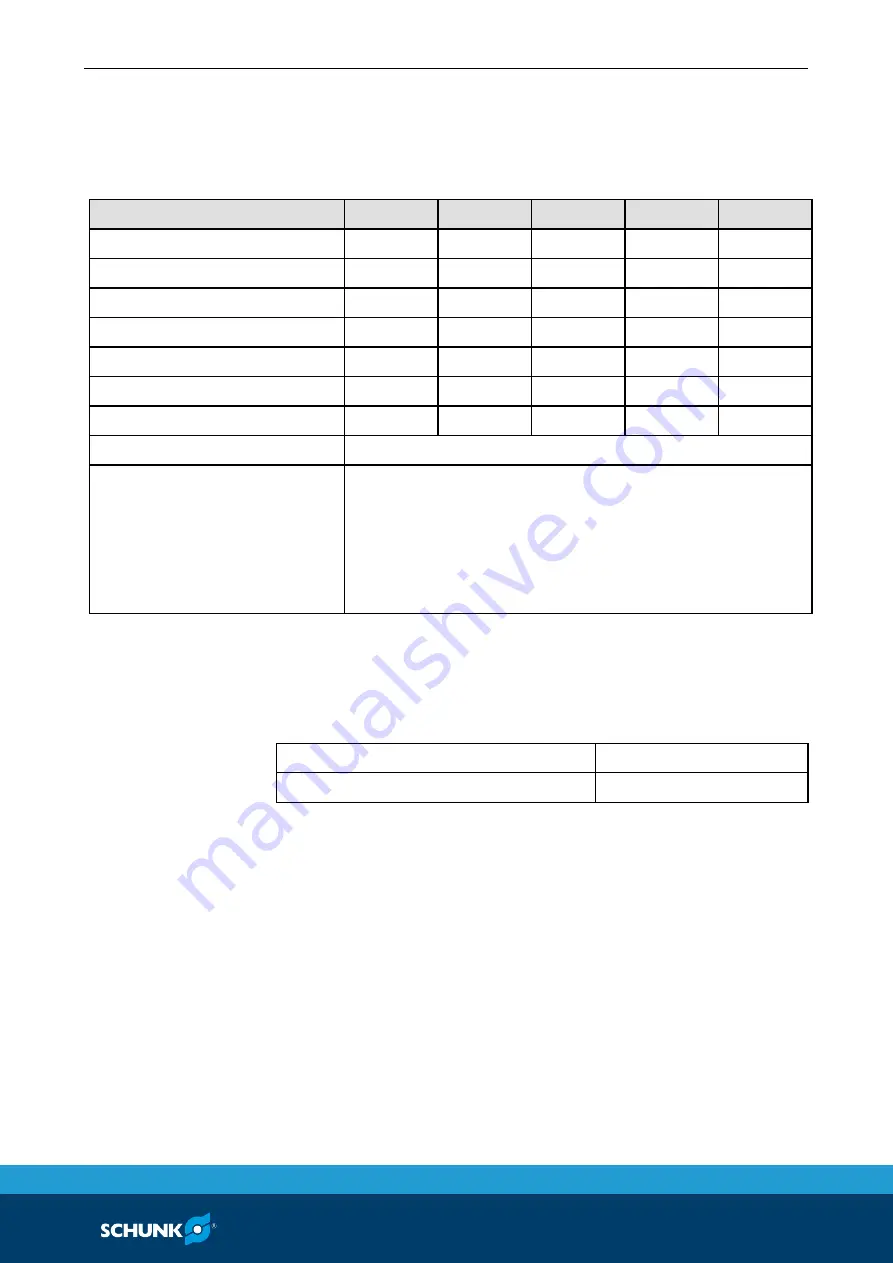
Technical data
01.00|ROTA THWplus |en
19
Technical data
Chuck data
ROTA THW plus
165-43
185-52
215-66
260-81
315-104
Max. actuating force [kN]
30
36
46
65
90
Max. clamping force [kN]
45
64
82
115
160
Max. rotation speed [min-1]
6000
5700
5400
4000
3600
Stroke per jaw [mm]
5.9
6.7
7.4
8.2
8.6
Piston stroke [mm]
20
23
25
28
28
Through hole [mm]
43
52
66
81
104
Weight [kg]
14
18
26
45
70
Operating temperature
15 - 60 °C
Centrifugal torque of the base
jaw with
fine serration
M
cGB
[kgm]
For the chuck THW plus it's necessary to determine those
data specific. Calculation examples are in the chapter
"Technology" in the SCHUNK-lathe-chuck-catalog or in the
chapter "Special jaws/Technology" in the SCHUNK-power-
chuck-catalog. Those catalogs are also available as down-
load at www.de.schunk.com.
The maximum permissible speed for special machining has to be
defined by the user on the basis of the required clamping forces.
This speed must not exceed the maximum speed of the chuck.
Warranty and maximum clamping cycles
Length of warranty
24 Months
Maximum clamping cycle number
500 000 Cycles
Ensure minimal weight for all jaws.
For unhardened top jaws or chuck jaws in special design, the per-
missible RPM according to VDI 3106 must be calculated for the re-
spective machining job. Whereby the recommended maximum
speed must not be exceeded. The values calculated must be
checked by means of dynamic measurement using a clamping
force tester.
Clamping force / speed diagrams
The diagrams refer to 3-jaw-chuck.
Clamping force/rpm curves have been determined by using hard
jaws. In the determination process, the maximum actuating force
6
6.1
6.2