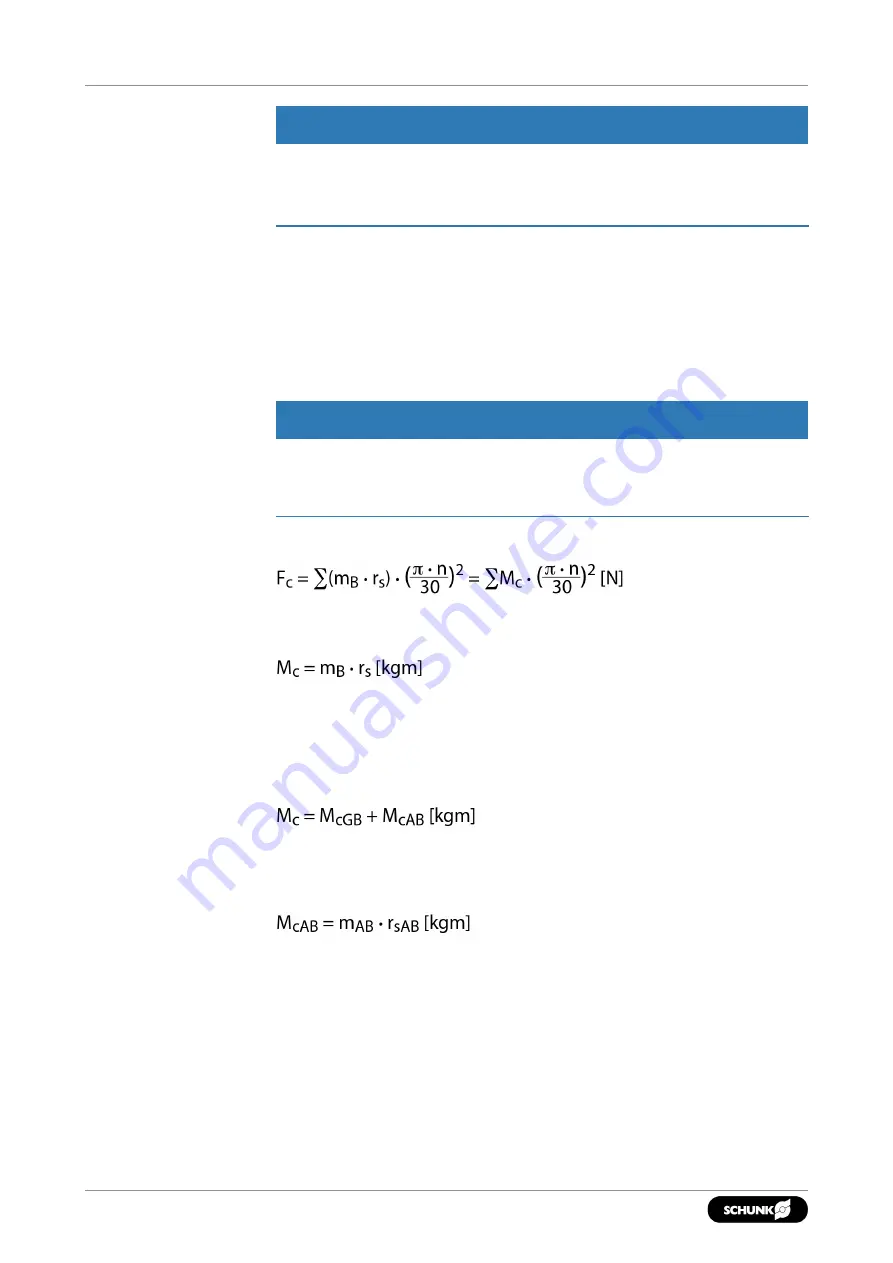
Technical data
26
01 | ROTA NCO2, ROTA NCO2-JA | Power Chuck | en | 1506425
CAUTION
This calculated force must not be larger than the maximum
clamping force ΣS engraved on the lathe chuck.
See also "Lathe chuck data" table
From the above formula it is evident that the sum of the effective
clamping force F
sp
and the total centrifugal force F
c
is multiplied by
the
safety factor for the clamping force S
sp
. According to VDI 3106,
the following also applies here:
S
sp
≥ 1.5.
The
total centrifugal force F
c
is dependent on both the sum of the
masses of all jaws and on the center of gravity radius and the
speed of rotation.
CAUTION
For safety reasons, in accordance with DIN EN 1550, the
centrifugal force may be a maximum of 67% of the initial
clamping force.
The formula for the calculation of the total centrifugal force F
c
is:
For this,
n is the given speed of rotation
in RPM. The product
m
B
∙
r
s
is referred to as the centrifugal torque M
c
.
In case of toolholders with split chuck jaws, i.e., with base jaws and
top jaws, for which the base jaws change their radial position only
by the stroke amount, the
centrifugal torque of the base jaws
M
cGB
and the
centrifugal torque of the top jaws M
cAB
need to be
added:
The centrifugal torque of the base jaws M
cGB
can be found in the
table "Lathe chuck data"
. The centrifugal torque of the
top jaws M
cAB
is calculated as per:
6.3.2 Calculation example: required initial clamping force for a given
speed
Required initial clamping force F
sp0
for a given RPM n
The following data is known for the machining job:
• Gripping from the outside in (application-specific)
• Machining force F
spz
= 3000 N (application-specific)
• max. RPM n
max
= 3200 RPM ("Lathe chuck data" table)
• RPM n = 1200 RPM (application-specific)