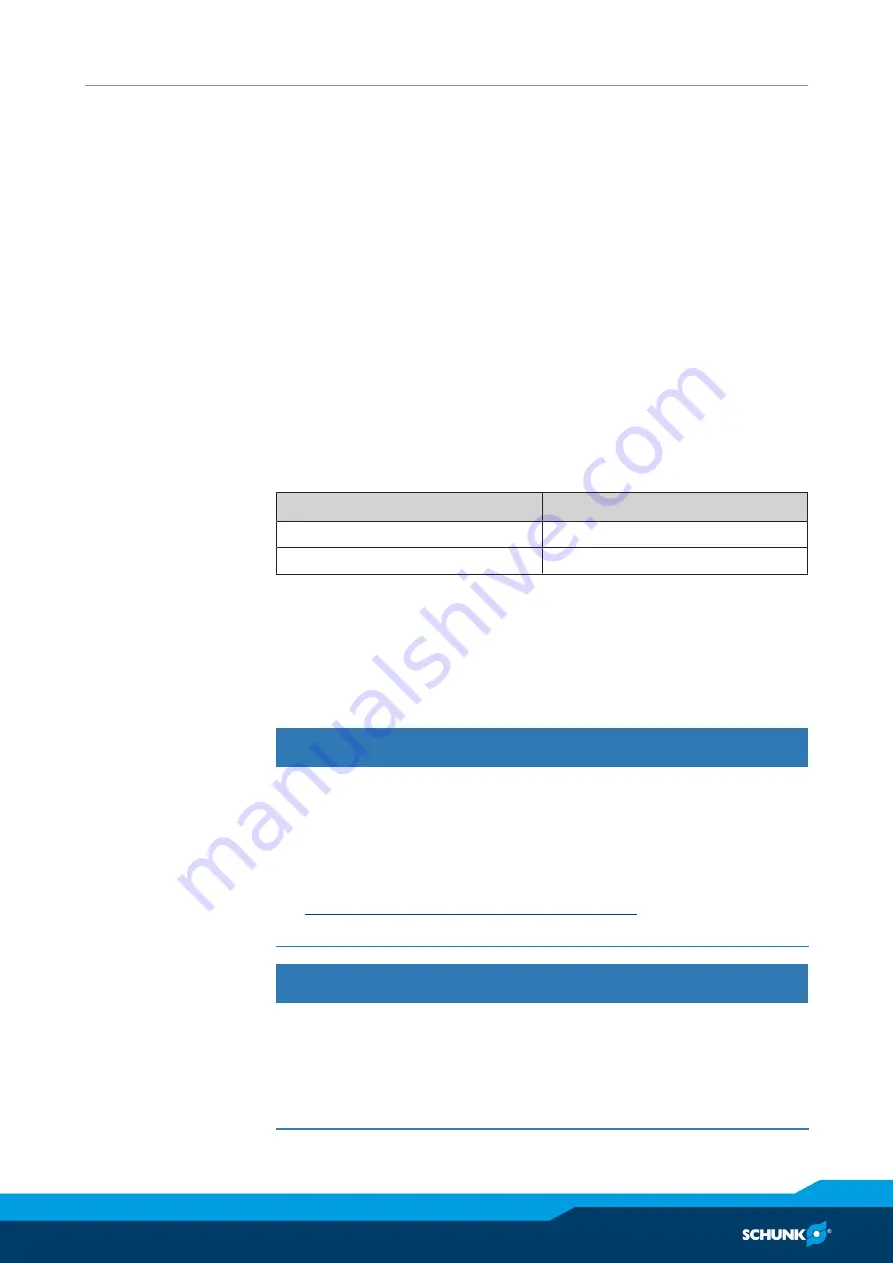
Assembly and Settings
03.00 | CLM | Assembly and operating manual | en | 389015
17
4 Assembly and Settings
Assembly measures
• When mounting the module and when mounting loads, do not
allow impermissible forces and moments to be exerted (
☞
catalog data)
• Select the suitable screw tightening torque when mounting the
module or loads on the module in accordance with the
generally accepted guidelines for screw connections.
• Secure all screw connections using a suitable chemical screw
lock.
4.1 Mechanical connection
Evenness of the
mounting surface
The values apply to the whole mounting surface to which the
product is mounted.
Requirements for evenness of the mounting surface (Dimensions in mm)
Edge length
Permissible unevenness
< 100
< 0.02
> 100
< 0.05
The linear module may be selectively attached to the body or the
carriage..
Similarly, the structure may be optionally attached to the end
carriage or the base body.
4.2 Pneumatic connection
CAUTION
Possible damage to the linear module!
If the unit moves too hard into the end position, the linear
module may be damaged.
•
A linear movement must always be free of impact and bounce.
•
For this purpose, carry out sufficient throttling and damping,
Adjustment of the shock absorber strocke
•
Observe the specifications in the catalog data sheet.
CAUTION
Risk of damage to the linear module when changing pressure
medium.
The unit must not under any circumstances be operated with
oiled air before operation with unoiled air (washing out of factory
lubrication).