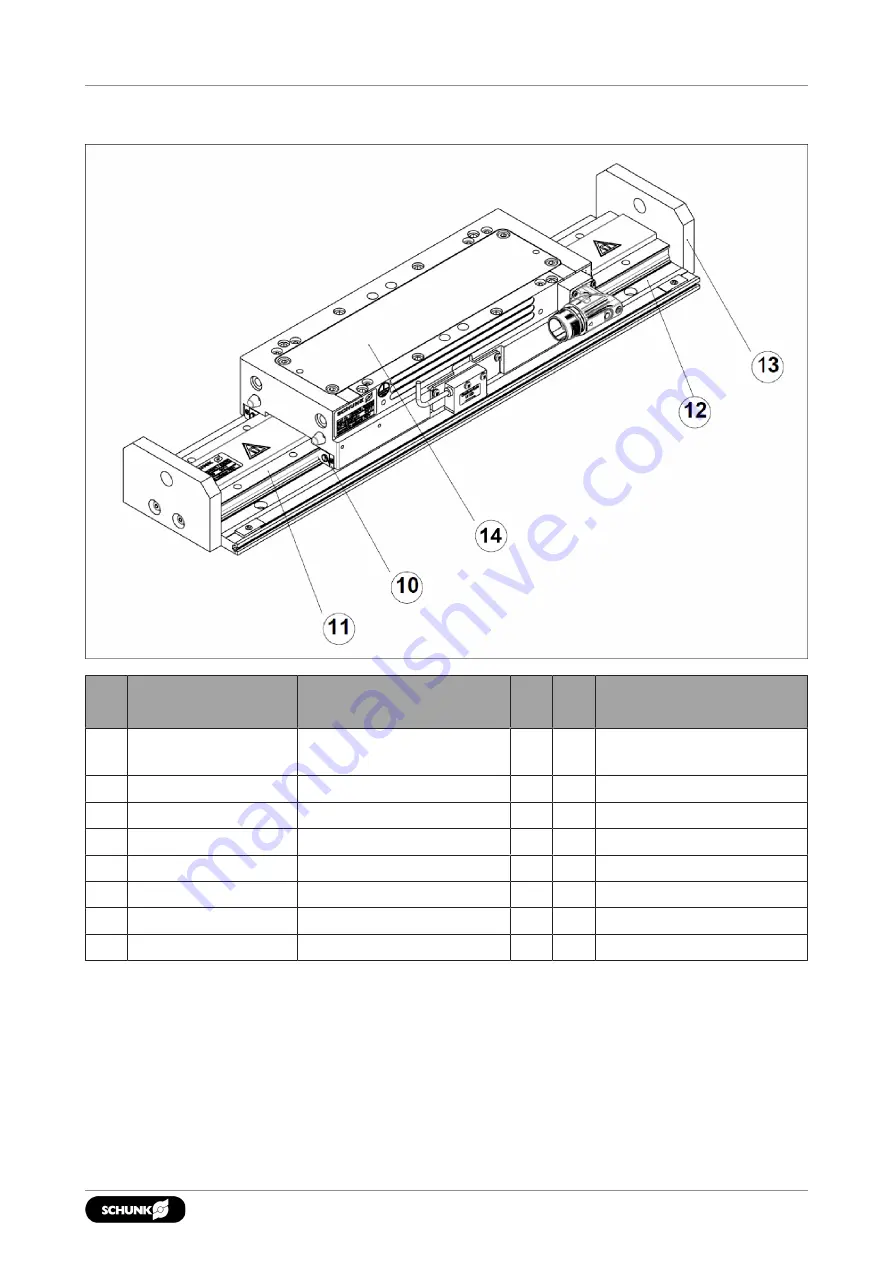
Spare parts
9.3 Axes
Pos. Type of axis
Designation
Num-
ber
Op-
tion
Order Number
10
all
Recirculating ball bearing
size 42
4
GAS361448
11
all
Guide rails
2
H
12
all
Profile guide
1
H
13 a all
End plate
2
GAS 319 743
14 a LDL-US-0100
Motor MGL-US-0100
1
GAS 368 645
14 b LDL-UL-0200
Motor MGL-UL-0200
1
GAS 368 659
14 c LDL-US-0100
Motor MGL-US-0100-RS
1
GAS 368 370
14 d LDL-UL-0200
Motor MGL-UL-0200-RS
1
GAS 368 662
H
stroke-dependant
111
06.00 | LDL | Assembly and Operation Manual | en | GAS341441