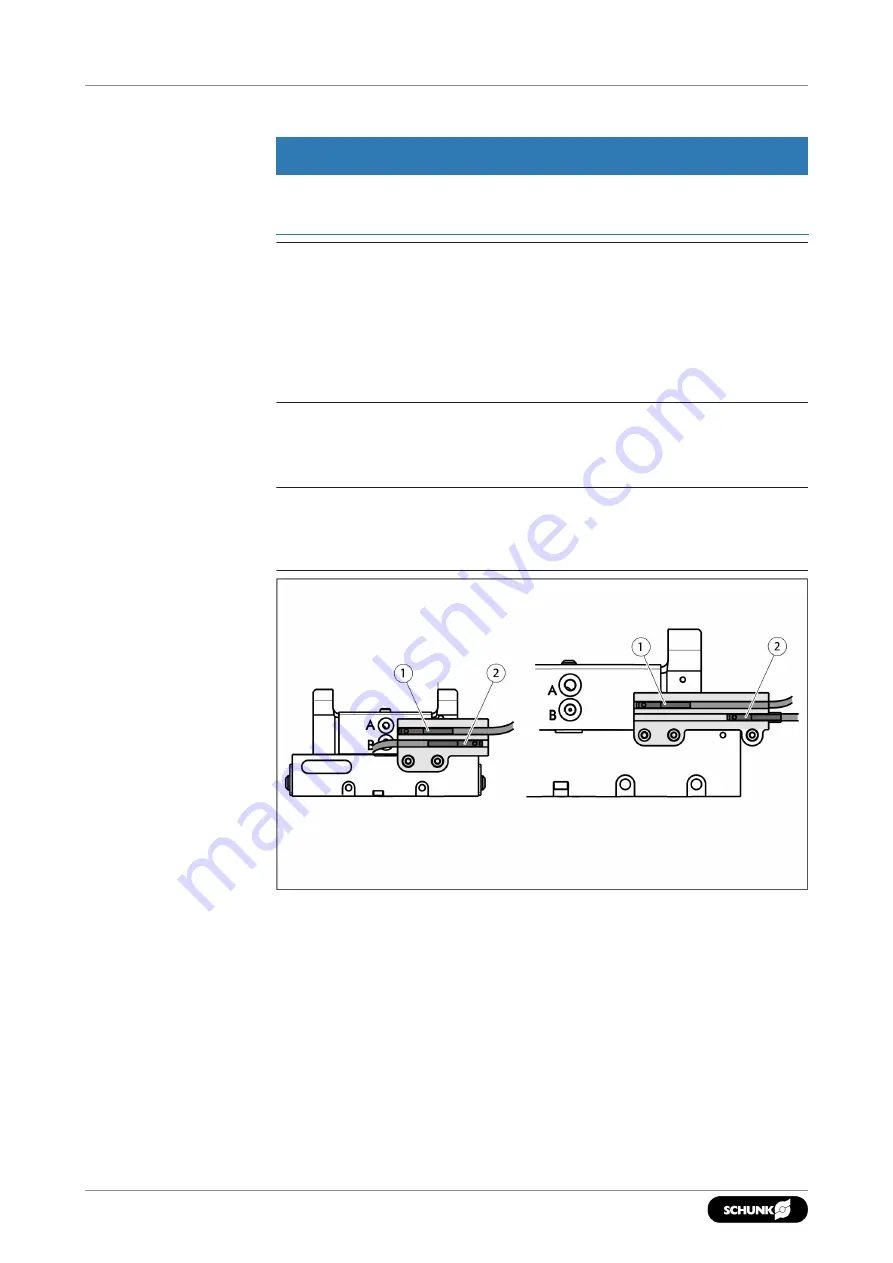
Assembly
30
17.00 | KGG | Assembly and Operating Manual | en | 389166
5.3.5 Installing the magnetic switch MMS 22 / RMS 22
CAUTION
Risk of damage to the sensor during assembly!
•
Observe the maximal tightening torque.
NOTE
Ferromagnetic material changes the switching positions of the
sensor. For example: Adapter plate made of ordinary steel.
At ferromagnetic adapter plates:
• First mount the product on the adapter plate.
• Then set the position of the magnetic switch.
The RMS sensors have a larger hysteresis than the MMS sensors.
This means that short gripper strokes may not be able to be
monitored with the RMS sensors.
Positioning the
magnetic switch
NOTE
The RMS magnetic switches have two switching points. Make sure
that the correct switching point is set.
Position of the magnetic switches
Summary of Contents for KGG 100
Page 1: ...Translation of the original manual Assembly and Operating Manual KGG 2 Finger Parallel Gripper...
Page 49: ......
Page 50: ......
Page 51: ......