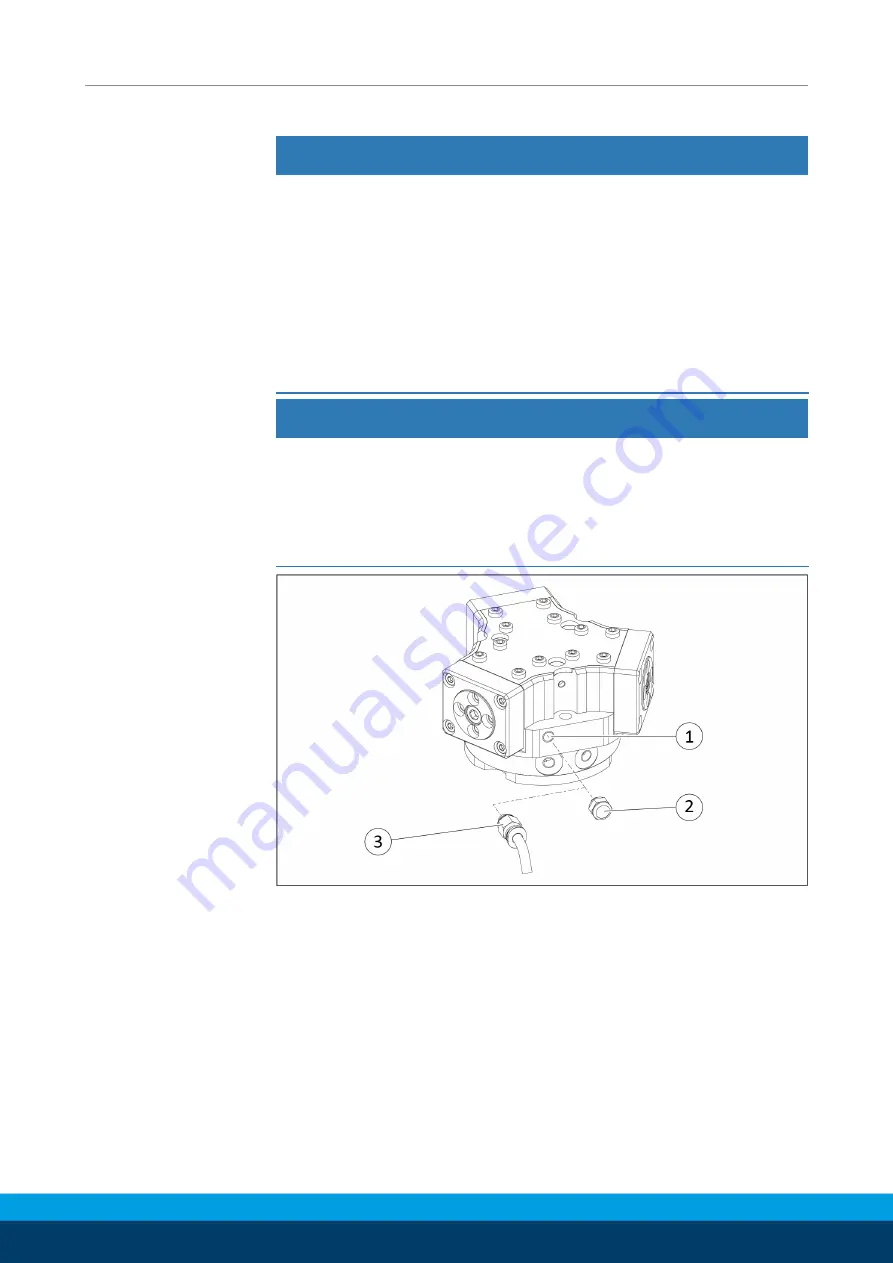
Assembly
26
25.00 | DPZ-plus | Assembly and Operating Manual | en | 389035
5.3 Installing the ventilation connection/air purge connection
CAUTION
Material damage due to incorrect connection!
If the product is only operated with the two main air connections,
neither correct functioning nor permanent tightness can be
guaranteed. This can result in damage to the product.
•
The product can only be operated if either a ventilation hose
(preferred) or the air purge has been connected at the air
purge connection.
•
When using the air purge connection, make sure the product
releases excess pressure while closing.
CAUTION
Material damage due to liquid ingress!
When used under water, liquid may enter the gripper during
temporary or constant immersion.
•
In such cases, always operate the product with air purge in
order to prevent ingress of liquid.