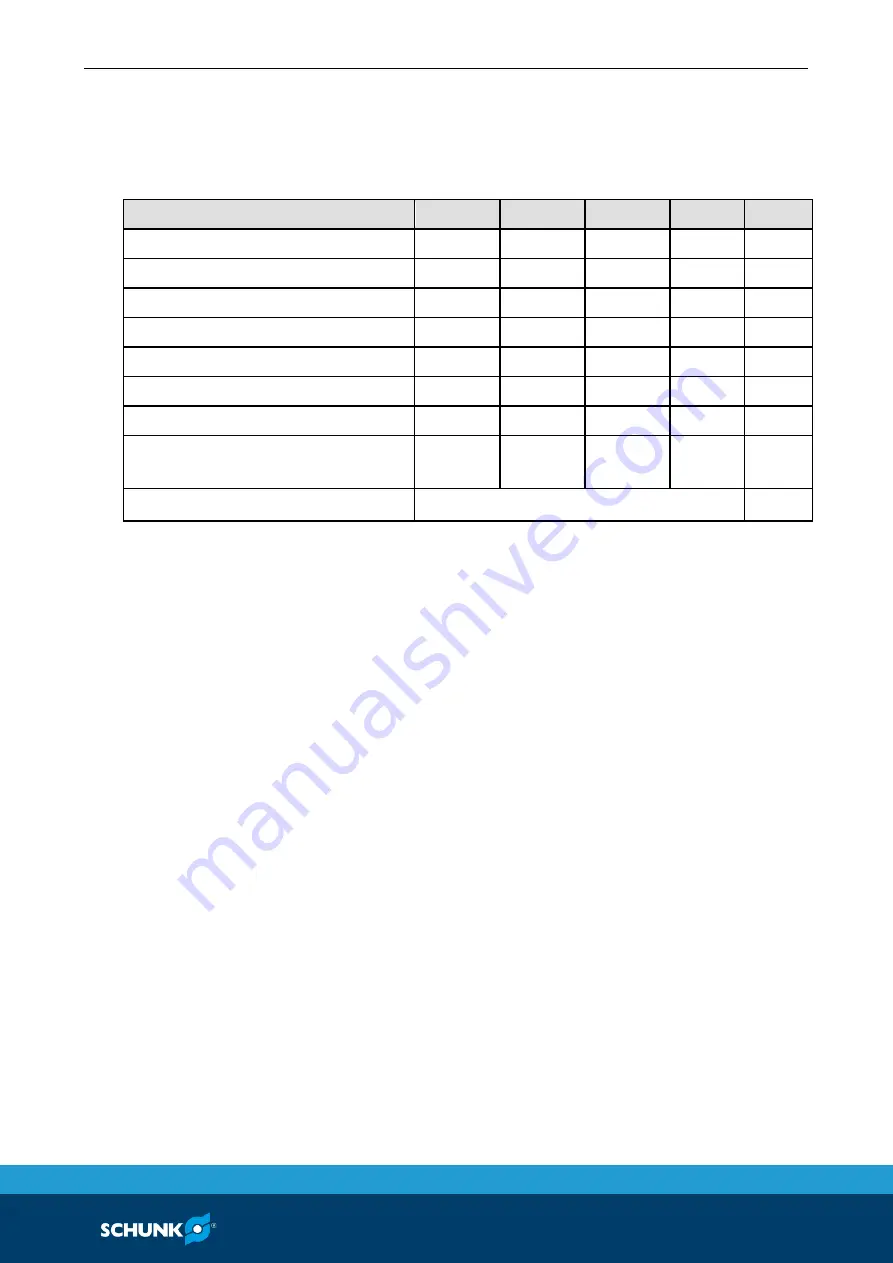
Torques per screw
02.00|ROTA NCA |en
19
Technical data
Chuck data
ROTA NCA
160
200
225
280
330
Max. actuating force [kN] *
20
32
45
63
72
Max. clamping force [kN]
45
72
100
140
160
Max. speed [rpm]
5500
5000
5000
4000
3500
Stroke per jaw [mm]
4
5.3
5.3
5.3
5.3
Piston stroke [mm]
15
20
20
20
20
Chuck through bore [mm]
32
52
66
86
104
Weight [kg]
11.5
19.6
29
42
62.8
Centrifugal torque of base jaw
[kgm]
M
cGB
0.039
0.089
0.153
0.348 0.478
Operating temperature
+ 15°C to + 60°C
* For I.D. clamping, the maximum actuating force must be reduced
by 30%.
The maximum RPM stated is only valid with the maximum
clamping force and when using the hard standard chuck jaws that
go with the chuck.
The maximum permissible RPM for the specific machining has to
be defined by the user on the basis of the required clamping
forces. This speed must not exceed the maximum speed of the
chuck.
Ensure minimal weight for all jaws.
For unhardened top jaws or chuck jaws in special design, the
permissible RPM according to VDI 3106 must be determined by
means of calculation for the respective machining job. In this,
however, the recommended maximum speed must not be
exceeded. The calculated values must be checked by dynamic
measurement. Function monitoring (piston movement and
actuating pressure) must be performed in accordance with the
guidelines of the Berufsgenossenschaft (employers' mutual
insurance association).
3
3.1